Tires, springs, shock absorbers and anti-roll bars get a lot of attention, but what about those unassuming bushings–you know, the little blocks of rubber tasked with locating all those suspension components day in and day out? Perhaps it’s time to think about them.
Just about every mass-produced car has been delivered with rubber bushings. Rubber does a fine job of …
Read the rest of the story
Next step: Spherical bearings and rod ends. :-)
The reason for staying with rubber is that the solid bushes (poly, Delrin etc.) rotate in the suspension components, need some sort of lubrication, and wear themselves as well as the suspension bits they run in. The rubber don't move, they just flex (and of course eventually wear out that way)
The reason for not staying with the old style rubber bushes is that it seems that it is becoming more and more difficult to source decent rubber today. In the old British car world, much (most?) of the rubber bushes come from China or India and while one batch may be great the next may be crapola. Owners are finding that they are changing them again after less than a year on the car when the OEM bushes would last years.
The market is strange - I would gladly pay 3 or 4 times as much for bushes that would last a long time or chrome bits that didn't need to be stripped and rechromed out of the box if they are to last any time at all, but the vendors tell me that people opt for the cheapest part (and then bitch when they get what the paid for). (Hint to MG owners - never use anything but the MGB V8 'metalastic' bonded rubber/steel bushes - they still seem to last well).
Given that, I think that the solid bushes will gain a following, as they offer both bragging rights and reasonable longevity (haven't seen any complaints about the solid bush quality control, but maybe I haven't noticed). Just remember that bushes like that don't make their wear noticeable until it is great enough that it may also require replacement of some suspension bits (I am assuming that no one ever checks anything under their car that doesn't make noise).
I've never had poly suspension bushings create an objectionable amount of NVH. But in my experience they wear out much quicker :(
Unfortunately, for many vehicles, replacing the rubber bushings is nearly impossible, or stupid expensive, or NLA.
Polyurethane bushings are often misapplied. It's not NVH, it's the fact that it takes a 20 ton press to get the OE bushing out, and then you can just push a greased up poly bushing in by hand? There is a lot of slop there with poly bushings. They float around on-center and then the take-up is abrupt because they're less compressible than rubber when corner loads build.
If a suspension component moves through more than one plane in it's travels, don't put a polyurethane bushing in it. They're not good in control arms and trailing arms.
Just because it's aftermarket and it's red doesn't mean it's an upgrade.
Tyler H (Forum Supporter) said:
Polyurethane bushings are often misapplied. It's not NVH, it's the fact that it takes a 20 ton press to get the OE bushing out, and then you can just push a greased up poly bushing in by hand? There is a lot of slop there with poly bushings. They float around on-center and then the take-up is abrupt because they're less compressible than rubber when corner loads build.
If a suspension component moves through more than one plane in it's travels, don't put a polyurethane bushing in it. They're not good in control arms and trailing arms.
Just because it's aftermarket and it's red doesn't mean it's an upgrade.
If the replacement bushing isn't precisely the correct size doesn't that suggest a manufacturing or design issue? I'm fortunate enough that I was able to replace my stock, void filled control arm bushings with solid rubber bushings from a performance model from the same manufacturer. The new bushing was rubber encased in a metal sleeve and with some grease it went in so easily I could have pushed it in by hand (I used a hammer and a block of wood).
Regarding trailing arms.... I don't see why a poly bushing with a metal sleeve through the center and washers on the outside can't work. No twisting forces would be applied to the poly because of the sleeve.
I answered my question by installing the parts (poly bushings in trailing arms). There's zero noise from the poly bushings because there's no actual friction between the bushing and anything else; the bushing exists to fill a void. Just as with the stock rubber piece that was there, there's a metal insert within the bushing that the bolt goes through to secure the arm to the chassis; so it's metal to metal contact.
Handling is improved more than I thought possible; conceptually I understood that toe deflection at the rear would impact how the car turns, but the most noticeable change is how much steering accuracy and response is improved.
I'd have been perfectly happy to use solid rubber instead, but as far as I can tell this isn't a thing that exists.
In reply to MrFancypants :
Definitely agree on the steering improvements. I replaced every single bushing on my R53 Mini with poly bushings and any other wear point (ball joints, tie rods, endlinks, etc.), and the biggest difference I noticed was the steering. The rest of the handling and ride didn't really seem to change much, though.
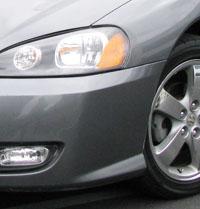
Some of these comments in this article are Good, Bad & just downright Ugly.
I have worked with Energy Suspension for 12 years and now with PROTHANE for 6 years, so I know what I am talking about.
Companies that manufacture performance urethane/polyurethane vehicle suspension bushings exist for several reasons: 1)- to make some money & provide jobs 2)- to provide an alternative to rubber bushings that often wear out soon 3)- to supply automotive enthusiasts with an improvement in bushing and suspension motion control. The last one is really important to GRM readers! Not all bushings and producers are the same as far as proper engineering of the products. Just as that there are good vehicles out there and there are bad. Most of these urethane/polyurethane companies recognize the need for firmer durometer bushings to really help with maintaining important alignment settings under high G-forces enthusiasts demand (motion control). And, there are many, many levels of durometer firmness bushings, specifically chosen for the location of the suspension that these companies select. Two examples: Sway bar end links are the firmest, to improve vehicle roll control enthusiasts demand. On the other hand- tie rod boots are very soft, to hold in rod grease. Other areas of the suspension get different durometer bushings and mounts, such as motor mounts, trans., drivetrain, etc. And on and on. Properly installed, and many times easier to do so than stock rubber replacements, they will not squeak. Use the grease that come with the bushings! Don’t forget, for the most part, professional race cars employ metal & hard bushings to maintain control. Way too much for street use.
Thank you!
In the true GRM spirit of things, what prevents the budget conscious (challenge or similar) builder from taking a stock bushing with rubber surrounding a steel sleeve, cutting out the rubber, and replacing it with polyurethane? Wouldn't that mostly accomplish the same thing as buying a premade poly bushing?
I know this is done to engine mounts all the time but wouldn't it accomplish the same thing in bushings?
*note: I actually tried this on front lower control arm bushings but without cutting out the rubber. It doesn't work. The movement of the bushing just pushes the poly right out. But in theory if all the rubber was cut out the poly couldn't be pushed out; it would be larger at both ends than in the middle.
In reply to David S. Wallens :
Rubber is fine for the street. But my solution for the race track is to use the odds and ends of aluminum. Cut it in half. Drill a hole at the split line just a tiny bit smaller than the bar. If you don't have a ream the right size wrap a piece of emery paper around the bar and slowly work it to the exact diameter. Then on either side of the bar drill holes to match the bolt pattern of the sway bar mount. One final task, drill a tiny hole to push grease around the bar and put a grease nipple in to grease the bar.
re-drill it bigger or make another set.
Mounts made this way will take stock bars or big tubular racing sway bars.