Mr_Asa
PowerDork
9/26/21 11:38 a.m.
I have to make a lifter galley cover for the LS4.9
I'm probably going to make it out of aluminum. I'm leery about putting threads into the aluminum just because I've had so many poor results with bolts seizing in aluminum threads, or the threads stripping out, or whatnot. So tell me what I need to do to make these things last.
The hole diameter is 10mm, so I was thinking 3/8" thickness minimum for the material the threads go into? Should I go with rivnuts instead? Some other method?
If I go with tapping it, 10x1.0? 10x1.25?
Picture of where the lifter galley cover will go.
A-B: 4"
B-C: 1.5"
C-D: 26.5"
A-C: 4.25"
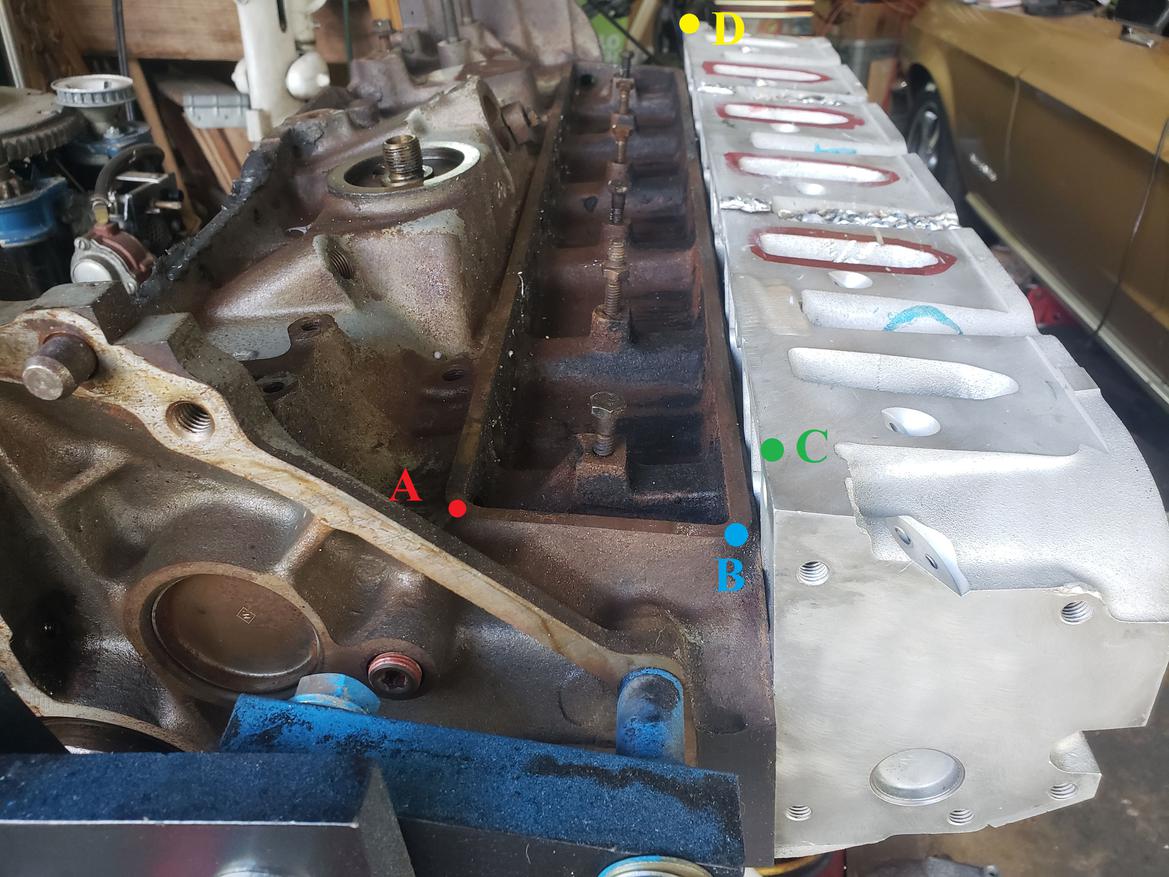
The Yukon aluminum third member in my 9" rear resists all of the torque trying to ram the pinion gear forwards and out of the car, by five 7/16" (might be 3/8") bolts threaded into aluminum. The housing is rated to 1200hp.
I did Helicoil them, because I had it apart so many times that I wore out the threads.
You will be fine.
Use Coarse threads into aluminum.
Use studs if it will be disassembled often.
If I am seeing this correctly, you need to make an L shaped cover to cover the lifters, and also to cover the edge of the head.
Correct?
I would use a piece of material thick enough to cover the bottom of the head as required. Use the existing bolts into the block as the main attachment point, and then just a couple of bolts to pull it up against the bottom of the head. Main bolt holes slightly ovalled to allow it to be sucked up to the head before finish tightening the block bolts. The material would be thick enough you can go as deep as you want.
Unless I've missed something regarding pushrod clearances. Even then, I would use a solid piece, and mill out the passages I need. If it's too thick and chunky for your taste, mill it into a taper, so the bottom edge is prettier and the top is sturdy enough.
That would also solve the challenge of getting that stupid side cover to not leak.
Mr_Asa
PowerDork
9/26/21 1:38 p.m.
Pushrods are going to be going at old school Hemi angles, so the galley cover will end up being reminiscent of a lean-to shape. Angled from A-C and filled in at triangle-ABC. Once I get some rockers I can mock up angles and make sure that what I have planned will cover everything.
Oil drain back and pushrod passage goes through BC
In reply to Mr_Asa :
I'd mill it out of solid stock, still. Trying to get sheet metal to seal that will be hell.
Mr_Asa
PowerDork
9/26/21 2:20 p.m.
In reply to Streetwiseguy :
I'd love to. What I can do and what I have the tools and time to do is a vastly different situation, though.
RTV will fix any sealing issues.
Mr_Asa said:
In reply to Streetwiseguy :
RTV will fix any sealing issues.
Maybe. 
You know that you can use a wood router to cut aluminum, right?
A couple of wedges of wood to give you the correct angle of the groove and the right router bit, you are golden.
In lieu of heli-coils, think about Time/Zerts. Helicoils line the threads, zerts give 100% contact area, better for something removed often. Harder to mess up.
Mr_Asa
PowerDork
9/26/21 4:07 p.m.
914Driver said:
In lieu of heli-coils, think about Time/Zerts. Helicoils line the threads, zerts give 100% contact area, better for something removed often. Harder to mess up.
Full steel body as well. I like the idea. Adds to the cost for Challenge purposes, though.
That is waaaaay overthinking it, IMO. The Ford engine had a piece of steel held on by four or so bolts. You're sealing a hole, not doing anything structural. Anything you do will be fine, up to and probably including just gluing your cover on with Right Stuff and not using any fasteners at all.
Mr_Asa
PowerDork
9/26/21 4:44 p.m.
Pete. (l33t FS) said:
That is waaaaay overthinking it, IMO.
This is the Mr. Asa method, yes.
In reply to Mr_Asa :
Oh, it's the Pete method too, don't get me wrong. That's where I sit and stare and ignore a problem for a few years until a dose of reality hits and I find the simple solution. This is not the best for getting projects finished.
In reply to Pete. (l33t FS) :
I've had enough experience with aluminum threads, I make it a rule of design to never use aluminum threads. Structural or not, it's going to seize.
I would put some coils in now while it's easy, and not in an engine bay.
Mr_Asa
PowerDork
9/26/21 5:13 p.m.
Mr_Asa said:
Adds to the cost for Challenge purposes, though.
$52 for 20...
Having a helluva time finding the keyed locking style.
Mr_Asa
PowerDork
9/28/21 5:28 p.m.
I'm in for glueing it on with RTV just for entertainment.
Mr_Asa
PowerDork
9/28/21 5:34 p.m.
Keith Tanner said:
I'm in for glueing it on with RTV just for entertainment.
Hey, the only one of these engines that's running (as far as I know) RTV'd the head sections together...
lnlogauge said:
In reply to Pete. (l33t FS) :
I've had enough experience with aluminum threads, I make it a rule of design to never use aluminum threads. Structural or not, it's going to seize.
I would put some coils in now while it's easy, and not in an lengine bay.
Jaguar has had aluminum threads in a lot of stuff since the 2nd WW. Rarely is it a problem. If I need to extract bolts or studs frequently I use a little anti seize.
Corrosion? I'll use a little heat and ATF + acetone. Let it cool and the reheat.
Don't over think it. It sounds like you have analysis paralysis or just plain fear.
It's not just Jaguar but Alfa and heck most cars.
Aluminum threads are fine.
Making the thread engagement 2 * thread diameter is a good rule of thumb for aluminum thread depth.