kylini
HalfDork
4/2/15 10:41 p.m.
Two on the Intrepid. 1) Why is the thermostat in an impossible to access location and, for good measure, STAKED INTO THE HOUSING? Any consumable part shouldn't require a bench grinder in the FSM procedure. 2) The battery requires removing half the air box and a FRIGGIN' TIRE. Yeah. Fender access batteries. Except you still need above access too. PICK ONE GRAARRGH!
whoever designed the 3.0/3.6 gm v6. Ever tryed to service one while hot? The 2014 cummins wear you have to remove the filter box and turbo inlet to remove the oil filter. How about the late 90's 2.2 cavaliers? ive learned too hate engineers for just basic service stuff. Dont even need to get into harder work!
You should not need a hub puller to change out your wheel hub bolts. All you need to "design" is a little notch to hammer them through.
Dipstickless automatic transmissions.
Opti
Reader
4/2/15 11:00 p.m.
pretty much everything ford did from 2000 to 2012 Or whenever they killed the 4.6 and 5.4.
AMC for putting the clutch master cylinder in XJ's directly above the fuse panel.
Where does the fluid go when the clutch M/C fails? Oh, right.
Know what doesn't like brake fluid? Insulation...
From my Locost build log:
A long time ago, in magical place named Detroit, there was an engineer working at Ford. He said "I shall cast my rear lower control arms from Iron. This will save cost and allow me to place the simple bolts attaching the spindle in double shear. Furthermore it shall allow easy access to these bolts so that the rear suspension will be easy to disassemble." and there was much rejoicing.
Then the evil engineer from Lincoln looked at the design and said "To make mine superior I shall cast my rear lower control arm from aluminum. Even though this is a very large and heavy car, this will make it seem as if we care about reducing weight. However I shall place these special bolts in single shear and in such a way that in order to remove the axle, you must first remove the upright...But in order to remove the upright, you must first remove the axle." and the rejoicing was replaced by the curses and obscenities of any who dared try to remove the axles on their Mk. VIII.
Later, the Lincoln engineer received a swift kick in the plums...And there was much rejoicing.
amg_rx7
SuperDork
4/3/15 12:29 a.m.
Porsche engineers for IMS bearings
BMW engineers for plastic cooling systems, control arm bushings that start wearing out every 30k miles, O2 sensors and other parts that require $pecial tool$ to replace, Nikasil liners, etc etc
VAG engineers for... ah screw it, too long of a list...
amg_rx7
SuperDork
4/3/15 12:30 a.m.
Driven5 wrote:
From my Locost build log:
A long time ago, in magical place named Detroit, there was an engineer working at Ford. He said "I shall cast my rear lower control arms from Iron. This will save cost and allow me to place the bolts attaching the spindle in double shear. Furthermore it shall allow easy access to these bolts so that the rear suspension will be easy to disassemble." and there was much rejoicing.
Then the evil engineer from Lincoln looked at the design and said "To make mine superior I shall cast my rear lower control arm from aluminum. Even though this is a very large and heavy car, this will make it seem as if we care about reducing weight. However I shall place these bolts in single shear and in such a way that in order to remove the axle, you must first remove the upright...But in order to remove the upright, you must first remove the axle." and the rejoicing was replaced by the curses and obscenities of any who dared try to remove the axles on their Mk. VIII.
Later, the Lincoln engineer received a swift kick in the plums...And there was much rejoicing.
Hehe
And where is this locost build log?
In reply to amg_rx7:
Take your pick: garageodyssey.blogspot.com, garageodyssey.tumblr.com, www.locostusa.com...Or last, but certainly not least, grassrootsmotorsports.com. Also trying to instagram @GarageOdyssey.
In hind sight, I'm pretty sure the Lincoln engineer finished his statement with a "Muahahahaha!"
The ones who designed the 4th gen Camaro... specifically the front shock mounting. Seriously, one type of fastener was not good enough so you designed a part that uses SAE, Metric, and Torx? Oh and the power steering pump positioned right off the header bank was awesome with its 100% failure rate under any kind of performance use, anything but straight line driving at low RPM's and the fluid boils. Oh and moving the clutch slave cylinder inside the transmission housing for '98 was awesome too...but at least y'all thought about if transmission ever needed work done on it and provided directions on dropping the whole front subframe with suspension, engine, and transmission out as one unit since apparently that is the easiest way to get the transmission out or change the spark plugs - Yep everybody has a lift in their garage.
Felt so odd when the serpentine belt was the easiest thing ever on any car I've done.... mere seconds to get the old belt off and not much longer to put the new one on. Where was this engineer for the suspension, engine, and transmission design?!
And +1 on GM sheet metal purposely being designed to cut you up whether in the engine bay or interior. I still have a scar from that Camaro (mostly physical...)
One from my dad - his 2014 XC60 doesn't have an actual dipstick. On top of that, the software for the oil level sensor is calibrated like an idiot light - either you're full, or empty. The actual gauge has a bunch of graduations, making the owner think it would give an accurate oil level.
Lots of nut-kick negativity here (and with good reason) but I'd like to give nut-props to the designer of the Suzuki Samurai.
Pulled a head in about 15 minutes with a 3/8 ratchet, removed/replaced exhaust manifold with header in about 1.5 hours dragging my heels.
Replaced alternator (had to take good one from parts-truck first) in 15 minutes in the dark. Drop out 3rd members front and rear, simple leaf spring suspension and I could go on and on.
Just figured I'd offer an opposing view even though every other vehicle I've owned has frustrated me to no end.
Oh, and let's not forget whoever managed to package the starter on an E36 so that replacing it requires removing your choice of the intake manifold or the transmission.
I've had other cars where I could swap out a starter in 10 minutes.
Props: '89 Corolla starter died so I changed it in 15 minutes with a crescent wrench in a parking lot.
Kicks: '85 Shelby Charger starter died and took me about 12 hours of hard labor on jack stands to replace (and wan't entirely right afterward). Who puts intake manifold, exhaust manifold, turbocharger, and starter all on the same side of the motor? And then slams the whole mess up against the firewall for ease of access.
Props: '98 Corolla air filter replacement took ten seconds and no tools. Spark plugs all sit right on top and changed in 10 minutes.
Kicks: 2000 Grand Caravan air filter took two different tools and 5 minutes to access. Spark plugs......well, changing 5 of 6 was probably good enough. Bonus kick for dodge on this one: hood release and parking brake release are the same feel and within a couple inches of one another. I like getting out to slam the hood half the time I'm setting off.
Kicks: VW. Why: everything
I'd like to point out the brilliance of the water pump on the BMW M54 engines. (No, really).
I replaced mine a few months ago, and it was one of the easiest I've ever done. It's the type that inserts into the block and seals with an O-ring. I was trying to figure out how to pry it out of there with various chisels and screwdrivers, and I noticed the two threaded holes that take the M5s that held the thermostat on previously in the job. It's got a built-in puller! They clearly went out of their way to make it easier to service.
The PRV engine.
Seriously?
I can't find a single thing about the design of that engine to like.
pinchvalve wrote:
Interesting assumption that all engineers are male...or is t just all engineers who make stupid decisions? That I might believe.
No there is equality in engineering mistakes but a many of the things I read in this thread aren't mistakes and are either regulated that way for good safety reasons or allow for cheaper faster assembly in modules in the plants. Faster assembly = cheaper for us to buy. There is a balance to all engineering.
My pet peeves is that the USA still remains the ONLY country that hasn't fully converted to Metric. Just dumb dumb dumb, sigh I feel sad for my country sometimes. Holding onto foolish things like Standard American Units and Daylight Savings time. I am certain engineers didn't make that call.
I remember working on my first FSAE car in college. I went to top off the engine oil and there was structural frame member in the way of the oil filler. I thought "I wish I could ask the berkley-tard who designed this what the hell he was thinking." Then I realized he was in the next room. So I went into the next room and said, "ROB! How the Berkley are we supposed add oil the car and what the Berkley were thinking when you designed it?" a bunch of the senior team members started laughing. Rob looked up and a little sheepishly said, "Yeah. I made a mistake. I was in a hurry to get the frame done and didn't think about the oil filler at all." So smiled at him and said, "I nominate Rob to do the engine maintenance until he designs and builds new parts that make it easy to do." This was met with more laughter.
Future car designs had much easier access to change all the fluids. A least until I graduated.
In reply to KyAllroad:
Yeah the original starter on those was a bastard due to the size and the need to add a brace to the block.
The later cars used a smaller starter that was easier to deal with.
Also pulling the passenger half shaft and axle helps a lot and allows you to change the transaxle fluid and reinstall a heat shield on the starter.
Doesn't completely absolve them of the stupid design there. They did fix it on the Neons though (which were based on what they learned on the 2.2/2.5 cars).
Back in highschool I had a '72 Ford Pinto with the German 2.0L. The rear cam journal was larger than the front cam journal, which means that to pull the cam, you either drill a hole in the firewall and pull the cam into the front seats, or you pull the head (which needs a fancy tool to undo the head bolts).
Surely this kind of engineering oddity goes WAY further back than we know.
I've only read the first page, but I'm stopping now. You guys would never make it as technicians.
Use the proper tools in the proper way, and almost none of this is an issue. Complaining about having to buy three different torx sockets? I have long and short torx sockets, stubbies, inverted, tamper proof, and several torx bit sets including five point in my tool box.
bluej
SuperDork
4/3/15 12:22 p.m.
MadScientistMatt wrote:
Oh, and let's not forget whoever managed to package the starter on an E36 so that replacing it requires removing your choice of the intake manifold or the transmission.
I've had other cars where I could swap out a starter in 10 minutes.
Yeah, this. It gets worse when you've put said motor into an e30 but re-used the larger early m20 starter from the e30.
I'd like to add e30 stereo wiring to the list. All I want to do is add a basic head unit for listening to tunes on the way to events. There's no simple way to wire the speakers.
I also have a theory for all German vehicular nominations. It's called Oktoberfest.
In reply to Junkyard_Dog:
Not complaining about having to buy them, I have 3 of every tool known to man in my garage - I'm complaining about having to CARRY them for even simple E36 M3 like removing the windscreen or changing the front tire. Different.
When you are here:
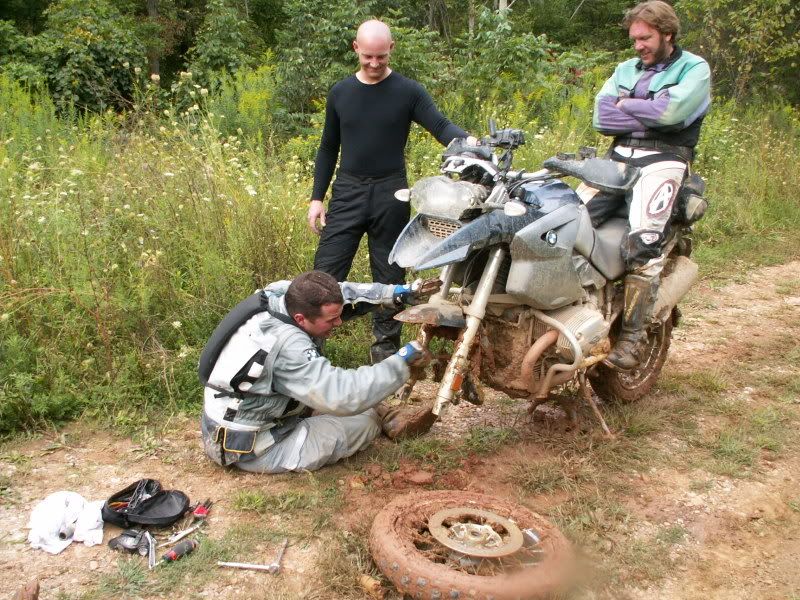
Keeping it simple is appreciated.
bruceman wrote:
All those exhaust system engenears who insist on steel bolts and flanges on a stainless steel exhaust system!
That is because stainless bolts gall like a sonofabitch and they are also pretty brittle. Stainless steel is not a material for anything structural.
tuna55
UltimaDork
4/3/15 12:44 p.m.
Knurled wrote:
bruceman wrote:
All those exhaust system engenears who insist on steel bolts and flanges on a stainless steel exhaust system!
That is because stainless bolts gall like a sonofabitch and they are also pretty brittle. Stainless steel is not a material for anything structural.
Yah, stainless bolts are scary.