AngryCorvair wrote:
Clay wrote:
All of the main team members had horrible GPA's but their job opportunities came from FSAE connections. It sure looked like fun though!
I've posted this tidbit before, but it bears repeating: when HR sees FSAE on resume, that resume goes to the top of the stack.
As an FSAE alum whose done college recruiting, I can confirm this.
mguar wrote:
unevolved wrote:
I think the reason the competition focuses on autocross is to keep costs down. These cars have a 610cc and 60" wheelbase limit, I can't imagine how much it would cost to stay competitive with a 2000cc, 80" wheelbase limit or something like that. At the speeds we're operating at now, the benefit of full-aero cars is debatable, if the cars were operating at road race speeds the cost would increase exponentially.
As far as Drexler, I'm not sure if there is one. I know our DT guys are interfacing directly with some people in Germany.
at sixty mph air is extremely powerful.. you'd be flying at nearly 1/2 that speed with wings..
there are some astonishingly light ways to gain aero benefits.. look to the ulta lite airplane crowd for those..
Want inspiration? look at what they did with that human powered airplane..
And thus begins the debate! Average on-course speeds for a FSAE course are around 35 mph. We're running an undertray this year, so we've actually got some CFD going on. Until you hit 45-50mph there's not a huge gain from aero. Our cars are very much in the "keep it simple, stupid" area of the design, and it's worked out well for us for the past few years.
That being said, there are some fun rumors floating around about next year's car.
Are there going to be any repeat team members between '12 and '13?
Not from the class this year, no. There are some incoming team members that have done the Challenge build for a while, though. Going to be interesting to see how that works.
Yeah, we cover the exposed surfaces of the car with Dacron for the same reasons. I'm not saying there's no merit to Aero, I'm saying we've got more benefit in spending an additional month testing than an additional month designing and building a full aero package. With a two-semester gestation period, time is a very finite resource.
We're huge fans of Aircraft Spruce. Every nut and bolt on the car is replaced with a NAS-6204 (Mil-Spec half-height head bolt for pure shear) or AN364 (half-height Nylock) to save a little bit of weight. With the amount of fasteners on this car, the weight adds up. If you worry about the ounces, the pounds take care of themselves.
I knew a guy who spent $10k on titanium fastners for his race car just to save 10-15 lbs.
Anyway, keep going... LOL
Every bolt that's in shear gets one of the half-height nuts... we'll use full-height nuts for tension applications unless there's a clearance issue and the stress in the bolt is small.
If you are really after weight savings, have the frame nickel plated. It weighs like 1/4 what paint or powdercoat does and looks cool. Should be good for a couple points on the final grade.
Aluminum bolts in non stressed areas are good and are cheap compared to Ti. Nylon can work also but they are easy to strip/shear. Also if you look around you can find drilled (hollow) bolts from dirt bikes to use for engine mounts, etc. Honda used to use them extensively in the Pro Link suspension pivots.
On shock mounts, make the brackets in double shear then use a hollow pin with a pair of snap rings to keep it in place. Like these:

Then machine a snap ring groove on either end. Much lighter than a bolt. That's an old motocross 'works' bike trick.
Curmudgeon wrote:
On shock mounts, make the brackets in double shear then use a hollow pin with a pair of snap rings to keep it in place. Like these:
Then machine a snap ring groove on either end. Much lighter than a bolt. That's an old motocross 'works' bike trick.
Fascinating idea. All the shock mounts are in double-shear, that could definitely work without changing anything in the design. I'll have to look into that if I ever get a chance, unfortunately I'm working on some other things at the moment and that's something that can be subbed in at the last minute.
Is nickle-plating really a cost-effective option? I thought he was being facetious suggesting that. I'm not familiar with the practical applications of that process. How much does it actually weigh? How durable is it?
The main reason I'm hesitant is how dirty it could become in a hurry. We keep our cars for a while for driver testing, and even a white chassis is annoying as hell to keep clean. We were planning on going with a gunmetal or black finish this year, plating is the exact opposite direction aesthetically speaking.
I've got some friends that work at the local airport, I'll have to ask them about Van Duesen. Thanks for the tip.
We have nickle plated LOADS of parts when I was in Odessa. The price was fairly cheap, but they were much smaller than the chassis. Though with the size of the tanks they had, it would fit. Prices on this are also very low.
The durability is not bad on it this is all oilfield equipment, which is not normally treated.......nicely, and the cleaning was fairly easy, though to do a chassis like that, the crevasses would be bad.
Now, this was done for the "durability" of product. The wells had corrosive natures to them and we needed the nickel coat to try to alleviate any sort of corrosion to the part. I say this because it was not a bright finish, though we never attempted to polish it. The thickness of the coating is in mils to. So the weight is fairly negligible. I cannot say for certain, but I would suspect that the difference in weight from a coating to paint would be nil.
Drop me a line and I can at least get you contacts out there if nothing more than information and possible pricing as a basis.
When trimming weight on R/C cars, some guys would use translucent paint in very thin layers only because the rules for most classes said the polycarbonate bodies could not be left clear. It was a very real weight savings!
Ever weigh a gallon, or even half gallon, of paint?
Sure it contains solvent which evaporates, in most cases that's ~40% of the weight, but when you are doing anything to save weight (as mguar says watch the ounces and the pounds take care of themselves) nickel plating is a very real weight saving option. It's also non porous, which is why it's done under chrome (which is porous). Powder coat has no solvent (or at least a very small amount) so what you spray is very close to what the weight winds up being.
Unpolished nickel plating:

Polished nickel plated motorcycle frame:
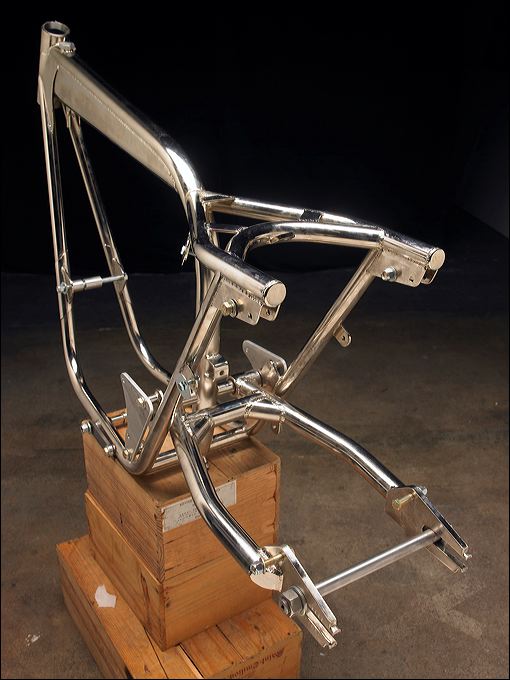
IIRC nickel can also have other metals, such as cobalt, added to change its color.
Did you ever have trouble with hydrogen embrittlement, especially with welded parts? I suppose we could have the whole thing baked afterwards and while it's at the heat treat shop have it all hardened, but that might cause scheduling problems. "Where's the frame? We need to figure out where the surge tank goes" but this year should be better than last for avoiding that sort of problems.
As for the weight of the paint, I think you could figure out when a component was last added or moved on '11 by carefully sanding and counting the different layers of paint!
According to the Internets, the baking process to minimize hydrogen embrittlement has to begin within 4 hours of the acid dip so it shouldn't cause much of a scheduling blip.
I was thinking about the Dacron bodywork thing. Another possible approach for that: RC airplanes are made by putting a heat shrink wrap over balsa and then going over that with an iron or hot air gun. The resulting airframe is very light weight. Maybe that's a possibility for covering stuff in a very lightweight manner? or even making lightweight aero aids? They might be a bit fragile, though. Quick tutorial: http://www.rc-airplane-advisor.com/heat-shrink-covering.html
Yeah, I used to do a lot of model airplanes when I was younger (just got a nice nostalgia blast... Monokote, Ultrakote...) but that stuff is really fragile. I can't imagine it would hold up for very long.
So say we decide to nickel plate the chassis. What about repairs/touchups down the road? Wouldn't we just be SOL to get an exact match to the chassis if we ever had to repair or replace something that required welding?
unevolved wrote:
There's a reason our team has been back at school since Jan. 2 working in the labs, and it's not for all the hot chicks running around the engine lab.
And where are the pix of this event taking place?
unevolved wrote:
So say we decide to nickel plate the chassis. What about repairs/touchups down the road? Wouldn't we just be SOL to get an exact match to the chassis if we ever had to repair or replace something that required welding?
Grind, weld, clean up with wire brush, rattle can that spot clear.
Not perfect, but good enough probably.
Showing off FSAE huh?
here is Oakland's '10 and '11 cars at the auto show in Detroit.
I was at the show all day yesterday and will be back tomorrow for the charity preview. Come by and check out our cars if you are heading down, we are in the lobby out front, you wouldn't even need to buy a ticket to see em.
The '11 car competed at MIS and took 11th at FSAE west. We competed at the U of T shootout at Mosport too. Any of the Detroit region SCCA and AROC folks should recognize our cars as well. We've been running em at every event we can get to. We have over 100 autocross runs, a few FTDs and (since very few local schools actually bring their cars out) a nother SCCA solo FSAE class win in the Detroit region. I'll get some build pics up of the '12 car later but I gotta get back to welding, chassis is almost done :D
Conquest351- They're coming. I've spent the past week or so in the computer lab working on some drawings, but I was in the engine lab until 6AM or so working on jigging up the chassis. Here's a quick cell phone shot until I get some better ones from higher up with a better camera-

DILYSI Dave- Thanks. I'm not sure if we'll be going with nickel plating this year, We've had our hearts set on a gunmetal/black chassis for a while now. While it's definitely a viable option for FSAE, I don't think we'll be doing it this year.
RXBeetle- Those are pretty sexy. What competitions are you guys going to this year? Sounds like you're farther ahead than we are at this point. We just started jigging last night, but we should be off the jigs within a week or two.
One issue with nickle/chrome/galvanized type coatings is the fact that submerged tubes probably will pick up fluid and could wind up not giving it back. You have to be sure that the chassis is either 100% liquid tight or will drain well. I'm not sure how those coating do for spotting cracks down the road either. We always just lightly painted our chassis as ease of touchup and repair was worth more than Bling-bling
A closed tube can be a problem if the air inside expands enough, the hot metal weld puddle will bubble and spit as the air tries to find its way out. The fix is to drill a 1/8" hole to release the pressure. If it needs to be airtight after the part is completed, weld the hole shut. Otherwise, leave it open so condensation can get out, that slows down rust formation inside.
How do you guys control twist in the chassis caused by the welding?