Hey everyone, fairly new to the forum. Since I've had a little more free time on my hands, I've been working on setting up my suspension to get my car setting on the ground to start aligning. I'm working with the front suspension at the moment and running into some limiting factors that are throwing me for a loop and I'm looking to get some good input.
I started squaring up my front suspension to the chassis last month and got that all done. Then I started figuring out my lower control arm angles and started realizing that if I have my lower control arms parallel to the ground, or slightly angled, the ride height seemed to be all wrong. With the chassis at the ride height that I want, the lower control arm is at a fairly large angle. I did everything I could to get the control arm adjusted into the highest slot in the chassis and I ordered the tallest ball joint I could find for the application and the lower control arm angle is still pretty steep. Is this normal for a setup like this? I realize that I could have a set of spindles made, but the lower ball joint is already close to the wheel and tire as it is, so that doesn't seem like a good option. On a double wishbone suspenion, is it ok to run a large lower control arm angle as long as you compensate with the upper control arms? I realize that will screw the camber curve, but I can work around that.
I'm sure I'm forgetting some info, but that seems like a good start to the post. Thanks for any help and here's some pics!
Car is sitting a little low, but close to the ride height I'm looking for
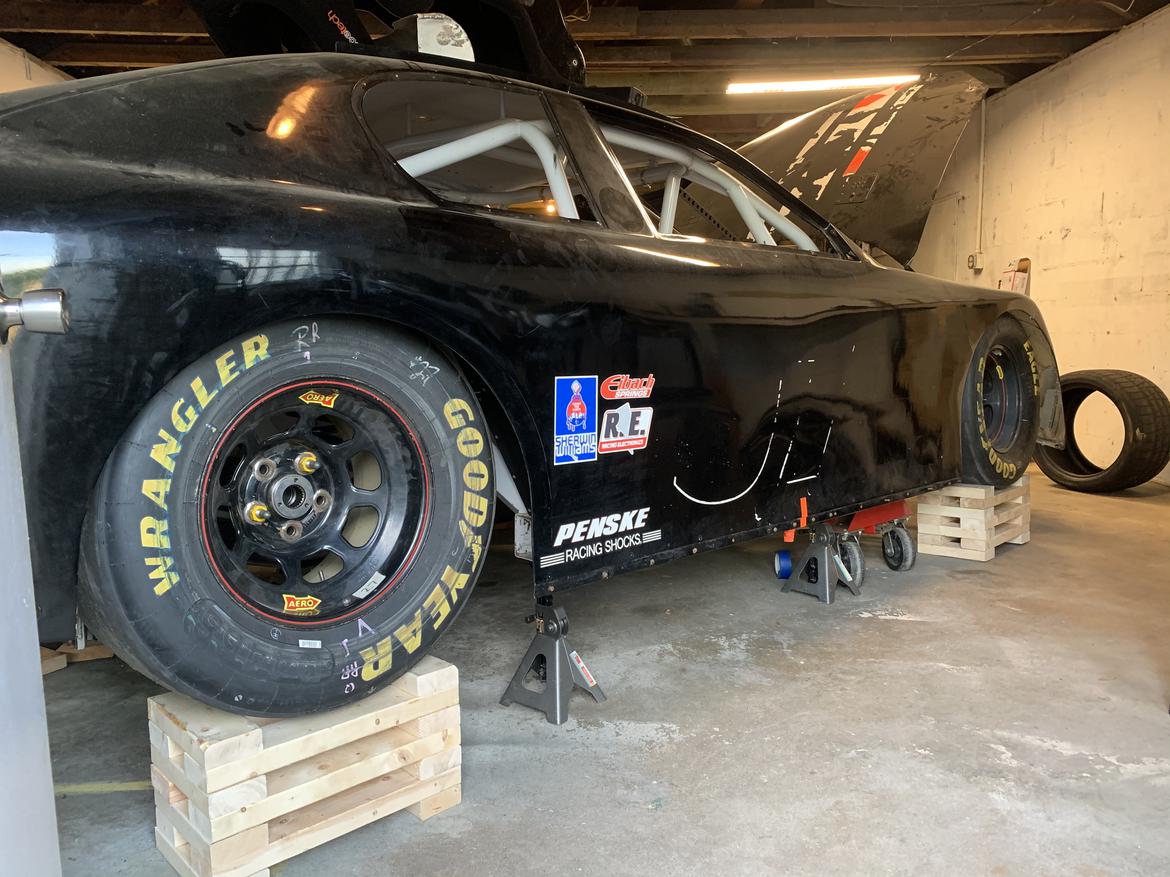
Angle of lower control arm angle close to ride height. Angled a couple degrees down
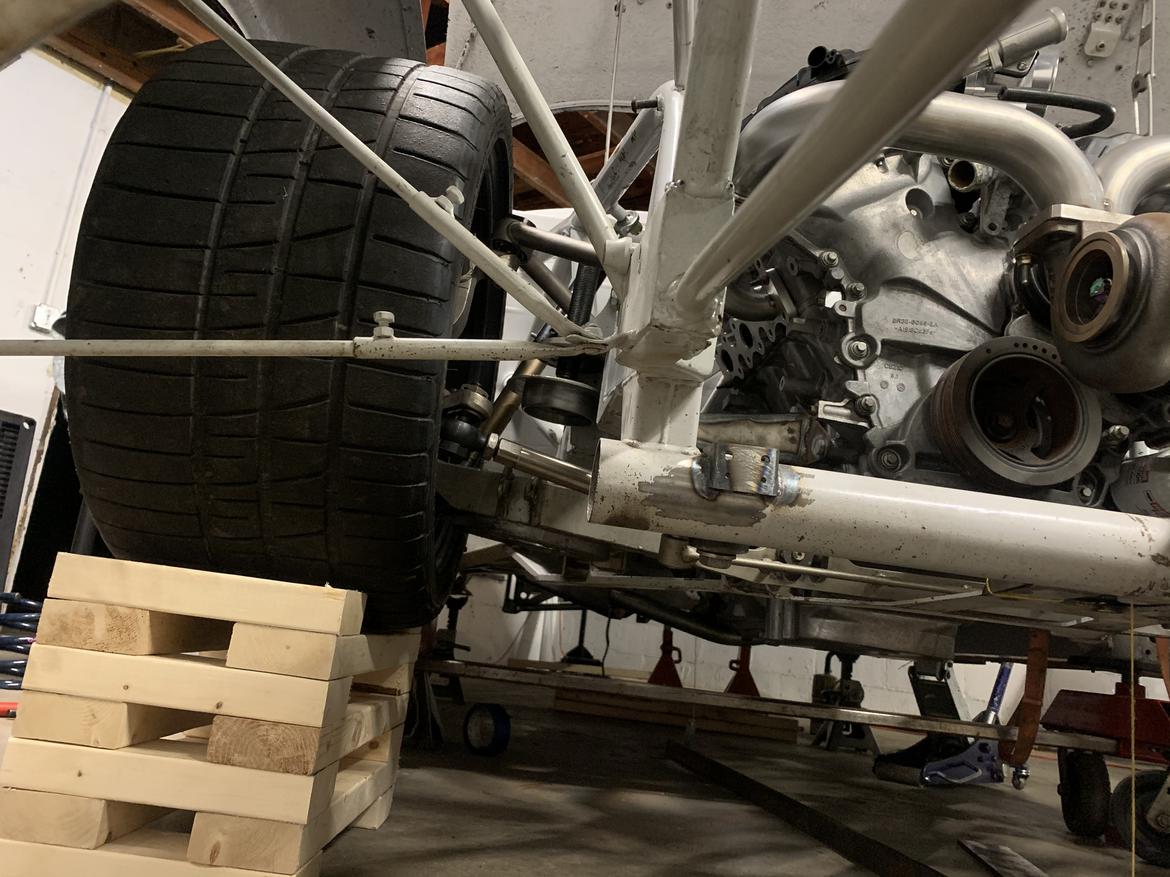
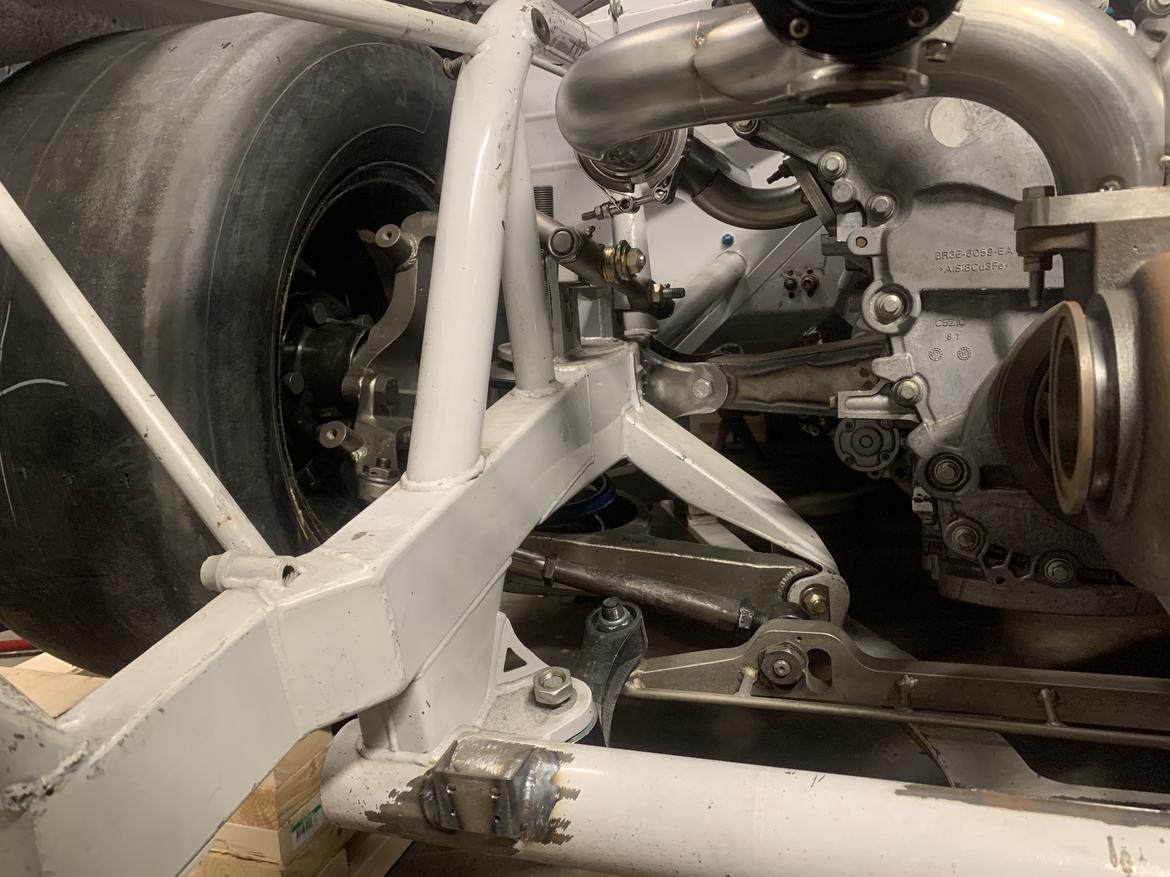
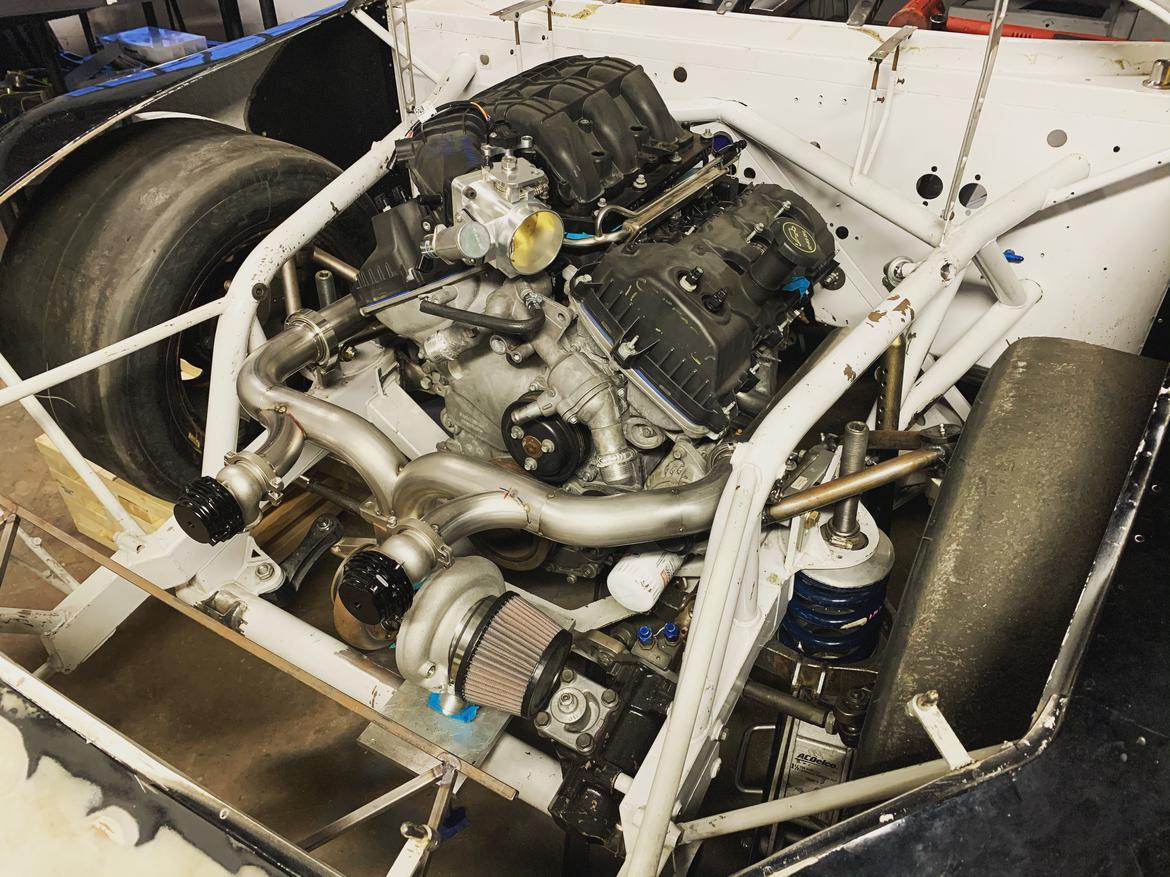
First of all, that car looks awesome. Always like seeing old stock cars converted to road racing.
For context, the geometry on a stock car (I'm using "stock car" in the NASCAR roundy-round sense) is, objectively, terrible. NASCAR tightly controls the locations of suspension pickup points, with a heavy, heavy emphasis on legacy designs. I don't know what that car's specific history is, but odds are good it was influenced by the NASCAR rule book in some capacity. So for your question of "is this normal?" the answer is sort of "yes, but it doesn't have to be." Odds are good you'd want to raise the inboard pickup points a good bit to reduce the angle of the LCA, but that's a large undertaking. Modern cup cars have a few Z-heights for the inboard LCA pickup points, as well as slugs to adjust the lateral position of the ball joints. I can't speak to exact alignments you want to chase since I'm more on the design/analysis side of things than the race engineering side, but you should have a lot more freedom in that regard anyways.
Out of curiosity, what's going on in the rear? Please tell me you got rid of the truck arms. 
Wow, that's great information, thanks a ton! And thanks for the compliment on the car! This thing is a huge project, but something I'm having a lot of fun with and learning. That's kind of what I figured with the front suspension. I have the LCA mounts as far up as possible and then I adjusted the rear slugs to get me the same anti dive angle from side to side. I was actually surprised that i was able to get the control arms square to the chassis on the first try. I made some nice little plumb bob tools to measure everything!
Nope! Kept the truck arms haha. I've never actually driven one of these cars except for in a parking lot and I wanted to get the full experience!
This was before I owned it
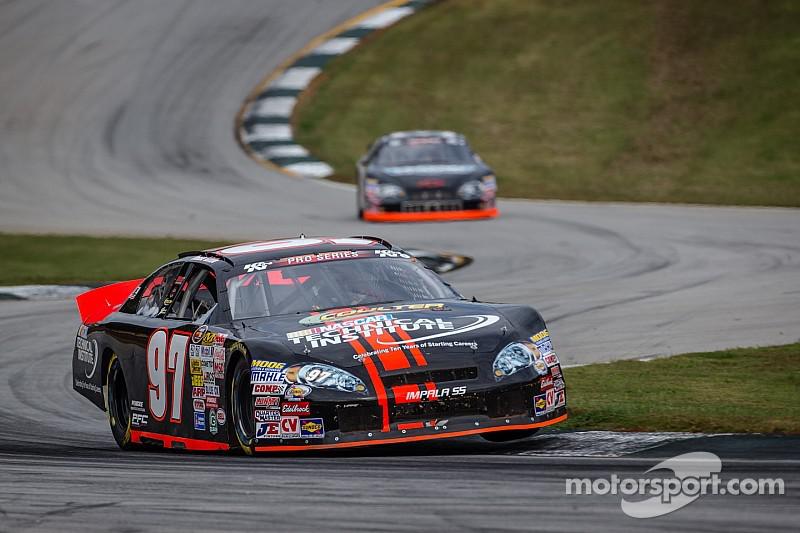
Also, I didn't mention, but I'm planning on running a "street tire" on this and running with some of the pro touring cars, even though it's not really legal for the classes
haha
fomoco01 said:
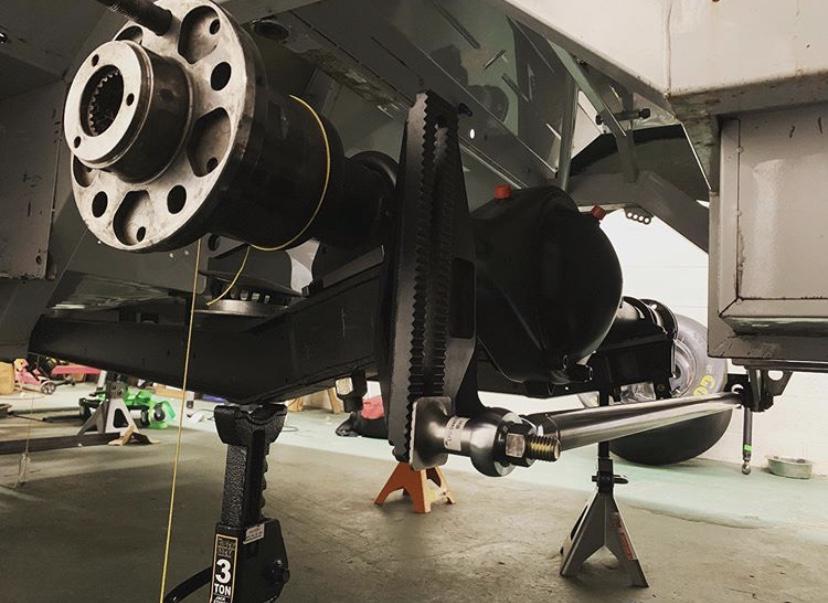
Do the axle saddles have one pin? Looking at that track bar mount, I would try and run as little standoff as you can, clearance-wise. The rear end on a stock car, for a non road course setup, is designed to laterally flex under load for kinematic and aerodynamic reasons. You're going to be fighting that on this car, I'd bet. Given that it's a K&N car, they may not have had road course AND oval truck arms, that adjustment slot on the TB mount looks longer than it needs to be- I don't know of any road course setups that run a high track bar, they're usually lower than the top of the truck arm I-beam. That longer slot is going to allow more lateral movement under load. I'd also recommend running some braces from the bottom of the U-bolt nuts to the center of the axle housing; those truck arms are going to try and twist under load.
I'm not sure what used prices are like, but a road course truck arm would have a stiffer left side track bar mount and help get rid of some of that deflection. Someone like SRI here in Mooresville may have an idea.
I'd really consider running a three link. Truck arms are inherently overconstrained, at best you can make them not suck. A general rule for engineering decisions on NASCAR racecars is "the right way isn't legal, so we've got to brute force the wrong way."
Looking at the front it looks like your Virtual Swing arm (VSAL) is about .75* the track width, and your Instant center appears to be underground. Your roll center in the front is likely at ground level and with those short of VSAL will tend to make it move around laterally a lot if the suspension is allowed to move at all. The other thing Short VSAL tends to do is cause a lot of camber gain/changes in bump/droop.
I wouldn't worry to much about the lower A-arm but would attempt to raise the innner ball joint on the upper A-arm. This will lengthen you VSAL which will reduce camber change and should allow you to run higher caster angles which I would think would be beneficial as your have a lot of KPI and offset on the front end. (Offset may be beneficial as it may be helping you unload the rear end like a go kart does). Caster won't reduce the amount of weight jacking you get but will tie your front camber curve to slip angle more then body roll.
That said all of my experience is in tuning and building light IRS vehicles. It's possible everything I said will make it worse and it is all the way it is because it is the best compromise to get the thing to work.
Just wondering why do you have a specific ride height in mind and how does that ride height compare to what it ran before? Ride height is usually entirely dictated by the designed geometry and adjistments tend to be to mess with weight jacking (raise rear increase rear weight transfer, lower front decrease etc.). Just picking a new ride height can have unintended consequences as the front and rear roll centers move very different especially with a panhard bar and your cg heigta at the two ends of the car tend to move the same amount as the chassis.
When I went through minimizing bumpsteer on my current project, it did not take much of a change in anything to get the geometry out of "optimal." I have certainly learned that you need to design EVERYTHING around your intended ride height, and changing it almost always brings issues.
The fun challenge can be when it's all done and you're testing it, and you discover you need to change the ride height to deal with a handling issue.
unevolved said:
fomoco01 said:
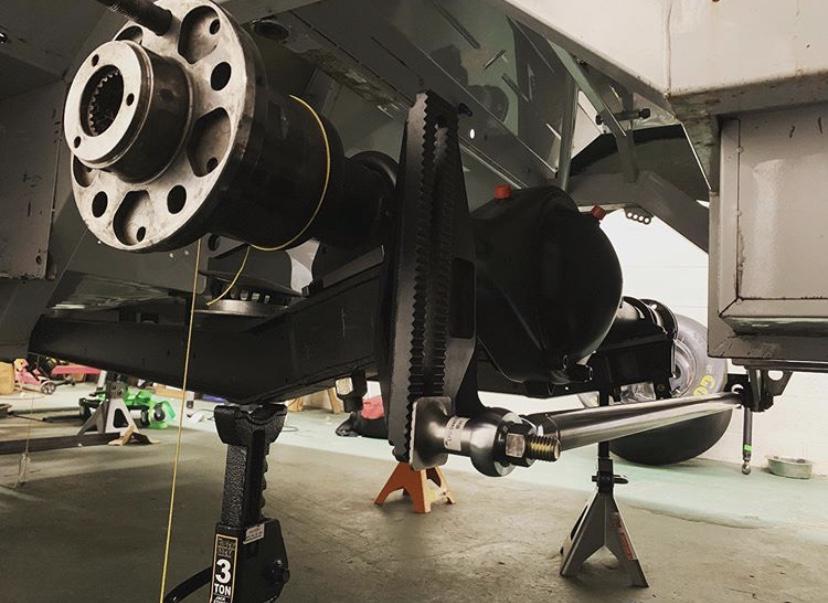
Do the axle saddles have one pin? Looking at that track bar mount, I would try and run as little standoff as you can, clearance-wise. The rear end on a stock car, for a non road course setup, is designed to laterally flex under load for kinematic and aerodynamic reasons. You're going to be fighting that on this car, I'd bet. Given that it's a K&N car, they may not have had road course AND oval truck arms, that adjustment slot on the TB mount looks longer than it needs to be- I don't know of any road course setups that run a high track bar, they're usually lower than the top of the truck arm I-beam. That longer slot is going to allow more lateral movement under load. I'd also recommend running some braces from the bottom of the U-bolt nuts to the center of the axle housing; those truck arms are going to try and twist under load.
I'm not sure what used prices are like, but a road course truck arm would have a stiffer left side track bar mount and help get rid of some of that deflection. Someone like SRI here in Mooresville may have an idea.
I'd really consider running a three link. Truck arms are inherently overconstrained, at best you can make them not suck. A general rule for engineering decisions on NASCAR racecars is "the right way isn't legal, so we've got to brute force the wrong way."
Wow, this is all great info, thanks for chiming in! I believe they do have one pin, but I could check to make sure. That makes sense about the standoff and the only reason I have the spacer on there is to try and get the bar closer to being on a straighter plane with the track bar mount on the chassis end. As far as the truck arm, I have seen the drivers side arm bend from the load but didn't realize that it would be an issue on a road course, I have an assortment of truck arms that I will look through and see if there is something better. At a minimum, I will brace the u bolt like you mentioned. Would you recommend that on both arms? I'd definitely be open to doing a 3 link eventually, at the moment I just want to get the thing running and driving so I can start tweaking! The car is in a small shop in Mooresville and I have been going to SRI every Saturday (up until this crap started happening) and picking up some used parts!
nocones said:
Looking at the front it looks like your Virtual Swing arm (VSAL) is about .75* the track width, and your Instant center appears to be underground. Your roll center in the front is likely at ground level and with those short of VSAL will tend to make it move around laterally a lot if the suspension is allowed to move at all. The other thing Short VSAL tends to do is cause a lot of camber gain/changes in bump/droop.
I wouldn't worry to much about the lower A-arm but would attempt to raise the innner ball joint on the upper A-arm. This will lengthen you VSAL which will reduce camber change and should allow you to run higher caster angles which I would think would be beneficial as your have a lot of KPI and offset on the front end. (Offset may be beneficial as it may be helping you unload the rear end like a go kart does). Caster won't reduce the amount of weight jacking you get but will tie your front camber curve to slip angle more then body roll.
That said all of my experience is in tuning and building light IRS vehicles. It's possible everything I said will make it worse and it is all the way it is because it is the best compromise to get the thing to work.
Just wondering why do you have a specific ride height in mind and how does that ride height compare to what it ran before? Ride height is usually entirely dictated by the designed geometry and adjistments tend to be to mess with weight jacking (raise rear increase rear weight transfer, lower front decrease etc.). Just picking a new ride height can have unintended consequences as the front and rear roll centers move very different especially with a panhard bar and your cg heigta at the two ends of the car tend to move the same amount as the chassis.
Great info, thanks for sharing! That makes a lot of sense, I will try to find a way to change the upper a arm angle. I may be able to find a shorter ball joint, but the inboard mount is as far up as possible. What do you mean by "offset"? Do you mean the wheel offset in relation to kpi? I was actually wondering about KPI and scrub on this car, it does not seem like you can make it any better without changing wheel size (which I plan to do).
I picked the ride height mostly due to the amount of clearance between the tire and the fender. The car is sitting a little lower than I plan at the moment, but I plan on doing a fair amount of aero work, so trying to keep underbody volume to a minimum. And what you were saying about picking a ride height as the first step makes total sense to me, I just don't really plan on changing any of the suspension pickup points from where they are now, just want to get the best out of what I have. The car did not have any suspension when I got it, so I'm working from scratch and finding the parts I need has been quite a challenge.
SkinnyG (Forum Supporter) said:
When I went through minimizing bumpsteer on my current project, it did not take much of a change in anything to get the geometry out of "optimal." I have certainly learned that you need to design EVERYTHING around your intended ride height, and changing it almost always brings issues.
The fun challenge can be when it's all done and you're testing it, and you discover you need to change the ride height to deal with a handling issue.
Thanks for chiming in, this makes a lot of sense and I now realize that you're right in pointing out that ride height should be the first step of the process. Just have to figure out how to optimize what I have!
Driven5
UltraDork
5/1/20 10:57 a.m.
fomoco01 said:
I realize that I could have a set of spindles made, but the lower ball joint is already close to the wheel and tire as it is, so that doesn't seem like a good option.
The car came with 15" wheels. You've got a tire for 18" wheels. That should provide ~1.5" of additional clearance to drop the ball joint.
Driven5 said:
fomhoco01 said:
I realize that I could have a set of spindles made, but the lower ball joint is already close to the wheel and tire as it is, so that doesn't seem like a good option.
The car came with 15" wheels. You've got a tire for 18" wheels. That should provide ~1.5" of additional clearance to drop the ball joint.
That's part of the dilemma. The 18" tires I want to run are about an inch or so shorter than the Goodyear's that are on it. I currently have the longest ball joint studs that I've been able to find. Can't find much info on the Moog ball joints that most people run, so I picked up a set from qa1. Also, not sure that I'd necessarily want to run a longer ball joint than what's currently on it.
What happened with this project? The engine/chassis combo is pretty epic.
Hey guys, sorry for being away for...several years...
Unfortunately and fortunately, I had to move across the county on extremely short notice and this project had to go. I'm still playing with cars though, I just had to pick up a substantially less interesting toy.