so I've built my trans cross member for the volvo/s10 build
in order to fit enough rubber for the mount and control the angle I ended up cutting a good bit of the member...

then I welded a plate to it... I also welded 2 "U" shaped plates to cap the sides and give the plate more support

yes my welds are ugly... and I ran out of wire on the one end plate... lol

I drilled a hole in the plate for the mount bolt... on the bottom I plan to drill and weld a short bit of pipe on the bottom to access/install the nut...
now I say all this because someone mentioned the cross member strength... is that really a concern... the tubing used is pretty stinking thick (not quite 1/4")... do I need to worry about strength? I could weld some material over the back 1/4 and not interfere with the mount... but no point if it's not going to need the added strength
Taiden
Dork
10/29/11 11:09 p.m.
FCAW? Man. That's my least favorite form of welding. More power to you.
Cutting it like this \ .........../ is better than like this |...........|
Also you can cut out <> shaped steel from thick plate and stitch weld them to the back side to give it support.
Finally you can support it with some C channel or erw pipe split down the middle.
Just get creative I spose
you could also fill the tubing with structural foam (not "great stuff," but the high-density, high-strength stuff that is super-messy to use).
ya flux core wire feed crap... never messed with anything else... I hope to go real MIG next time I have a real project... cleaning up after flux sux lol... add to it piss poor welding skills and it's even worse lol...
in reality... do I need to worry?... my gut says no way... but I tend to 2nd guess myself.
Taiden wrote:
Cutting it like this \\ .........../ is better than like this |...........|
assume you are talking about beveling the edges right?... I got side tracked because my first plan didn't work out
Taiden
Dork
10/30/11 8:57 a.m.
no I mean the whole cut, but you're beyond that. That was more of a
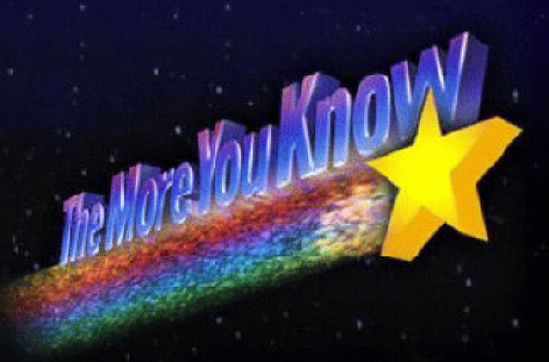
My personal, non professional, opinion is:
I would brace it. I mean, why not? It's already out of the car. If the crossmember would have fit the design requirements and be half the original width, it would be such due to more profits from cost cutting. But there is safety factor in all parts (unless VW electrical system har har har) so perhaps you are still within 'acceptable' limits. Hard to know really, but I would give it a little extra help while you can.
But a larger issue to me than support is that place where you over shot with the cut off wheel. My gut feeling is that if a crack is going to form it will be there. Take a 1/8" drill bit to the end of all these places and weld them up would be my personal plan of attack.
But welding is one of those things where they are just as many right ways to do something as wrong ways.
I suppose if you're really curious you could go to your local good library and check out ASM volume 6 and neighboring volumes.
Get rid of that 90 degree angle! You have a nice stress concentration there.Take a piece of piped and cutting it to fit will help. (you will have a nice curve) Curves are your friends. Next is triangles.
Taiden did a good job on his explanation
I'd weld two rib on to the sides that extend down at least twice the depth of the cut, and three times as wide. Remember your strenght comes from vertical depth.
Just weld in a piece of tube of about equal diameter, shaped the same as the cross member, ahead or behind wherever is best fit. Weld a couple of flat pieces between the cross member and stiffener tube at the ends, Maybe even find another of the same cross member and cut the ends off.
I'd run it as built. It looks plenty strong to me unless you running big HP. I'm thinking your cross member is at least as stronger than the bolt holding the mount in place.
Taiden
Dork
10/30/11 3:03 p.m.
I thought modern vehicles tied most of the front suspension through the lower front crossmember.
I don't see an issue with it supporting the engine.
It's all the other stuff I'd be concerned with.
I lean toward 44's idea, I'd rather err on the side of too strong.
You guys think too much. It's fine as-is.
Yeah, its probably fine. I bet the chassis is more flexy now, but you probably wouldn't notice that with out decent amounts of seat time before and after and some sticky tires :P
I will say though, in bending most of the load is carried in the outer most parts of the member (top and bottom, not radially). The inside of the curve compresses, the outside is stretched and the material in between is in between... :P
That means the material in the middle (well, not always the middle depending on cross section) carries almost no load, some of it literally no load (as far as bending is concerned). Your patch piece is pretty damn centered... It is a thick piece but I am betting you still made the thing much more flexible.
And that 90 is pretty bad, if you can gusset that it will help.
I did something similar on a BBC engined Nova with raised exhaust ports. Thanks to the raised ports, the headers would not clear the crossmember anymore. Relocating the trans mount down was far preferable to notching for header clearance for several reasons.

No idea on the power of the thing, but it was a 540 with heads that could flow like wind tunnels and a cam in the 270@.050 range, so, um... a lot?
The trans crossmember shouldn't really see any stresses anyway. The torque is resisted by the motor mounts, the trans mount just holds the end of the trans up.
Taiden
Dork
10/31/11 8:24 a.m.
Oh. Hahaha. Foot in mouth. I thought that was your front crossmember.
I'd still brace it a little while it's out, but it's not as critical as your front xmember.