I have often wondered about what made a particular shape expensive, or what about a certain "look" a car had mad eit expensive to produce.
Take for example these two:

Against this:

Fairly similar in concept and even design, but the Boxster, putting aside the internals or interiors of either car, has a fuller, rounder shape, likely a wider track and wheelbase, etc.But, what would stop a car maker from making a car with more basic internals look a little more developed? I've always thought the MR2 was almost an 80% xerox of the Boxster, but it is of course a little more slab sided, a little less proportioned in the nose, and frankly shows its more value oriented roots in these qualities.
It seems like lately, more car makers are developing cars that look much more expensive than they are, like the new Fusion for example, but what is it about the actual shape of the panels that makes it costly to produce today, as opposed to when panels were hand beaten and lead welded?
yamaha
PowerDork
10/23/13 3:33 p.m.
In reply to mattmacklind:
The stampings are the easy/not so expensive part, the machined parts, now theres the bulk of your manufacturing expense
My brother was an engineer for one of the big three in Detroit, and part of his job was figuring out if the stylist's designs could be transferred to the stamping dies. He said the stylists would often come up with body shapes that would have been expensive or impossible to stamp, so there would be a lot of back and forth between the stylists and engineers until they could compromise on shapes that could be economically be put in production.
I'll add another that emphasizes your point:

vs

vs

vs
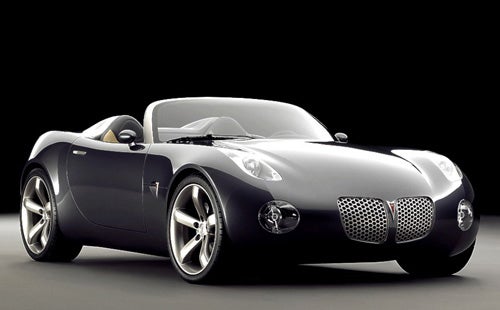
I feel like I'm automatically biased toward the exotics, but can't put my finger on it. Looking at the FRS next to the Alfa, the FRS actually compares nicely.
Edit: Acknowledging the fact that the alfa picture is a photoshop.
Wedges. Everyone knew the faster Hot Wheels were shaped like wedges. This thought process has carried over into adulthood.

I have no data to back this up....
I was under the impression that all of those cars cost the same to manufacture. Not just those cars but any like cars.
If there's anything to the shape itself, I'm guessing compound curves are harder and/or have a higher rejection rate.
Anything that's more deeply drawn will eventually wind up requiring multiple press operations, I think? So there'd be a whole additional set of dies and a press taken up on the assembly line by each required step to draw to full depth...
I'm talking from half-remembered "How It's Made" and so forth, so I could be WAY out in left field...
Interesting to think about. What led me to pose the question was the Lotus Elan (M100) discussion on the classic thread. Regardless of position on the car itself, having seen them in traffic, they really draw the eye the way an exotic does, like when you know something very low and wide was in your field of view but you don't yet know what it was so you pull up and around to identify it.
It is not an expensive car per se right now, and was actually sold as a badged Kia in Korea. Again, from a strict form/design perspective, it is simply much more striking than the Miata was at the time, and despite run of the mill mechanicals, was significantly more expensive. Then again it was fiberglass, so that might be a factor.
stuart in mn wrote:
My brother was an engineer for one of the big three in Detroit, and part of his job was figuring out if the stylist's designs could be transferred to the stamping dies. He said the stylists would often come up with body shapes that would have been expensive or impossible to stamp, so there would be a lot of back and forth between the stylists and engineers until they could compromise on shapes that could be economically be put in production.
IIRC the hood for the HHR required five separate stamping processes.
Ever read the book "Small Wonder"? It was written in the 70s as a history of the Volkswagen company, back to the early 1900s. One thing the VW engineers noted when they tried to restyle the original (like, ORIGINAL original) Type 1 is that anything they did would significantly increase the amount of sheetmetal required. Pre- and post-war, this was a huge consideration.
(Random trivia: The window was split because the roofs were welded from two pieces. Something about not being able to get sheetmetal of the proper size for a one piece roof...)
stuart in mn wrote:
My brother was an engineer for one of the big three in Detroit, and part of his job was figuring out if the stylist's designs could be transferred to the stamping dies. He said the stylists would often come up with body shapes that would have been expensive or impossible to stamp, so there would be a lot of back and forth between the stylists and engineers until they could compromise on shapes that could be economically be put in production.
You can stamp darn near any shape you want. Now getting that shape out of the press is a while nother ball of wax.
Though lately with hydro-forming of aluminum you can do some insane stuff. Bentley in particular has done some amazing stuff with single hydroforming steps and laser cutting.
^ Hopefully when mainstream auto manufacturers get their hands on the equipment Bentley is using, they use it for good instead of evil.
It would be a terrible waste to use expensive hydroforming and laser equipment to build boring SUVs. Heck, it is in my opinion a terrible waste to melt down scrap soup cans to build an ugly boring SUV.
I had a couple of roommates at college 15 years ago who were working on stamping of aluminum body panels. There were limits to what you could do to without introducing stresses that would lead to fatigue problems. They also talked to me about multi stage stampings in steel and how a reduction of one step was a huge deal.