I'm surprised no one has mentioned Autodesk Inventor. The team here prefers it to Solidworks, though that could be familiarity. Inventor has been a lot more stable, in my experience, but the Solidworks weldment tool seems head and shoulders over any similar in Inventor: it's pretty brilliant for some types of work. Inventor sheet metal seems to be pretty reasonable. I don't find myself running CAD much these days. We're going machine design, pump stations, small structures, lifting/transport frames etc. FEA is in Strand7 , ANSYS or Abaqus depending on the application.
In reply to tuna55 :
Are we talking contract or full time? I have a pretty good gig at the moment.
Back to the discussion at hand, NX is probably awesome, I just haven't used it.
Teamcenter, that I have used. It's powerful. It is a complete PLM-ERP-PDM-purchasing-tie your shoelaces system. Here's the rub. You need purchasing, manufacturing, maintenance, pretty much the whole organization to jump on board or all those "enterprise" tools are going to sit on the shelf. I experienced that at my former, large, global company: Oracle for purchasing, IBM Mossimo for maintenance and shop work, TeamCenter for engineering... probably a few more in the background.
Ne'r the twain did meet.
Each one of those is a complete "enterprise" system with file storage and viewer capabilities. To add to the fun, we were using SolidWorks with the TeamCenter with a 3rd party plugin to make it work. When it worked, it was ok. When it didn't, well, it broke a lot of stuff. Legacy data was problematic. They overwrote a lot of fields during some updates. Fun times!
tuna55
MegaDork
8/13/24 1:23 p.m.
In reply to tester (Forum Supporter) :
Definitely need full time, but I probably can't afford you (and you're likely still geographically constrained)
In reply to tuna55 :
Yep. I have family obligations down here.
prodarwin said:
Just had an epic NX battle where I ran into limitation after limitation after limitation. If one of you SW guys wants to give modeling this part a try I'd be curious how well it handles it. Not a common usage by any means (this is just a personal part I wanted to 3D print) and most of these issues wouldn't impact me day to day.
Hexagonal patterns are hard
Certain dimensions (perimeter) don't give you the option of making them reference only
Draft feature only drafts along vector
Circular patterns do not give option to stagger
Get enough formula driven dimensions in a model and stuff gets really wonky
This is one of those things where it almost makes sense to use Grasshopper/Rhino.
Solidworks guy here.
-Hex patterns of features are relatively easy, you can do a sketch driven pattern OR a circular pattern and define 6 points around a centroid feature.
-Any dimension can be reference only or you can make a fully defined reference sketch and then use it as a definition point for your main sketches.
-Draft is easiest defined by planes but can be defined by direction as well. Draft can be independent by faces but will eventually get pretty wonky. Standard drafted parts is straight forward.
-Circular patterns can be staggered using either skip feature option (if you want them say every 18 degrees but skipping a few along the way) or can be individually varied by degrees if you need just a few oddballs (every feature on 18 degrees but one on 15 degrees/21 degrees). Very simple single dialog box.
-Formula driven dimensions can either be through a table or typing equations at point of use, but I try to avoid them and just use centerlines and stuff. Only place I have used formula driven dimensions is on configurable models that dont have to work correctly for sales models, not for production stuff, but our use case is 100% custom stuff so very little value to us to reuse designs other than save-as.
Long story short seems simple enough to make this part in Solidworks.
Here's the part if you want to give it a try:
Note that the hex pattern must end with the "tip" of the hexagons exactly on the line of the flat protrusion on both sides. Each hex is "drafted" at a 45 deg angle perpendicular to outer surface of the cylinder.
Obviously I can create it in NX. The issue is now, although its parametric, some of the parameters are a lot of manual effort. I can't easily change the pattern from 10 hexs on the circumference to 12 for example without some manual effort. Same with defining the length of the pattern. If I were designing this like every other part I design, the key dimensions (like diameter, length of flat protrusion, height, etc) would drive everything downstream of them with no more user input needed for tweaks. This doesn't work that way.
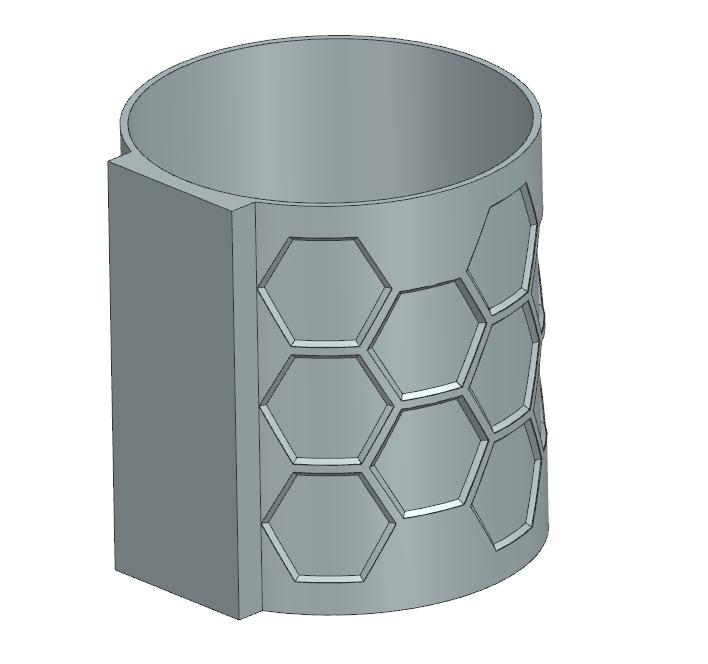
That pattern looks like it might be a good candidate for Algorithmic Modeling.
yeah, thats why I mentioned Grasshopper earlier.
*I work for MegaCorp™ and I have no idea which license bundle I would need to load to get to algorithmic modeling and it would probably require divine intervention to get access.
I tried making this in solidworks but got called away to a meeting.
The main body is super simple single feature.
The hexagons were a bit of a challenge, had to make them as a wrap with a sketch plane and a pattern defined by the circumference less the little blocky thing, which wasnt too hard but took some more sketches.
The draft was easy, chamfer feature got it did. I had to do every hexagon as a unique feature and play with the offsets to get it looking right, that pissed me off. There is likely an easier way to do it with surfaces but solidworks doesnt like draft on non-planar surfaces. Depending on if you want to scale this by adding more hexagons of the same size (Hard) or bigger hexagons (easy), this is a workable solution.
Then solidworks hung and I went to a meeting.
If I knew more of the design constraints and what was supposed to be parametrically linked and my boss was paying me to do this and not yell at customers, I probably could have gotten further.
You are describing basically the way I ended up doing it in NX. Ideally I'd model one hex, drafted, radiused, etc. exactly how I want, then just pattern it around. But because hex patterns are a bitch, I ended up doing a wrapped sketch, chamfer, etc. etc.
When I think of the ideal parametric scenario, picture a part family. Cylinder radius, height, width of block extension, and number of columns and/or size of hex as being the only variables.
prodarwin said:
You are describing basically the way I ended up doing it in NX. Ideally I'd model one hex, drafted, radiused, etc. exactly how I want, then just pattern it around. But because hex patterns are a bitch, I ended up doing a wrapped sketch, chamfer, etc. etc.
When I think of the ideal parametric scenario, picture a part family. Cylinder radius, height, width of block extension, and number of columns and/or size of hex as being the only variables.
Solidworks does have the boundry fill pattern, but its a bit of a pain in this instance because of the cylinder.
This part would be very very easy to model if you could allow a thin cut in the part and use the sheetmetal "flatten" feature to do the hexes on a plane and then unflatten it.
Hmmmm Got me thinking now.
93gsxturbo said:
prodarwin said:
You are describing basically the way I ended up doing it in NX. Ideally I'd model one hex, drafted, radiused, etc. exactly how I want, then just pattern it around. But because hex patterns are a bitch, I ended up doing a wrapped sketch, chamfer, etc. etc.
When I think of the ideal parametric scenario, picture a part family. Cylinder radius, height, width of block extension, and number of columns and/or size of hex as being the only variables.
Solidworks does have the boundry fill pattern, but its a bit of a pain in this instance because of the cylinder.
This part would be very very easy to model if you could allow a thin cut in the part and use the sheetmetal "flatten" feature to do the hexes on a plane and then unflatten it.
Hmmmm Got me thinking now.
Tried this, doesn't work. Hexes blow up when part is re-un-flattened.
In reply to 93gsxturbo :
Looks like a fun puzzle. I will give it a try over the weekend.
tuna55
MegaDork
8/23/24 1:58 p.m.
Using Solidworks because that's what we have now, but wow it's primitive. It doesn't combine bodies well at all.
I'll throw this into the mix... for schematics we've been using KiCad. Best part, it's free!
tuna55
MegaDork
8/23/24 2:47 p.m.
Nathan JansenvanDoorn said:
I'm surprised no one has mentioned Autodesk Inventor. The team here prefers it to Solidworks, though that could be familiarity. Inventor has been a lot more stable, in my experience, but the Solidworks weldment tool seems head and shoulders over any similar in Inventor: it's pretty brilliant for some types of work. Inventor sheet metal seems to be pretty reasonable. I don't find myself running CAD much these days. We're going machine design, pump stations, small structures, lifting/transport frames etc. FEA is in Strand7 , ANSYS or Abaqus depending on the application.
Will try it. Nx has a steeper learning curve for me through the trial
tuna55 said:
Using Solidworks because that's what we have now, but wow it's primitive. It doesn't combine bodies well at all.
What features are you trying to combine? You may have better success checking the "merge" box during body creation vs trying to combine things in a separate item on the feature tree.