Could you increase CFM output of a compressor by doing work to the pump like you do a motor?
I imagine changing the compression ratio of the compressor pump would change output, but I'm not sure in what ways.
It would just be nice to squeeze a little more air than 6.2@125.
I suppose you could, but compressors don't have a throttle or an RPM band. Changes to an IC engine make power (increase flow) at certain RPMs, thereby shifting the peak RPM band to a different range. The result is you have to rev to different RPMs to take advantage of the efficiencies you've changed.
You'll have to be careful how you alter it. Compressors are pretty well matched to (for instance) 1800 rpms. So let's say you port the head on your compressor. You might reduce its efficiency unless you increase the speed.
On individual aspects:
Increasing the compression ratio in an IC engine works because the added energy from compression facilitates increased thermal efficiency from combustion. That is to say; the added use of energy from increasing compression pays off in a net win of more BTUs being converted to pressure seen by the piston after combustion. Compression ratio tends to make more cylinder pressure after ignition than it uses creating pressure before. In a compressor situation, increasing CR isn't really a thing. It functions as a 2-stroke pump. The compression stroke isn't compressing a fuel/air charge in preparation for combustion, its sucking in one valve and pushing out a second valve. The compression ratio is not a function of displacement versus chamber volume, its a function of displacement versus tank volume. The compression stroke is open to the tank, not trapped in the cylinder awaiting a combustion event.
Porting an IC engine works to increase bulk flow with the by-product of reducing port velocity which is why it shifts RPM range up in the band. Porting a compressor would only increase efficiency IF the ports were a restriction to flow. Since compressors don't rely on broad ranges of RPM operation, they can basically be wide open to flow. Often you'll notice that most compressors have a filter and a reed valve right on top of the head. There isn't much to be improved.
In an IC engine, you have to think of it as a self-fueled air pump that makes power as a by-product. In a compressor, you have a passive pump that is driven by external power. For the most part the compressor unit is a simple displacement pump capable of X pressure and Y cfm. The way to increase performance is to either up the power you put into it (within operational capacities of the pump) or to increase the displacement of the pump (within the parameters of the power you have to supply it).
In short, the easy way is to spin it faster as long as it can handle it, AND make sure it has the peak power from its source to handle the peak pressures.
Let's put it this way: Let's say you have a 6.2 cfm/125 psi setup. The CFM is set mostly by the displacement of the compressor. The peak pressure is set primarily by the capacity of the tank. Since CFM drops as pressure rises, peak pressure is also set by where the compressor starts to significantly drop CFM. So if your compressor operates at 1800 rpm, and you have a 5 hp motor and it makes 6.2 CFM, lets theorize swapping out the electric motor for a Chevy 350 at 1800 rpms. Nothing will change. You'll still have a 6.2 CFM compressor that shuts off at 125 psi. But if you quadruple the size of the compressor because you have the power to back it up, you now have a 25 CFM compressor at 125 psi.
The cfm is determined more about the displacement of the pump than anything else. No matter what you do, a certain size pump is going to pump the same amount of air if everything is working correctly. If you want more flow, you need to a bigger pump.
I feel like this is a "no replacement for displacement" situation.
Changing the pulleys would be the obvious first choice to increase output...but may lead to other problems, necessitate a higher HP motor, cause excessive heat, etc.
You would probably would have trouble quantifying any increase in performance, esp. in real world situations.
That's kind of what I was getting at. Can I increase the displacement of the pump or just hunt for a bigger one?
For my particular pump, there are several similar models, with what appear to be interchangeable parts, but very different specs.I'm not sure how different the parts are between models honestly, but I was thinking maybe a bigger pump head and smaller valves with porting of the air ways could get some more air through at the same speed. $50 in parts vs $500 in pump.
Maybe you can add a second compressor? I have a twin pump Jun-Air.
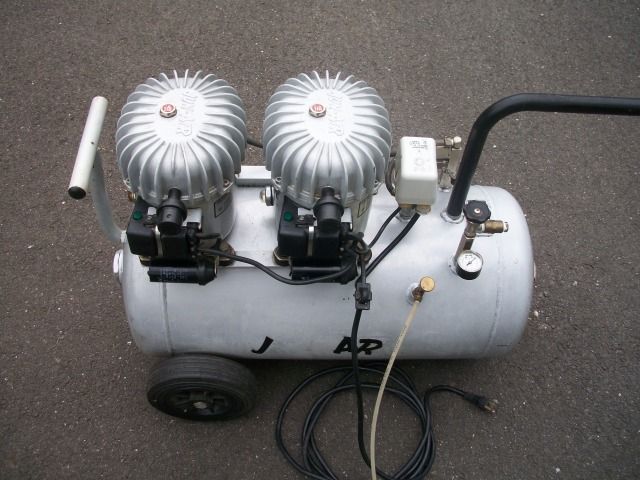
The relief valve on the tank is sized to be able to flow more air than the compressor puts out. Put a bigger pump on and you may have to replace the valve too.
oldopelguy said:
The relief valve on the tank is sized to be able to flow more air than the compressor puts out. Put a bigger pump on and you may have to replace the valve too.
wrap the tank with duct tape. Bingo. A full-flow relief valve. It will also be very easy to tell if the relief valve has opened by the very massive explosion.