The short of it is I am putting a MS in my 924s. I got a bad DME and gutted it so all I have left is the plug and the flat spade connectors that use to go to the board. I am going to now wire the MS to these pins making the install virtual P&P.
My question is do I want to make these connections with crimp connectors or should I make them solder connectors. I could also do a hybrid and solder on male and female spade connectors and then plugging things together
I also thought of using different size and type spade connectors for the various types of systems. 1st type for the grounds, 2nd type for the power, third for the sensors, a 4th type for the ignition and a 5th type for the injectors. This way there is less of a chance of screwing things up if it has to come apart.
So what would you do and why?
My ms thread with photos if you want to read my progress
http://clarks-garage.com/phpBB2/viewtopic.php?t=8338
I prefer solder, but PLEASE use solder that contains lead. Lead free solder will crack from the vibrations likely seen in an automotive environment, leading to failed connections. This comes from experience in RoHS and OCXOs used in helicopter applications. More extreme vibration, but I wouldn't chance it. Use the solder that isn't lead free.
Here's my opinion (having been a professional Radio Electronics Officer in the U.S. Merchant Marine (RIP), and having 3 Megasquirted vehicles): The home mechanic can make a good soldered connection and a bad crimped one. The professional with $1K tools can make a crimped connection that may be better than the home mechanic's soldered connection.
Crimp to get it running, solder once you know its right.
For connectors do some searching for terminal ends and weatherpack connector bodies. Do it once, do it right.
If you buy the weatherpack connectors, terminals and crimping tool, you're set. The right tool, your crimped conections will be better than a soldered joint.
Whenever you solder something, you need a good mechanical connection FIRST. I tightly twist the wires together end to end and heat the wire enough to wick up the solder. I haven't had a single failure yet.
I have a series of flat metal tangs about 1/16" wide that come out of the back of the plug in the DME case. I was thinking of crimping spade connectors on to them and soldering them in place. I would then crimp and solder the corresponding spade connector on the wires making things changeable. When I have it all up an running I can run over the spade connectors and solder them permanently and shrink wrap them.
I do agree about having a good crimp. It is a must!!!! a vice grip really is not a good substitute no matter how hard you try. 
I will try to post up a photo of the inside of the DME. It may help explain what I am doing.
Solder connections should always be stress relieved with heat shrink.
If you have good crimpers (not the cheap and sleazy masher type) then it's hard to go wrong with this style of butt connector: http://www.napaonline.com/Search/Detail.aspx?R=NW_725339_0063685264
It's all I ever use anymore.
PS - I can tell you what won't work. Had a C4 come in that was modified all to hell and back by some shop in Texas. It had Accel DFI, which we have some experience with. When it got hot, it would quit running. We ended up pulling the TPI plenum and found that the fuel injectors were just twisted and taped - with duct tape. Duct tape that got conductive when heated.
kb58
Reader
9/21/10 10:48 p.m.
I'm an EE and work in aerospace.
Almost any soldered joint will last forever if there's no vibration - that's the key. The solder itself isn't what fails, it's the interface point between the copper wire and solder, that's where the wires - not the solder - fail. Always use shrink sleeving, and always restrain the wire mechanically so it can't work-harden itself to death.
And yes, with the proper crimp tool, a crimped connection is always better than soldered, and yes the right tooling is expensive. The AMP hand-crimper alone is about $400, never mind the dies.
Derick Freese wrote:
Whenever you solder something, you need a good mechanical connection FIRST. I tightly twist the wires together end to end and heat the wire enough to wick up the solder. I haven't had a single failure yet.
That's because you're doing it the right way.
What you're after is called a "Western Union splice". It's normally for solid wire but when you do it with stranded wire and solder it, you'll almost never have a problem.
Shawn
ddavidv
SuperDork
9/22/10 5:14 a.m.
I'm no wiring guru but since I've been using just halfway cheap, but job specific, crimping tools I've not had a failure. The same can't be said of my soldered work. I no longer solder, unless it's for really small wiring connections (non-automotive, mostly).
peter
New Reader
9/22/10 6:16 a.m.
I prefer to solder, but just for kicks, can someone like to the "professional" level crimp tools/dies/connectors that make worthy crimps?
In reply to dean1484:
My company makes (amongst other things) wiring harnesses for heavy duty off road vehicles that see massive amounts of vibration. We used to solder all connections, and still do with some connections, but over time we have found that a proper crimped connection (meaning a good quality terminal and crimp) holds up over time just fine. When subjected to elements, we shrink sleeve connections, soldered or crimped. Based on our testing and experience, I almost never solder a connection on my own cars. That said, if you are going to err, err on the side or overkill.
Solder and strain relief. Use shrink tubing over it and if there are wire-to-wire joints in the middle of your harness, wrap the whole harness tightly in that area and try to mount it to something to keep vibration to a minimum.
Oh... and if you are not a skilled solderer, practice a little first. A cold joint will fail. Tin the wire first, mate (twist/crimp/etc) and then heat the wire or post to accept the solder. It should draw it in - never heat the solder onto a joint. Always try to place the iron under the work - heat rises. Use leaded solder and don't lick your fingers or breathe too much smoke ;)
I prefer a soldered connection and as noted the idea is to heat the wire until the solder is drawn into the joint. Heat shrink is teh shizznit, for wet locations it's a good idea to put some dielectric grease on the soldered connection before heat shrinking it. That will keep water out and reduce the chances of corrosion.
On crimed connections, the #1 thing I see wrong with the usual butt splice is that the splice ID is way too big for the wire, making it difficult to get a really good mechanical connection unless you really squash it. In most cases, I find that 22/18 splices will work well on 16/14 gauge wire. The insulated butts are nearly impossible to weatherseal properly, so I use uninsulated ones, then heat shrink same as a soldered joint. But even this sometimes does not work properly, as I recently found out with the splices on the leading coil for the Jensenator. 
On really small wires like that used in newer harnesses (meaning early 90's and up), Radio Shack has butt splices meant for telephone wire which are a perfect size.
I'd solder that and use heat shrink over the joint and onto the wire. I'll crimp like a speaker terminal- actually, I usually solder them too- but anything on the car I solder.
Are you splicing wires, or making completely new leads???
IF you are splicing....
crimp it or solder it..... that is up to the builders confidence.
get the correct shink tube and which ever splice you choose make it stronger, and fully sealed.
The above product is Thermafix shrink tubing.... The reason I recommend it over others... it is adhesive lined. Once set this is how it looks....
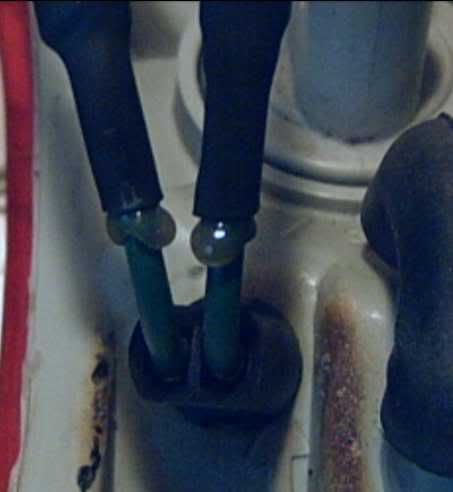
the adhesive has fully sealed the splice - NOTHING can get in there to degrade which ever fastener choice you finally decide on
I think it's easier to make a bad crimp joint than a bad solder joint. Just know what a cold solder joint is, and don't make any.
I've used both, but I prefer solder and heat-shrink tubing.
The home mechanic can easily make bad soldered connections too! We see a lot more bad soldered connections when troubleshooting, mostly due to vibration. I use insulated crimp connectors with heat shrink housings and a good crimping tool - not $400, just a ratcheting one with interchangeable jaws. Works well. Definitely not as pretty as solder, but the fact that there are NO solder joints from the factory in a Miata tells me something...
Keith wrote:
The home mechanic can easily make bad soldered connections too! We see a lot more bad soldered connections when troubleshooting, mostly due to vibration. I use insulated crimp connectors with heat shrink housings and a good crimping tool - not $400, just a ratcheting one with interchangeable jaws. Works well. Definitely not as pretty as solder, but the fact that there are NO solder joints from the factory in a Miata tells me something...
Nice to have agreement from someone else that does this type of work a lot. 
I smell a GRM article here 
Paid ~$50 for a nice ratcheting crimping tool, and I haven't used a soldered joint in any of my cars since I bought it about 8 years ago. The one I have will do three sizes, and I always tug-test them after crimping. VERY Rarely will they pull out. Also, its quicker and easier than soldering, and less burn-ey. Ever drop a nice hot blob of solder onto your carpet or seats? Ick. No thanks.
As a side note, I threw away and gave up on Scotch locks about the same time as I bought my crimper. Don't ever use them. If I need to join three wires, I use a wire nut, or a butt splice.
I work aviation also. I have done both solder and crimp. Crimp can be better than solder if using a quality crimp done right. That said, it depends on where it is for me if I solder or crimp. And good heat shrink over whatever method you use and proper support to reduce vibration issues.
Manufacturers seem to frown upon soldering nowadays. I work at a VW dealership and VW requires us to crimp all our connections when we do wiring work. They published a training article at some point showing the weakness of most soldering compared to crimping and it was pretty convincing. I honestly prefer crimping anyways, it can be pretty easy and quick once you start doing it a lot. But I'm sure in most instances you could make either one work. To make it truly "plug-and-play" could you get some pins and put a connector in there so it can be removed by just unhooking the connector?
Keith wrote:
We see a lot more bad soldered connections when troubleshooting, mostly due to vibration.
Interesting. I wouldn't have guessed. Is part of that from not leaving enough slack? I've never had a failure of a solder joint, but have had crimp connections fail. But I don't have a snazzy crimp tool.
What breaks? The wire or the solder joing? I have seen where people go kinda nutty with the solder heating the connection so much is sucks solder down into the wire. I could see that making things kind of brittle. Still hard to imagine it breaking. Huh.