Heres how I spent my morning:
built a fire in my furnace:
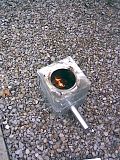
then I melted some scrap Aluminum:
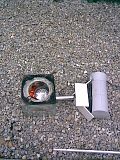
Filing my fancy pants crucible with shiny goodness:
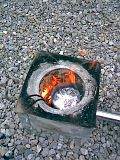
And cast some ingots in a mini muffin pan:
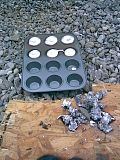
And let em cool till I could hold it in my hand:
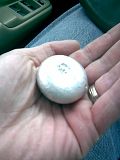
That melt produced 6 ingots at a total of 4.5 lbs. This was my first firing and my first attempt at back yard metal casting. Id say I did an alright job if I do say so myself, and I do. I built a furnace for free, used $10 worth of kitchen stuff, burned scrap lumber I already own but had no use for, and melted some metal I woulda thrown away otherwise. Not too shabby.
I got jazzed on the idea from a thread a few months back where someone wanted a decorative timing cover without a lot of cost. Cant remember the details, but I was hooked after looking into it and finding backyardmetalcasting.com.
Ideally I want to build my own metal working lathe, and cast/fabricate my own aluminum underdrive pulleys, make some universal shift knobs, and maybe some decorative placques and other hullabaloo. Theres miles to go before I get to that point, but you gotta start somewhere.
What you need now is a good slingshot 
EastCoastMojo wrote:
What you need now is a good slingshot
or a potato gun, whichever...
RossD
Reader
7/30/09 8:06 p.m.
I'd have to admitt, that looks all the way cool. I've often wanted to makes my own castings since I worked at a pattern shop back in high school. Now you can make knock off Hurst shifter handles that say "Horst". 
NYG95GA
SuperDork
7/31/09 4:58 a.m.
That's major cool.
Well, once you can hold it in your hand..
Very cool, but I might hesitate before making pulleys. I wouldn't want to machine something that rotates at crank speed out of a billet that I cast myself.
I'm just sayin'...
my high school had a foundry and we packed sand molds and then poured them at the end of class.
Since it was the late 1970's; a lot of belt buckles were made. But I still remember enjoying the foundry work. The rest of the class was lathe/mill/drill/welding. Metals I, II, III, IV.
They have since removed all that equipment from my high school, because I think it is now illegal to teach this stuff.
Dude. That's really, really, really cool.
In my junior high metal shop class, we made chisels, sheet metal tool boxes, and did some casting.
No welding except for the spot welds, and no machine work, though.
Now the old shop full of computers and a small robotics lab.
No shop in my highschool.
The closest thing is a robotics program. They have some tools, but...
Here's my favorite scoldings from the past year:
"Tommy! You could hurt yourself with that screwdriver. You have to wear safety goggles."
"Tommy! You need a fire extinguisher next to that. And gloves!" (watching someone drill a hole in a piece of metal in a vice on a drill press)
etc, etc.
Of course, we weren't allowed to use any of the tools except the screwdrivers until we were 18. Even vice grips. I had to show a lot of the 18 year olds how to use the tools.
My high school had a metal shop. They cast a lot of stuff out of aluminum, soldered, welded, etc.
Combine the recent high school observations with the fact that Vice Grips (r) are now made in China and the conclusion is that we are totally screwed.
Hey, 4cylndrfury, what are you using for a crucible?
Tommy Suddard wrote:
No shop in my highschool.
The closest thing is a robotics program. They have some tools, but...
Here's my favorite scoldings from the past year:
"Tommy! You could hurt yourself with that screwdriver. You have to wear safety goggles."
"Tommy! You need a fire extinguisher next to that. And gloves!" (watching someone drill a hole in a piece of metal in a vice on a drill press)
etc, etc.
Of course, we weren't allowed to use any of the tools except the screwdrivers until we were 18. Even vice grips. I had to show a lot of the 18 year olds how to use the tools.
This makes me a sad panda...
Metal casting = way cool! I want to try casting my own bullets for reloading someday.
My high school had shop classes, but they were at the career center, for folks who knew they weren't going to go to college. It was such horsepuckey. I really wanted to take the classes but I also wanted to take AP classes for college...in retrospect I think the shop classes would've served me better!
Making boolits yourself is easy, inexpensive and straight forward. You can roll your own for basically free to a penny each (including lube). I've been doing it myself since I was 13. With the price of store-bought boolits and bullets these days, there isn't much other choice.
the link was so badass that I just wasted 35 mins of company time.
that looks like fun.
cb
Reader
8/20/09 6:43 p.m.
would a burner from an old grill make enough heat?
Tommy Suddard wrote:
Of course, we weren't allowed to use any of the tools except the screwdrivers until we were 18. Even vice grips. I had to show a lot of the 18 year olds how to use the tools.
I see the Nintendo generation every few months in the new Machinist apprentice classes. A few couldn't figure out how to get a chuck key into a drill press chuck. No mechanical experience.
Yes, sad.
cb wrote:
would a burner from an old grill make enough heat?
Probably, aluminum melts at 1220' F.
[pssst. Don't use an aluminum pot/i]
dunno why thats all in italics?^^
OK, another update...
Im trying to build a burner for my furnace that will burn waste vegetable oil from a local fast food joint. Its a very clean combustion if you can get it to atomize in enough air. In order to move said air I need a blower. Well, I have an old vacuum cleaner whose motor works but the plastic housing cracked ruining the impeller, so it wasnt getting suction... bingo - motor for a blower. now Im gonna cast 2 plates that will sandwich a center housing that will form a crude blower housing, and using the impeller from my recently deceased sump pump, Im hoping to create enough pressure on a small volume - forcing the air through a 1 1/2" square tube with a venturi at the end tapering to a 1/4" hole, and gravity feeding the oil into the venturi about 1" behind the orifice.
ok, so heres the photos -
the plate:
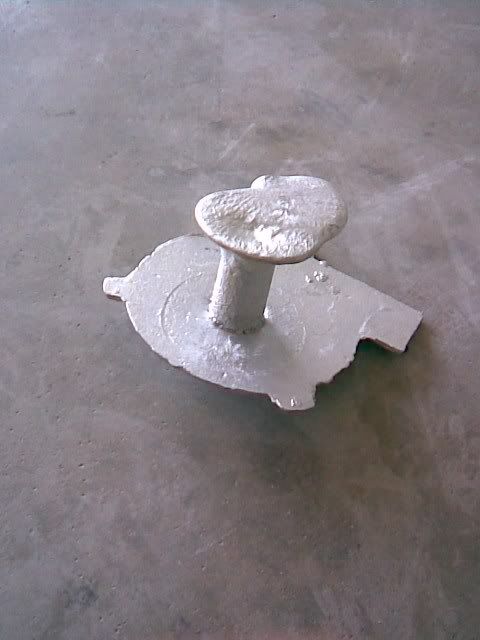
Its pretty thin - 3/16" or so:
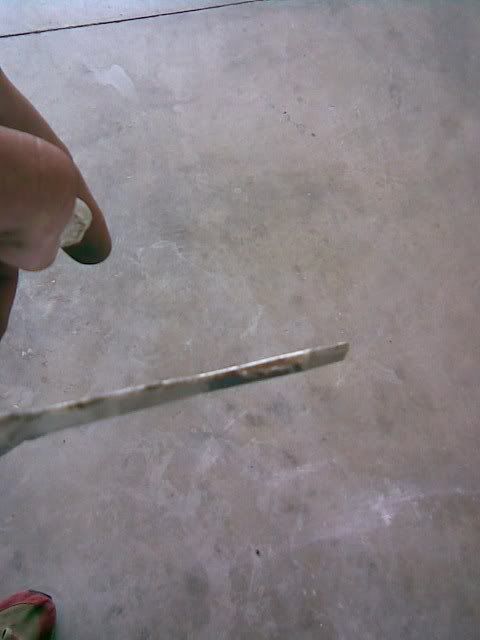
Anyway, theres something elemental feeling about melting metal and using a technology as old as the bible to turn that metal into something useful...well except for the electric blowers and stamped stainless steel crucibles and what not
LOL still not sure about the ITALICS????