I have a super-sweet 40x60 garage planned. If I gave the plans to a contractor it would probably cost in the neighborhood of $60k to build. I'm trying to get some friends/neighbors to chip in and build it GRM style instead.
The project looks like this:

It will be cut into a hill. The driveway would lead to the upper doors for parking on the mezzanine. Basically, the bottom 8' of the building would be a foundation wall with some kind of construction on top of it... steel, stick frame, post, SIP, whatever.
My neighbor two doors down has a landscaping company and they have the means to excavate. I can custom-order a steel building (some assembly required) for around $16k. I'm wondering if you folks can give me some tips on building the foundation so that I can do as much as possible on my own without paying the big bucks.
Would you do it as concrete block? Poured walls? Foam-insulated forms?
What is most cost-effective/easiest to DIY?
Just wire it for 3 phase, whatever you do.
just a thought: leave an opening in the floor of the upper level inside one of the doors to allow you to use that bay as a "pit" for some super easy under car work like transmission swaps and oil changes and what not... make the section of the floor about 3 feet wide and 10 feet or so long removable so you don't have to worry about falling thru it when you aren't doing work on cars in that bay..
or leave the floor out of that one section and put a nice tall 4 post lift there to act as an elevator/work pit..
otherwise i have nothing to offer here...
I assume the plans aren't complete? I'd hope you'd have more support for the "mezzanine" if you're parking cars on it. It looks like the wall with the doors on it would be the 60' side? If it is, I doubt you'll get away with not having trusses for the roof. If that's the case the center door on the high side won't work. Other than that can you obtain permits in your area without a general contractors license?
note: rereading this it sounds like I'm being a happy shiny person. That's not my intention, I'm just not sure how else to put it.
Had a friend use.....I forget the name, basically it was a filled block construction. Basically you stack special interlocking blocks dry like lego, and then the cement truck comes and fills the hollow space with concrete. This was for a basement in Upper Michigan and he was very happy with the price and work when it was all said and done. He and his two brothers laid all the block over a weekend and then the truck came on Monday. Quick and easy.
Josh
SuperDork
5/2/13 7:02 a.m.
In reply to mazdeuce:
ICF. Insulated concrete forms. Foam blocks, fill them with concrete, structure and insulation in one step. You have to cover the foam on the outside somehow though, or it will be damaged.
Ian F
PowerDork
5/2/13 7:16 a.m.
Kenny_McCormic wrote:
Just wire it for 3 phase, whatever you do.
Easier said than done sometimes. Many residential areas aren't wired to provide 3-phase power. Sometimes even in commercial areas. I had a project years ago where a client (a radio/cable company) wanted to run 3-phase power to one of their transmitting towers. When we got the medium voltage line upgrade quote from the utility company (we're talking well into 5-figures here), the PM nearly sh1t himself and we found another solution to their problem that was much cheaper. And this is a company with much deeper pockets than your typical homeowner.
As far DIY costs, concrete will probably be your biggest expense. As you'll find out, the building itself is pretty cheap - what that building sits on isn't. Make sure you're sitting down when you start getting quotes for a 40' x 60' slab.
Foundation designs vary depending on location, but you typically pour a concrete footing below the frost depth and then build a block wall up to a couple of feet above grade. Then 2x construction for the walls. Probably 2x6 for such a large building. Sometimes it's easier/cheaper to order pre-made trusses for the roof span.
For a metal building, go online and/or talk to potential vendors to find out what they need for a foundation.
moparman76_69 wrote:
I assume the plans aren't complete? I'd hope you'd have more support for the "mezzanine" if you're parking cars on it. It looks like the wall with the doors on it would be the 60' side? If it is, I doubt you'll get away with not having trusses for the roof. If that's the case the center door on the high side won't work. Other than that can you obtain permits in your area without a general contractors license?
note: rereading this it sounds like I'm being a happy shiny person. That's not my intention, I'm just not sure how else to put it.
I dont know the code in your area, but around here, Doubled 2x10 SYP rafters would cross a60' span at 7/12 without deflecting. It would be costly, but it would get you the height. If its going to be a steel building, you could get away with that steel beem criss-cross construction that a lot of pitched warehouses use:
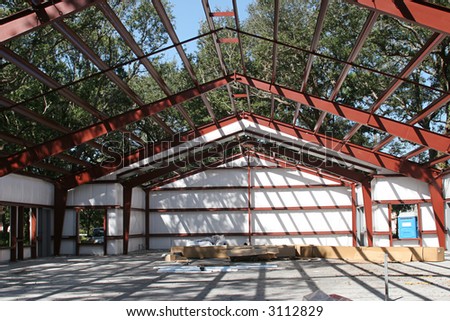
...Would also be pricey, but maybe not much more than engineered wood trusses?
Having a supported concrete floor to support automobiles is probably going to require an engineer to design and stamp.
Love the idea of the mezzanine, but it's going to require some careful engineering. Think of it this way: three 3,000 pound cars sitting on it are only the tip of the iceberg. The mezzanine itself will weigh at least twice that, MUCH more if it's concrete slabs. That means careful engineering of both the supports and the floor below.
Me, I'd build the walls of concrete block to the level of the mezzanine and then park the steel building on top of that.
Duke
PowerDork
5/2/13 8:11 a.m.
spitfirebill wrote:
Having a supported concrete floor to support automobiles is probably going to require an engineer to design and stamp.
THIS. Plus, that whole lower part is functioning as a retaining wall, and it's not boxed like your house foundation is. There's a lot of engineering in there - yes, if you are buying a steel building, you can tie the mezzanine diaphragm framing back into the side walls to brace the top of the wall, which will help... but the pre-engineered building people need to know about that, and it's going to introduce some lateral loading that they typically don't deal with.
@ Curmudgeon: live load from cars is actually pretty reasonable. Yes, a car may way 3000-4000 pounds, but it is typically spread out over 100 sq ft or more of structure, so the loading is only 30-40 psf.
klb67
New Reader
5/2/13 9:07 a.m.
In reply to curtis73:
Your drawing is similar to a common old barn design around here with lower access for animals and upper access for hay, etc. Those barns have stone/block walls for the entire lower section, wood above.
I think you'll need to have an engineer look at it if you want to just use the back wall as a retaining wall and frame the rest, as Duke mentions. Depending on what look you want, if you don't mind concerete block for the entire lower section, I'd get a quote for that footer, block and slab. I helped my dad build a home addition where he farmed out the block and concrete work (4 car garage below, living and kitchen above) and we did all the framing except the roof/shingles.
In reply to Duke:
True, but in this case there's a cantilevered mezzanine also. If it's done in concrete also it's going to be HEAVY. A square foot of concrete 4" thick weighs 48 pounds. A 40 foot by 12 foot slab 4" thick will weigh 23,040 pounds. Add another ~8,000 pounds for the steel framing. All that load, including the weight of the cars, would be approx. 40,040 pounds transmitted to the lower slab via 5 posts which, if they are, say, 6" diameter steel tubing, a quick rough calculation gives me each has a load bearing surface of 28.27 square inches x 5 = ~ 141 square inches of load bearing surface for the 5 posts.
40,040 pounds of load divided by 141 square inches is only 284 psi, but concrete has no real shear or tensile strength, only compressive, it's typically 3000 psi compressive, not shear. But that's dependent on the substrate, if it's not properly prepped so that it can support the concrete slab then the necessary strength might not be there. As in: if the substrate shifts or settles then the post punches through with disastrous results. I would not want to be under that 40,000 pounds if that happened. So yeah I'd rather be real sure.
Duke
PowerDork
5/2/13 3:36 p.m.
Oh heck, the posts of the mezzanine can't bear on the ground slab! They'd punch right through. They're going to have a footing, probably 48" square at a very minimum (more like 60") and 12" thick with half-inch rebar at 12" on center in both directions, 2 layers - under each post.
The upper slab will probably be on formdeck, which hill about halve the cubic volume of poured concrete without reducing the rigidity any.
See why we think you need an engineer? 
Personally, I wouldn't use the mezzanine for cars, I'd just build it with a standard wood floor and use it for storage, office, or maybe lighter work. Building something that far off the ground that's strong enough to safely hold cars would be pretty expensive to do right. And dangerous if done wrong.....
Pre engineered trusses are a damn sight easier (and cheaper) than DIY. BTDT. One other thought: on the side that's dug into the hill, of course you want to seal the side of the block that's going to be buried and provide a French drain or similar for water to exit around the sides. That will keep the walls inside from sweating and efflorescing.
Ian F
PowerDork
5/2/13 4:00 p.m.
In reply to Tom_Spangler:
I don't know... My g/f's parents have a barn like the one mentioned earlier. 3x oak planks for the upper floor. They've been parking a 1.5 ton (~ 10,000# GVWR?) Diamond T DRW truck up there for over 40 years.
Ian F wrote:
In reply to Tom_Spangler:
I don't know... My g/f's parents have a barn like the one mentioned earlier. 3x oak planks for the upper floor. They've been parking a 1.5 ton (~ 10,000# GVWR?) Diamond T DRW truck up there for over 40 years.
yeah, but that's different... somehow...
Ian F wrote:
In reply to Tom_Spangler:
I don't know... My g/f's parents have a barn like the one mentioned earlier. 3x oak planks for the upper floor. They've been parking a 1.5 ton (~ 10,000# GVWR?) Diamond T DRW truck up there for over 40 years.
Old barns are a touch different, you cant really buy wood like that anymore for starters. I suppose you could build it in steel and deck it with wood, footings are still a concern.
I like the idea of putting a 4 post lift in the corner and only using it to bear the weight of a car. Use the rest of the mezz area for storage.
Ian F
PowerDork
5/3/13 7:28 a.m.
Kenny_McCormic wrote:
Old barns are a touch different, you cant really buy wood like that anymore for starters. I suppose you could build it in steel and deck it with wood, footings are still a concern.
Yes and no. The materials are different but the engineering is basically the same. They are still building timber-frame structures, so you can still get wood like that, but it'll cost a fair bit. Steel is cheaper and stronger, so you'll need less of it to perform the same function. Not that structural steel is particularly cheap these days...
Yes, the footers for the support columns would be considered structural members, so they would need to be fairly deep. The actual footer size would require engineering calcs by a structural engineer and will vary depending on the soil bearing capacity.
FWIW, the home body-shop barn/shop I mentioned over in the "start a business" thread is basically built how Curtis is describing, although the second level covers the entire square floorplan. It was a little smaller than Curtis' though, so I'm pretty sure there are no columns on the ground floor and the second floor slab is supported by steel beams spanning the width, sitting on the block walls. The slab was poured over steel decking, common to commercial construction. I'm not sure how much of the build he did DIY, but he did say many of the materials were bought cheaply by keeping an eye/ear open for various deals and then making them work.
I'd agree with the sentiment that the mezzanine design will take some hard looking at by a structural engineer to ensure that the supporting structure can take all the loads it will see. I would also be worried if it were me about the possibility of a vehicle going over the edge of the mezzanine and into the lower area- you'd need to make sure there was a sufficiently high (and strong) barrier to prevent that. I would think you'd have a much easier time using the lower section for the vehicles- you'd even have plenty of height for a lift or two.
Glad I read through this thread too- my curiousity about the ICF led to my finding that one of the companies that makes them also makes a fairly simply (looking) to install insulation & finishing system for basements that I think could also be used to insulate a garage...
When we had our house built, they did a "pretensioned foundation". What this means is, only a small amount of rebar was used to reinforce the foundation. Mainly in corners and just along the sides. There were 3/4" cables run throughout the foundation and the concrete was poured over that. Once the concrete set for a week or 2, a guy came by with a big hydraulic jack/press and pulled the cables to 1400 PSI and locked them in place. Cut the excess off, mixed up some concrete and covered up all the holes. You don't have to worry about cracks forming or any type of seperation due to soil shift or anything like that with this type of foundation from what information I've found.
I'm not fond of the pretensioned cable foundations. I had one in Texas and it cracked. Actually, every one I saw there cracked.
When I built my shop, 30 x 46,

I asked my friend, a retired civil engineer who worked for the Texas Highway Department, how to build a slab and he sent me the Texas HD's specs on slab construction. I followed that and everything has been just fine. Basically, a concrete beam all the way around with rebar, beam(s) across the middle with rebar, mesh in the slab itself and pour it all at once. Concrete here is about $75/yard today. I also recommend subbing out the pouring and finishing to experts.
I'm in Texas. LOL Apparently they're doing it that way around here because of the soil condition. My foundation does have rebar inserts in the footers and perimeter, but no mesh in the center.
The pretension thing has been used in Charleston SC for years but in a slightly different way: they are called 'earthquake bolts' and are used to help keep a masonry wall together during a temblor.
