We have a press at work, with a pinhole in the hydraulic system. It's buried in a location that would be a nightmare to remove the part, so I'm looking for options to plug the leak. JB Weld doesn't work.
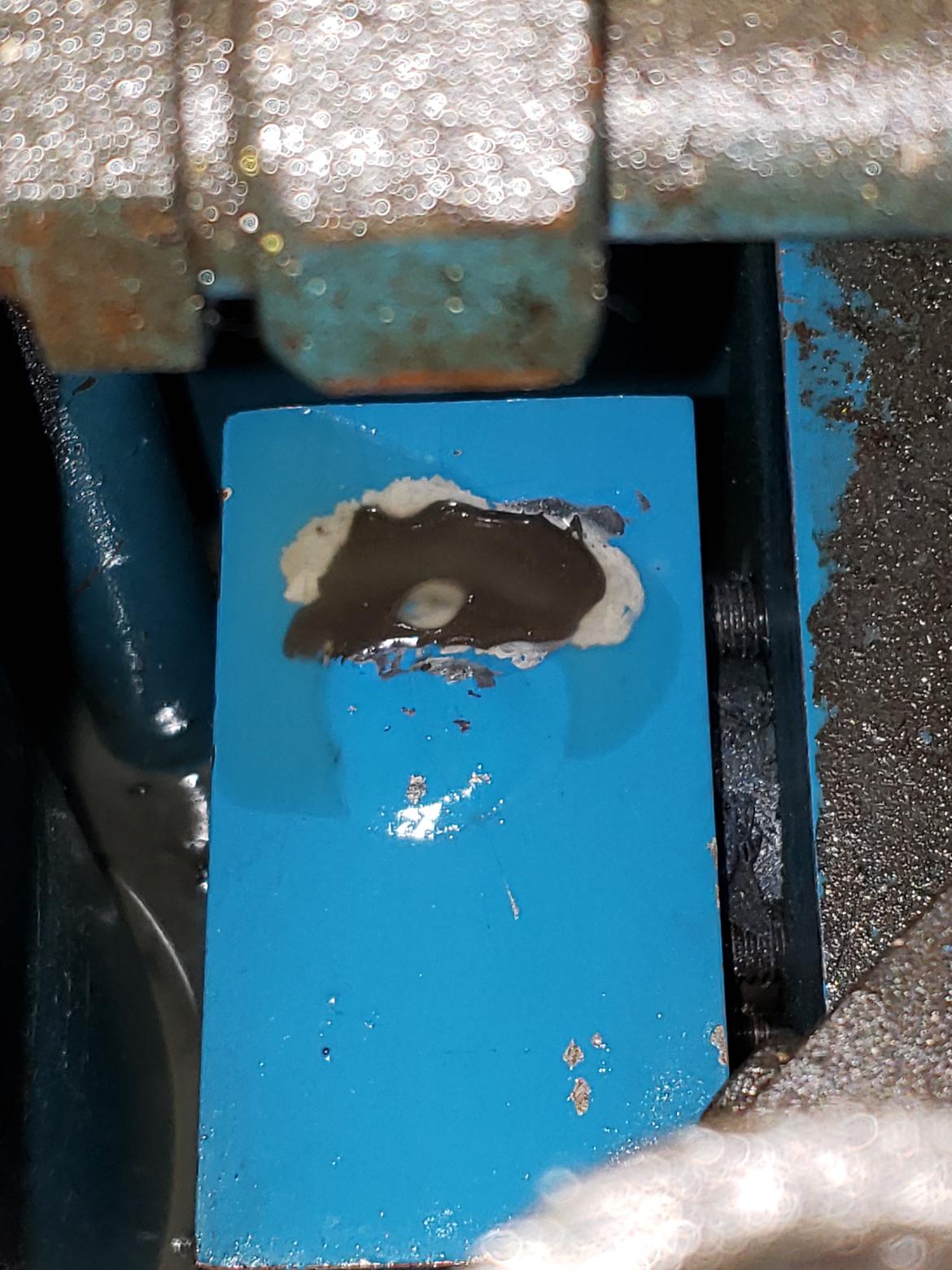
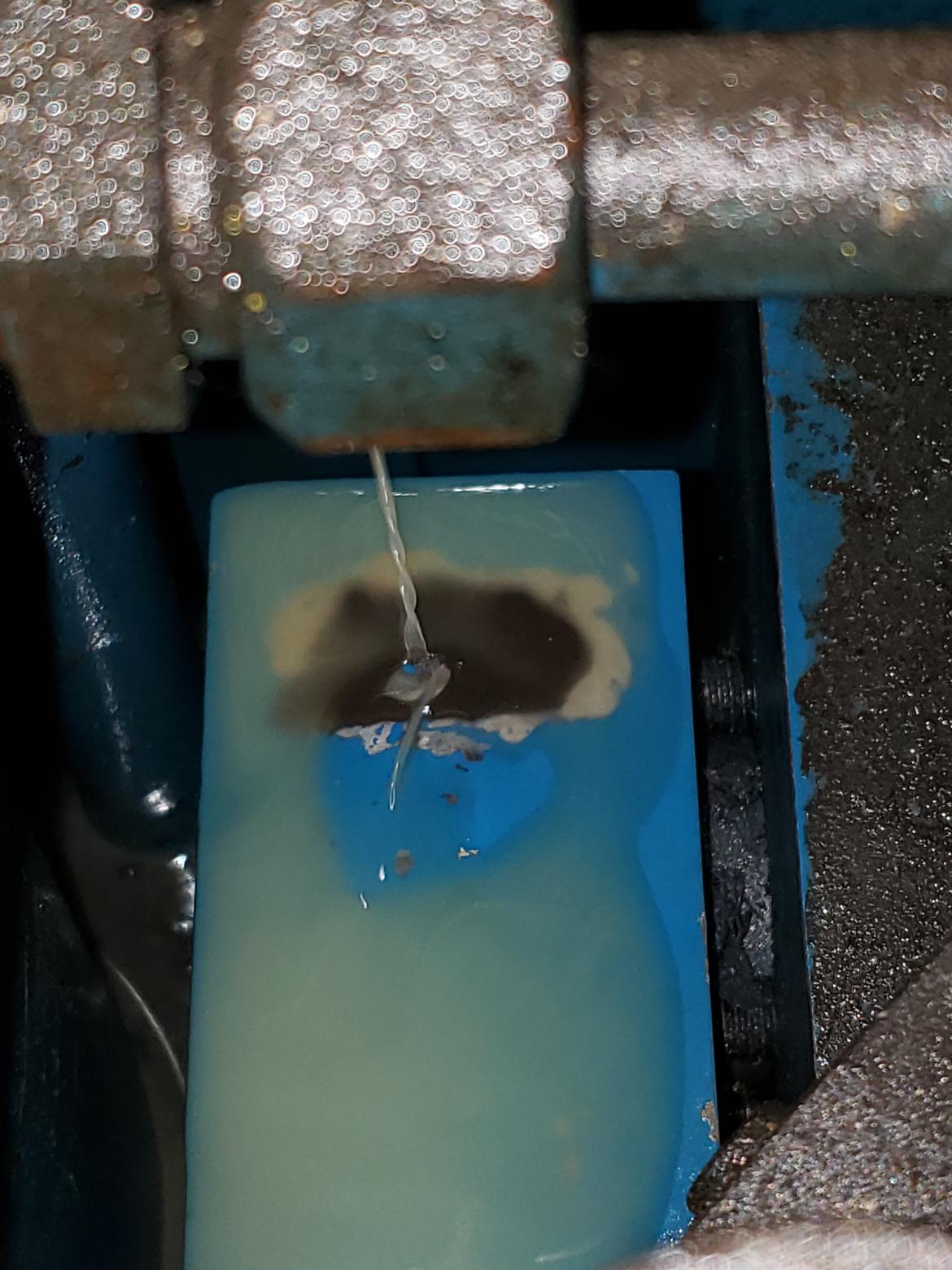
It's not part of the sump, but part of the pressure side, as you can see (along with a blob of JB that said "nah, berk it"). It is steel, but I'm hesitant to put heat or spark to it.
What would GRM do?
Take it apart and fix it correctly.
STM317
UltraDork
8/5/19 7:49 a.m.
What part is leaking? A flexible hose? A thin walled tube? A thicker walled pipe? A fitting with a bad seal?
In reply to bigdaddylee82 :
I would if I could, but it appears that the cabinet was welded around the pump assembly, essentially rendering it unserviceable. I've looked at it up, down, and sideways, and can't see any way to get the damn thing apart.
Plus, parts are obsolete.
In reply to STM317 :
The part is a steel block, circled in red, with the pinhole circled in yellow.
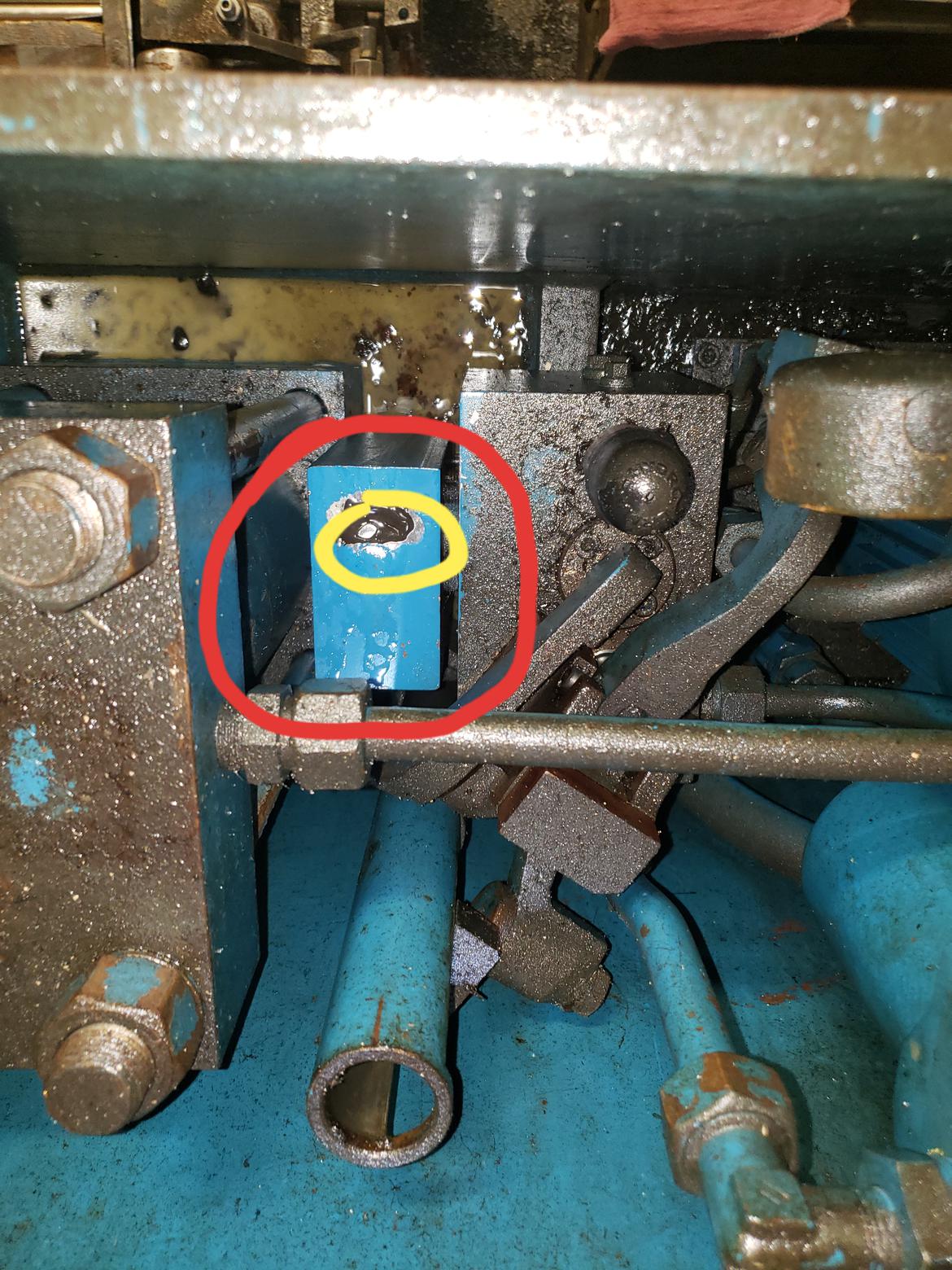
These pictures are all looking down, into the machine.
STM317
UltraDork
8/5/19 8:40 a.m.
Is there enough wall thickness to drill/tap/plug?
STM317 said:
Is there enough wall thickness to drill/tap/plug?
This.
Drill, tap, machine screw with some JB weld.
Toyman01 said:
STM317 said:
Is there enough wall thickness to drill/tap/plug?
This.
Drill, tap, machine screw with some JB weld.
Bingo, that was my first thought as well.
Of course one must wonder just how it decided to leak there in the first place. Porous casting? Any idea what kind of pressure is running back there? Any way to find an exploded parts diagram to see what is on the other side of that flat face?
And you’re gonna want to make sure P=0 before drilling into it
D2W
HalfDork
8/5/19 11:11 a.m.
Can you give any more info on what that part is or does. There may not be enough wall thickness to drill and tap. If it did have a thick wall it is highly unlikely that it would have cracked in the first place. Is it cast, aluminum, ductile? It appears to be bolted to the other part? How hard would it be to remove, and fix correctly. I'm afraid that trying to drill and tap will be a huge waste of time.
Perhaps make a rectangular plate retained with 4 screws in tapped holes where you can be confident of enough material to tap. The face of the square plate gets an O ring groove located to surround the leak point. Need to glue the O ring to the plate to insure it stays in position. I am thinking 10-32 allen cap screws in the corners, but I am not sure of the scale I see.
How much pressure are you dealing with?
You might be able to make something like one of those pipe repair clamps provided you have clearance.
Two plates, rubber face on one, 2 or 4 bolts, then tension them up to seal off the hole.
Solder or brazing would probably be the best long term.
Basic hydraulic is in the 3000psi area but I’m not familiar with this application.
It's steel, possibly iron? Definitely magnetic. The block is roughly 2x4x5". I have a sonic thickness reader, but I didn't have a chance to get into it this afternoon.
Getting the part out would entail disassembly of the whole machine. Berk that. I'm trying to come up with an in-situ solution.
Could be a valve body or a manifold. Be careful drilling it if you go that route. The hole looks more like a slot than a round. Possibly a spring has worn through the block?
Can you get pictures of the other end of the block? Is there any obvious control or fitting on the other end?
The good thing about hydraulics is that when they do fail, the failure is low-energy, as fluid is incompressible.
The bad thing about hydraulics is that when they do fail, if parts of your body are near the failure point, you can be injected with that high-pressure stream before it BECOMES a low-energy failure.
Hydraulic injection is a NASTY injury...skin must be opened up to expose the damage, tissue debraded and often removed, with subsequent potential loss of limb.
Sometimes it's far better to replace obsolete equipment wholesale if it's needed for production and you don't have time for maintenance/repair/rebuild. YMMV.
From someone who has dealt with hydraulics from 3,000-80,000psi+ in industrial applications for most of the last 20 years.
D2W
HalfDork
8/6/19 8:36 a.m.
If you are intent on fixing it in the machine. Clean all the oil and dirt off the part. Also remove the paint around the hole. Get a small piece of scrap metal and weld over the top of the hole.
Getting the oil away from the weld is critical as it will never seal with oil in the weld. I would use a round slug so I could weld it up in one pass.