I want to learn (teach myself though YouTube and other online sources) how to machine things. Small plastic bushings. Door pulls for cabinets. Radio block off plates. All sorts of small things, most of which are small enough to fit in my hand. Made of plastic/wood/aluminum soft stuff initially.
Do I want a small lathe? A mini mill with a rotary table? A good book to start the thinking process?
I know I want to stay 110v. I don't have 220v in the Grosh right now and in an ideal world small machines would live in the basement of my cottage someday so I would have something interesting to do inside in the winter. Cheaper is better, but I'm always willing to spend more for quality especially if the results are better.
A vertical mill probably does more car-guy kind of stuff. The kind of lathe you'd need to be useful for the kind of car-guy things that require a lathe is going to be huge, and three-phase.
I have used a drill press as a lathe for booger-machining plastic items. For example, I made a shift ball for my Golf by drilling a shift shaft sized hole in a hockey puck, then threading a bolt and nut into the hole, chucking the bolt into the drill press, then using a file to get the ball size/contour right. It actually worked really well aside from HUGE amounts of cleanup afterwards. And the shift ball lasted forever.
Lathe, something like a South Bend 9 inch or a 9-12 inch import lathe would probably work well for you. Learn what to look for when buying one (most notably wear on the bed ways, a tired lathe will turn footballs near the headstock).
EDIT: I say this as somebody who has learned the basics on both and currently has access to neither, I think "wow a lathe would be handy right now" a lot more often than a mill. Half the stuff people like to do on Bridgeports and smaller mill drills (locate and drill holes in things) can be done, albeit a bit more slowly, with a halfass decent drill press and some basic layout tools.
Watch for worn lead screws on a mill also.
Rufledt
UltraDork
12/18/16 2:24 p.m.
Might I suggest the Gingery Book Series?

or in single tome format:

I freaking LOVE that book.
On the other hand if you just want to buy one and not spend years of your life making what is likely a less-capable machine, i have no useful information to present.
If you get one and learn to use it, post videos. i wanna see!
You really want both.
A lathe generally has more versatility than a mill - including doing some light milling on it of you mount a vise on the cross slide but there are times when there is just no substitute for a mill. I do not have one yet and have passed over cool racecar and other fab projects that would have been easy if I could have just cut a keyway or a few slots. Little things like making T-Nuts for the bed rail system of my truck out of HDPE cutting boards... they are $15 a pair. I could make 20 in an hour with a $6 cutting board if I just had a mill.
I have a Grizzly G9972Z lathe that I bought used for $600 with a bunch of tooling ... and bought some new gears, a turret tool holder and a few other things making it all in for a grand. My cheap Chinese lathe has been more than adequate for any work I've done, and holds some pretty tight tolerances while doing it after just a little home tuning and care. Like making a new drum shaft for my washing machine or a BMW ZF trans to Tilton hydraulic TO bearing adapter plate and a million other little things ... My hope is similar for $1700 delivered on a mill.
So... my xmas present to myself this year (well, not really, I sold a bunch of stuff off to cover it) is a Precision Matthews PM-727M http://www.machinetoolonline.com/PM727M.html
The PM-25MV mill (little brother to the one I'm ordering) saves dough and has a nice variable speed DC motor. I do believe it is 110v too. I picked the larger one mainly because of the extra space under the quill (I already own a vise but it's tall/huge and would eat up workspace) but might change my mind again before finally pulling the trigger.
Despite a million people telling me to buy a used Bridgeport ... those things are massive, heavy, and typically $2500 before shipping. Not that they aren't much more rigid in every way - they are gross overkill for the kinds of things I do. Slotting aluminum, making bushings in HDPE or nylon, drill/tap a circumference... etc. It just won't fit in my garage and still allow the cars inside and room to work. If you have the space and want to do BIG work like hogging a 4" trench in steel with one pass - then I'd probably go that route.
In reply to mazdeuce:
You need to speak with MotoMoron.
I would say lathe. I use the lathe twice as often as I use the mill, as a mill. It spends most of it time as a huge, cumbersome, overly powerful, drill press.
I started out with a Taig lathe. http://www.taigtools.com/
It will make a surprising amount of things. I've even turned a set of backhoe pins on mine. It will not cut things quickly, but it will cut just about anything. It has since been passed on to my eldest. It's a cheap starting point if you want to try it out without breaking the bank.
My primary lathe now is a Southbend 9A tool room lathe. It's a 1947 that I restored. It's probably one of my favorite tools. It's belt drive, so a little more forgiving than a gear drive lathe.
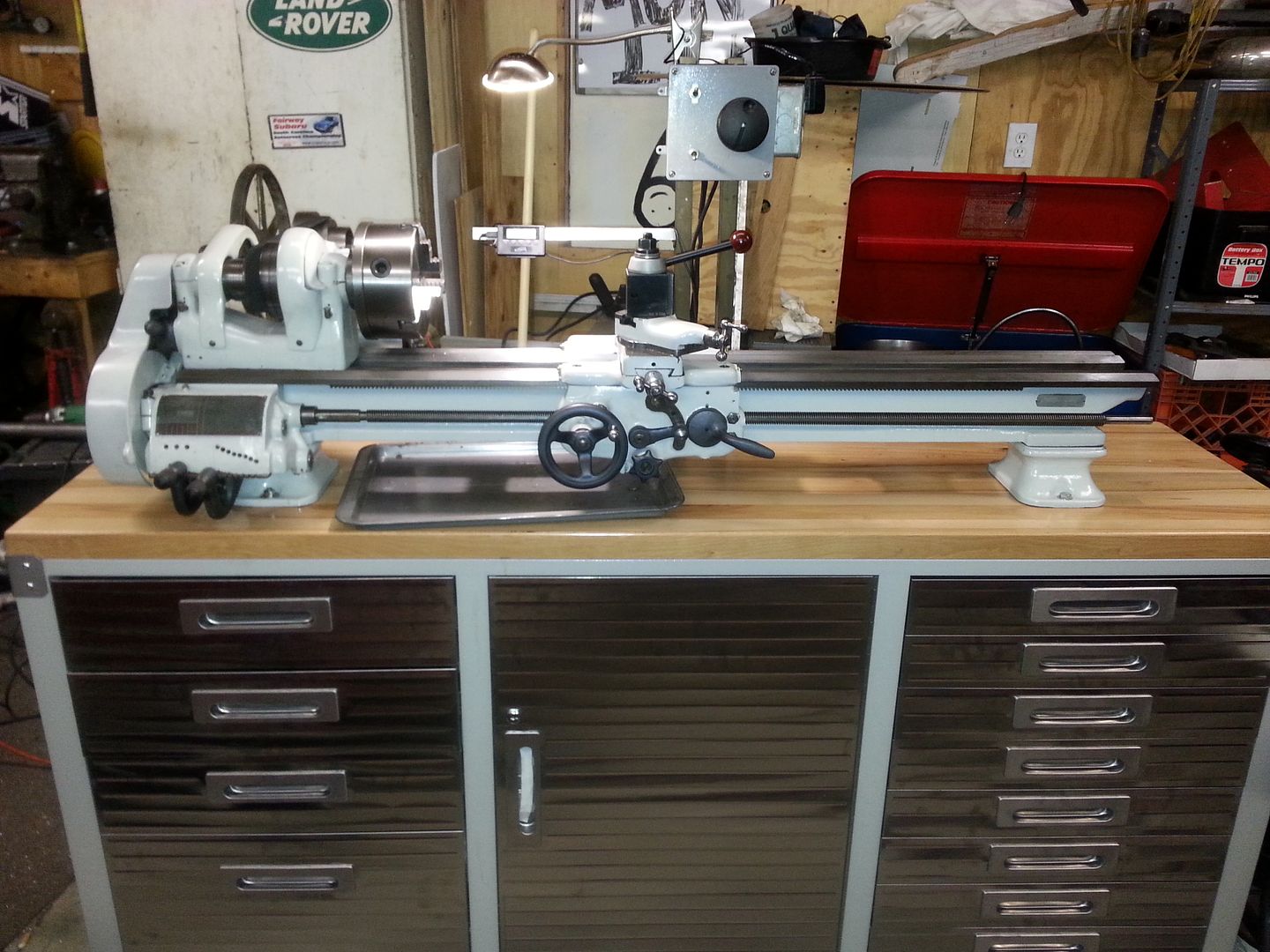
Remember the tool is the cheap part. The above lathe cost me $400. There is $2500+ in tooling, chucks, and instruments, in the cabinet below it.
In reply to Huckleberry:
Huge thanks. I tend to think 90% of what I want to make, like steering column bushings for Fergus that are NLA, can be made with a small lathe. If I get all wrapped up in it then I can always add a mill later.
Toyman01 wrote:
I would say lathe. I use the lathe twice as often as I use the mill, as a mill. It spends most of it time as a huge, cumbersome, overly powerful, drill press.
I started out with a Taig lathe. http://www.taigtools.com/
Remember the tool is the cheap part. The above lathe cost me $400. There is $2500+ in tooling, chucks, and instruments, in the cabinet below it.
Thanks. I'll take a look at that. And yes, the tooling and such is clearly the expensive part long term, but atmleast the majority of that transfers from lathe the lathe if I were to upgrade.
In reply to Toyman01:
I have that exact same cabinet. It cost almost half what I have in the lathe at $400 from Sam's Club. I didn't buy a ton of new tooling - but I easily have $1000 in used stuff in that cabinet. Watching CL for whole shop sales or estate auctions and you can score a lot of nifty stuff in a box for $50 at a time.
I got about 20 end mills and a set of R8 collets in a cool wood box at a yard sale for $20 last fall.
In reply to mazdeuce:
It won't if you start out with a small lathe like the Taig. All the collets and such won't fit a larger lathe, so if you are thinking big, go big now. It really depends on what you want to make.
With riser blocks, the Taig will turn 6" material. With the long bed, it will turn 15" long stuff. I turned a set of backhoe pins for a friend on mine on the Taig. It took several hours. With the South Bend, it would have taken less than an hour. Small tools are great, but there is a trade off.
In reply to Huckleberry:
When I picked up my lathe, it came with a 1947 lantern tool holder and all the crap that goes with it. It didn't take me long to scrap the whole mess and buy a quick change tool holder. Then you know you need all the new tooling to go with it...and that new boring bar...and a set of digital readouts...and a new 4 jaw chuck...and a new 3 jaw chuck...and...a set of cutter blanks so you can make that tool you need...
Then you pick up a mill and it's collet time, and fly cutter time, and end mills, and ball mills, and center finders, and...
It's a vicious cycle.
Fun though. 
And the best part is being able to walk out into the shop and build or fix anything. 
Toyman01 wrote:
And the best part is being able to walk out into the shop and build or fix anything.
Both blessing and curse. I spent about 16 hours making a new shaft (twice because I'm a terrible machinist) for my washing machine when it spun a bearing and ruined the old part. Because I could.
People who spent the $159 and just re-assembled the washer had a whole weekend left to wash clothes in it.
In reply to Huckleberry:
Yeah, but it's an enjoyable 16 hours. Well, except for the whole making it twice part.
Did you move a decimal, or try to squeak in that one more pass, so you didn't have to polish quite as much? Or even better, did you throw it across the room, bending it in the process?
BTDT.
SVreX wrote:
How about a combo unit?
I like my Smithy.
I followed the common wisdom of the interwebs when I was asking these kinds of questions which dictated getting separate machines because of setup/teardown being a big chore and the compromises inherent in the design but I have wondered many times if I wouldn't have been just fine with a combo machine. Because right now I have no mill and I think a compromised mill would have been better than none for the last few years.
Doing it over - I'd buy one as a first machine. I think I had an opportunity on a Smithy from someone on here a few years back for $400 or so and it would have done anything lathe-wise I attempted in the 1st year or two and I would have been able to make camber plates, wheel hub adapters, etc on the mill myself instead of buying them.
Someone will always buy one from you for that kind of money too - so even if you do come to outgrow or hate it... it was essentially free.
TL/DR: Sometimes the internet is wrong. A quality combo would be OK by me in hindsight.
Huckleberry wrote:
Toyman01 wrote:
And the best part is being able to walk out into the shop and build or fix anything.
Both blessing and curse. I spent about 16 hours making a new shaft (twice because I'm a terrible machinist) for my washing machine when it spun a bearing and ruined the old part. Because I could.
People who spent the $159 and just re-assembled the washer had a whole weekend left to wash clothes in it.
I'm already this guy, but I'm just frustrated because I can't build those things. At least not as well as I want to.
Years ago I took a couple of semesters of "Machine Shop" at the local community college in the evenings.
Later I got to play on some lathes, a Bridgeport Mill, and a surface grinder at a race shop that a friend was working at. The car owner encouraged volunteer crew to come to his shop to work on the car and I ended up making a lot of misc. stuff in his "machine shop". As mentioned I used the mill as a glorified drill press most of the time and any real machining I did was on the lathe.
Years later I lost access to that shop so when I decided to buy my one machine I choose a lathe. A Logan 12X24 built in the 60's. It's seen some abuse but I can hold tolerance well enough for the stuff I make.
A mil would be nice but I seem to get by without it.
Toyman01 wrote:
In reply to Huckleberry:
Yeah, but it's an enjoyable 16 hours. Well, except for the whole making it twice part.
Did you move a decimal, or try to squeak in that one more pass, so you didn't have to polish quite as much? Or even better, did you throw it across the room, bending it in the process?
BTDT.
I had the speed way down and took too much sneaking up on the goal so when I sped up to do the last smooth pass I connected all the dots and ended up with too little shaft for a press fit. I tried to TIG in some fill and turn it again but the area was too wide for my skills in that area as well. I could have used the MIG but that seemed like giving in. So... many hours of idiocy were spent before just cutting another hunk of bar and starting over. I learn like a salmon spawns. It's always upstream with waterfalls. And bears.
In reply to Huckleberry:
It's probably for the best that we only hung out for a couple of minutes that one time. If we had enough time together for one of us to get an idea, it would have been bad.
Currently looking at combo machines. I'm pretty sure I could build a cabinet that would make it look like a nice armoire.
mazdeuce wrote:
In reply to Huckleberry:
It's probably for the best that we only hung out for a couple of minutes that one time. If we had enough time together for one of us to get an idea, it would have been bad.
Currently looking at combo machines. I'm pretty sure I could build a cabinet that would make it look like a nice armoire.
Yeah - I've thought about that a few times. I regret not having put you and the boy up for the night so you didn't have to race the storm out of here. It's another teachable moment - when someone is starting an epic journey at my place I should try to contribute more to the story. Or atleast get them drunk. I mean... 8yr olds get drunk really quick so it's not like it's even that expensive. Would you like to do it again? I'll try to find another cool car to stock the garage with ... or in reverse if, ya know... you wanna sell it back for even money :)
I can say if you go multipurpose, avoid the Harbor Freight unit. It has too many compromises - no power feed for the lathe (can't cut threads) - the mill head doesn't go low enough so you have the block the work up high leading to instability - etc etc.
I did manage to turn out a shifter knob. Now it sits in my basement patiently waiting for the next widget I can pretend to "machine".

I have a Logan 10" lathe and this milling attachment set up:

There is a small X/Y milling table, a vice that can be indexed at various angles, and another gizmo that allows you to index round parts in order to cut splines or flats or what-have-you.
The most recent thing I made was this temporary replacement for the fan clutch on my friend's Mazda B1200 truck (one of only a few in the US). The clutch had seized crooked and there was not a replacement available anywhere. They sold these trucks in Oz with un-clutched fans so we figured it would be OK.
Pulley side:

Fan side:

It worked good and got him back on the road:

Go take some classes at the local
Community college. Then you'll know what you want.