Been thinking about getting one to help in measuring / designing parts. Like as an hopefully easier way to make an engine adapter plate than trying to trace the shape, then measure all the bolt holes, then draw that in CAD. Seems like it would be a quick way to get something in digital form, then off to a service like Sendcutsend.
https://store.3dmakerpro.com/products/moose-lite?gad_source=1&gclid=CjwKCAiApY-7BhBjEiwAQMrrEVNam6DG_ch_hPIzmsY--DmUvmIbmryDXdxNAsSo4la8tJoFet1TYBoCU2AQAvD_BwE
In reply to Tom Suddard :
Perfect, checking it out now.
Well not exactly right now because my GRM+ seems to be messed up. Been paying for it but it's not letting me access.
Mr_Asa
MegaDork
12/19/24 6:47 p.m.
So is an iPhone really still the best choice for semi-budget option?
NOHOME
MegaDork
12/19/24 6:48 p.m.
Would love a high level explanation of how the results from a scanner end up as a scaled and measurable drawing in say Solidworks.
The scanner seems to produce a fuzzy cloud of points. based of an origin point of some sort. That is easy to understand. But how do you import that cloud into a program like Solidworks so that you can used the data?
Mr_Asa
MegaDork
12/19/24 7:04 p.m.
In reply to NOHOME :
You only need 3 points to define a plane. If you interpolate a line between each of those points, you have created the boundaries of that particular plane and formed a triangle.
Basically the point cloud gets turned into a large number of triangles. By further interpolation you turn those triangles into a mesh, and that mesh is the equivalent of your surface.
These reasons are why you need to move the scanner, take pictures from different angles, and other things. You are gathering more points between your points.
Now, turning a surface into an actual solid object? That's something I have no clue. Generally when you bring in a surface model it is only as thick as the image. If you were to take a cross section of that surface you'd have a line. A lot of people use them as references, not as a solid model
Mr_Asa said:
So is an iPhone really still the best choice for semi-budget option?
I think only the newer iphones have Lidar which does the scanning ,
but maybe there is something else for the older Iphones without Lidar ( I hope )
I asked the support team to look at your account and chime in with a fix, dan. Sorry about that!
I didn't have success with lidar, even with the newest, shiniest iPhone. Good 'ol photogrammetry and washable spray chalk got me great results, though. Not to gatekeep, but I did explain everything in that article
.
Not grassroots, but not top of the line either, but I've gotten great results from my Revopoint Miraco. It cost me $1400, but I can apparently scan within .001".
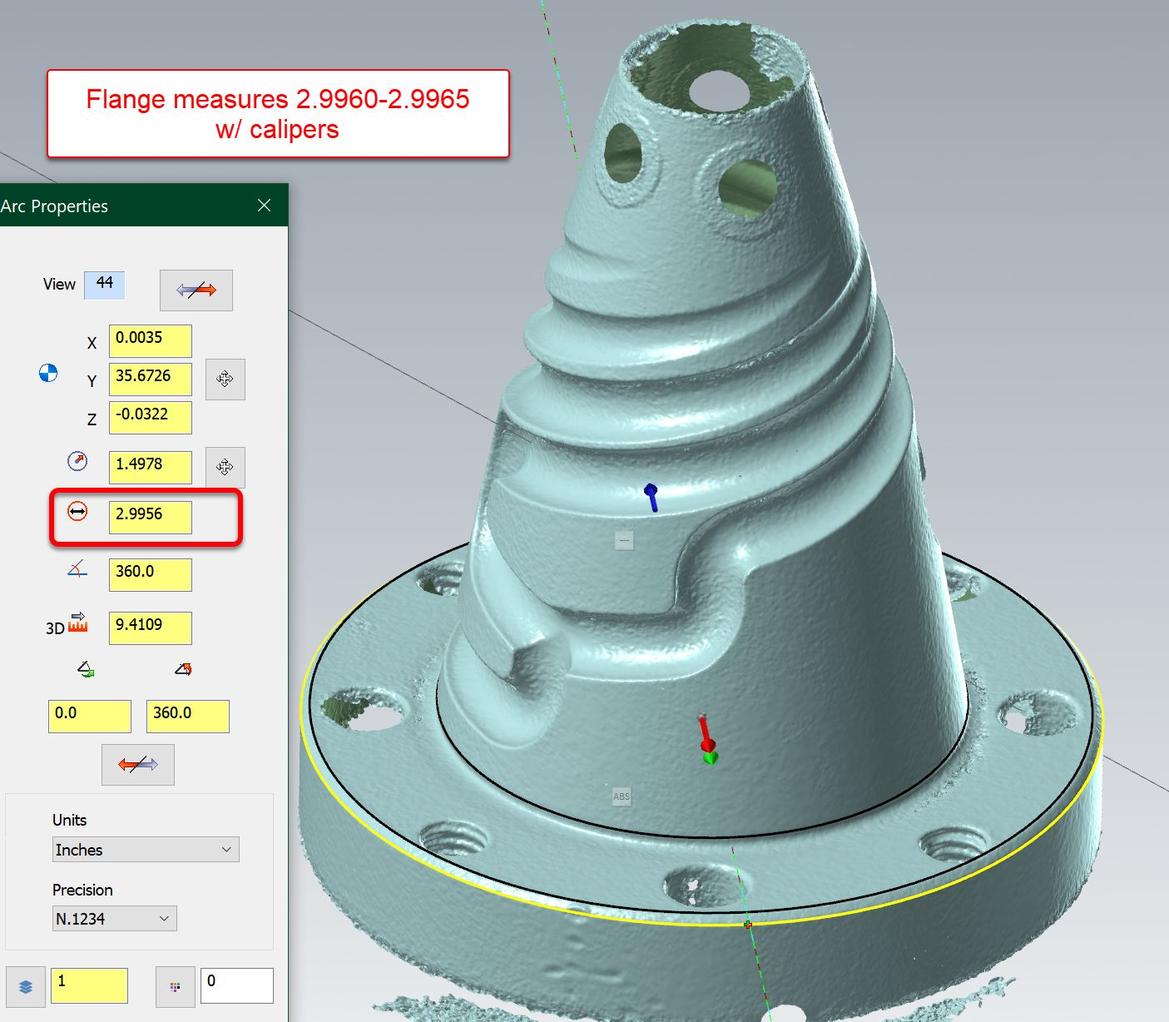
Note that this was to reverse engineer those "fingers," so I didn't bother to scan the top of the part.
You're not that far from me, you're welcome to use it over here if you need to, Dan!
In reply to WonkoTheSane :
Perfect! That's what I'm looking for. Then from there be able to "slice" that model up to get the section needed.
dan0 said:
In reply to WonkoTheSane :
Perfect! That's what I'm looking for. Then from there be able to "slice" that model up to get the section needed.
Yeah, if this is a one or two-off thing, I can do it for you so you don't have to invest in any equipment :)
If I have a mesh, it's pretty easy to slice it up and get wireframe:
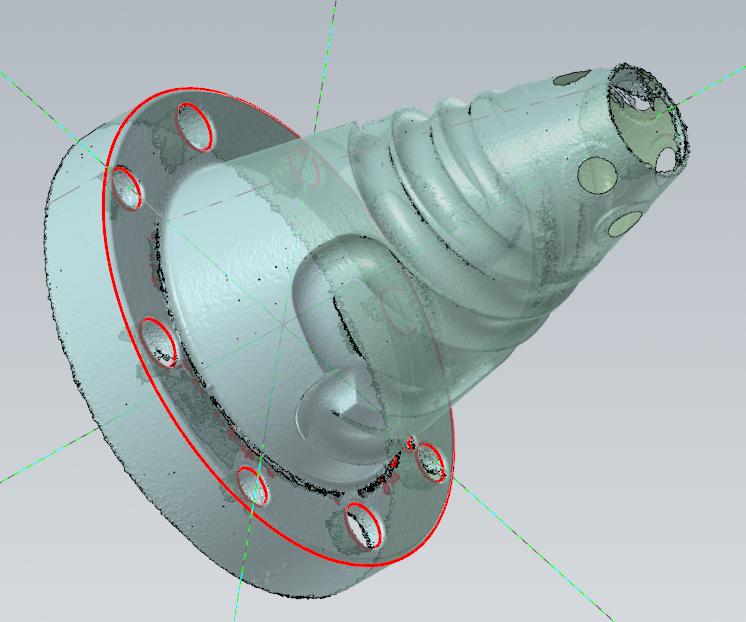
I'm over in Stafford, CT. You can email me at my <username>@gmail.com.
Mr_Asa
MegaDork
12/20/24 11:11 a.m.
I'd love a similar thing to the On The Road Assist List where those of us with scanners or whatnot post so we can figure out how to get more models out there.
I've used an Einstar scanner to scan most of a car and design powertrain swap related parts in CAD. It's been shockingly accurate, even with the accumulated error of me assembling individual components/scans in CAD. Since I have more time available at a computer than in the garage, it's been really helpful to identify the (many) trouble areas and come up with creative solutions for mounts, exhaust & turbo routing, etc. I have enough confidence in it now to design parts and send them out for laser cutting without making templates first.
The other bonus is when it comes to cutting sheet metal out of the car, I know exactly where and how much to take out to get the clearances I want first cut.
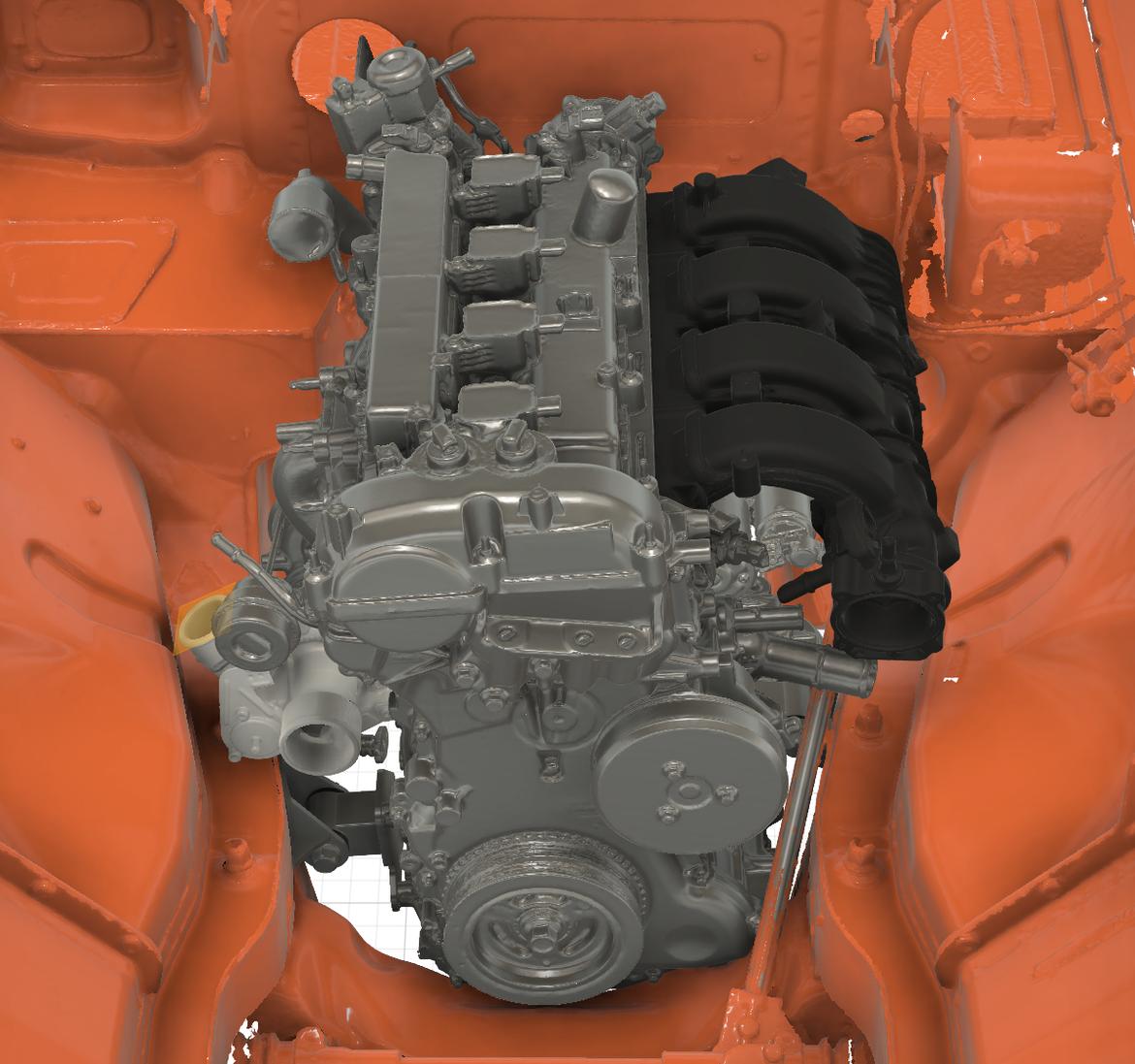
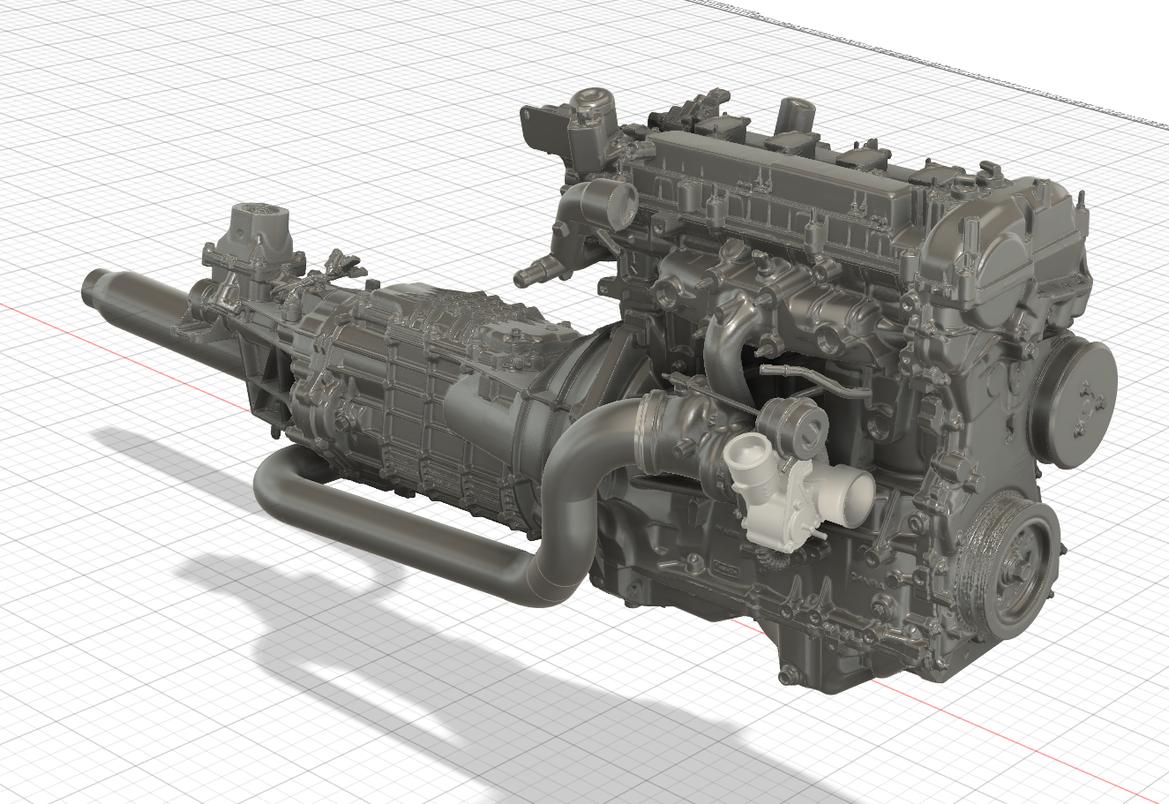
enginenerd said:
I've used an Einstar scanner to scan most of a car and design powertrain swap related parts in CAD. It's been shockingly accurate, even with the accumulated error of me assembling individual components/scans in CAD. Since I have more time available at a computer than in the garage, it's been really helpful to identify the (many) trouble areas and come up with creative solutions for mounts, exhaust & turbo routing, etc. I have enough confidence in it now to design parts and send them out for laser cutting without making templates first.
The other bonus is when it comes to cutting sheet metal out of the car, I know exactly where and how much to take out to get the clearances I want first cut.
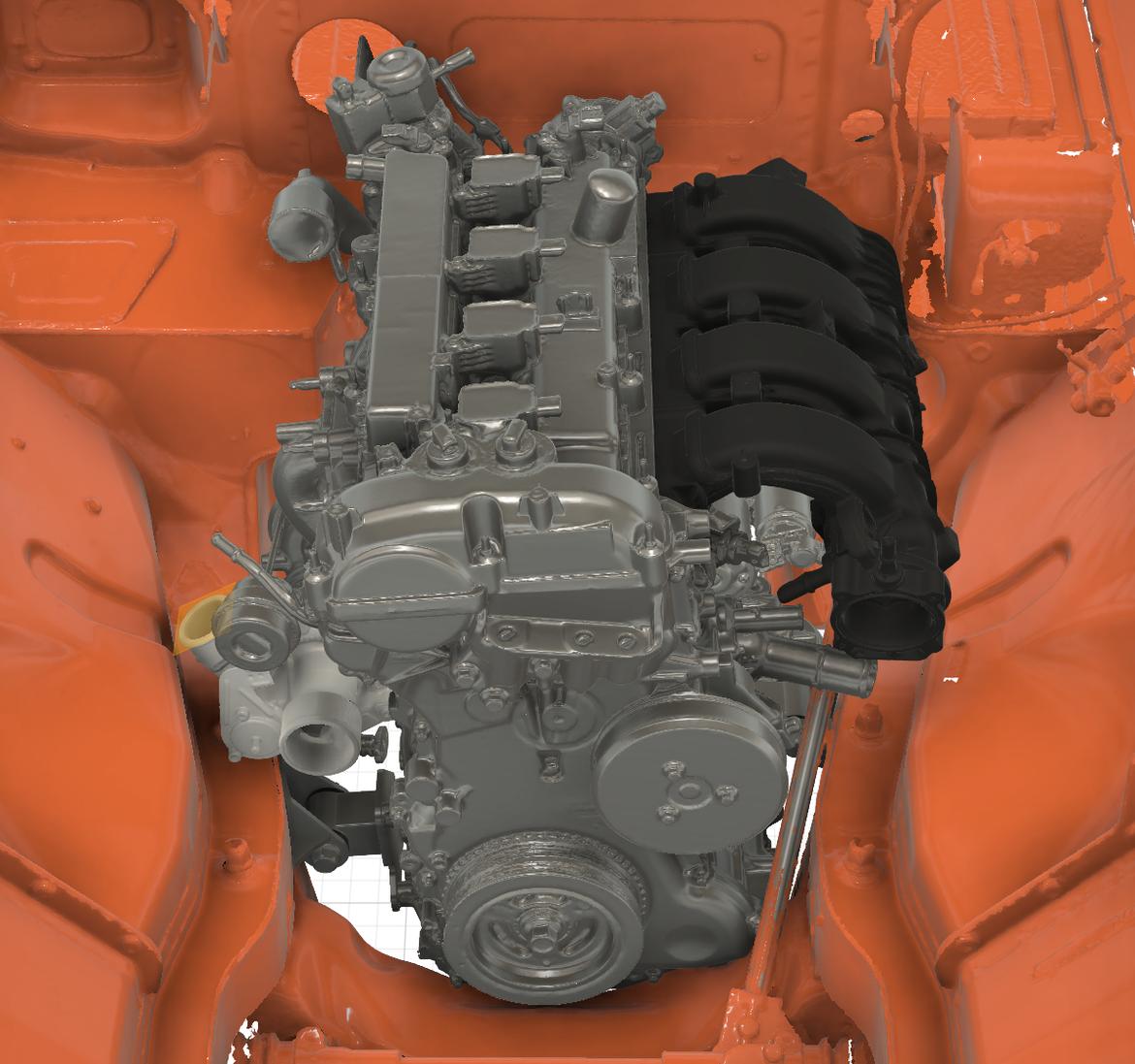
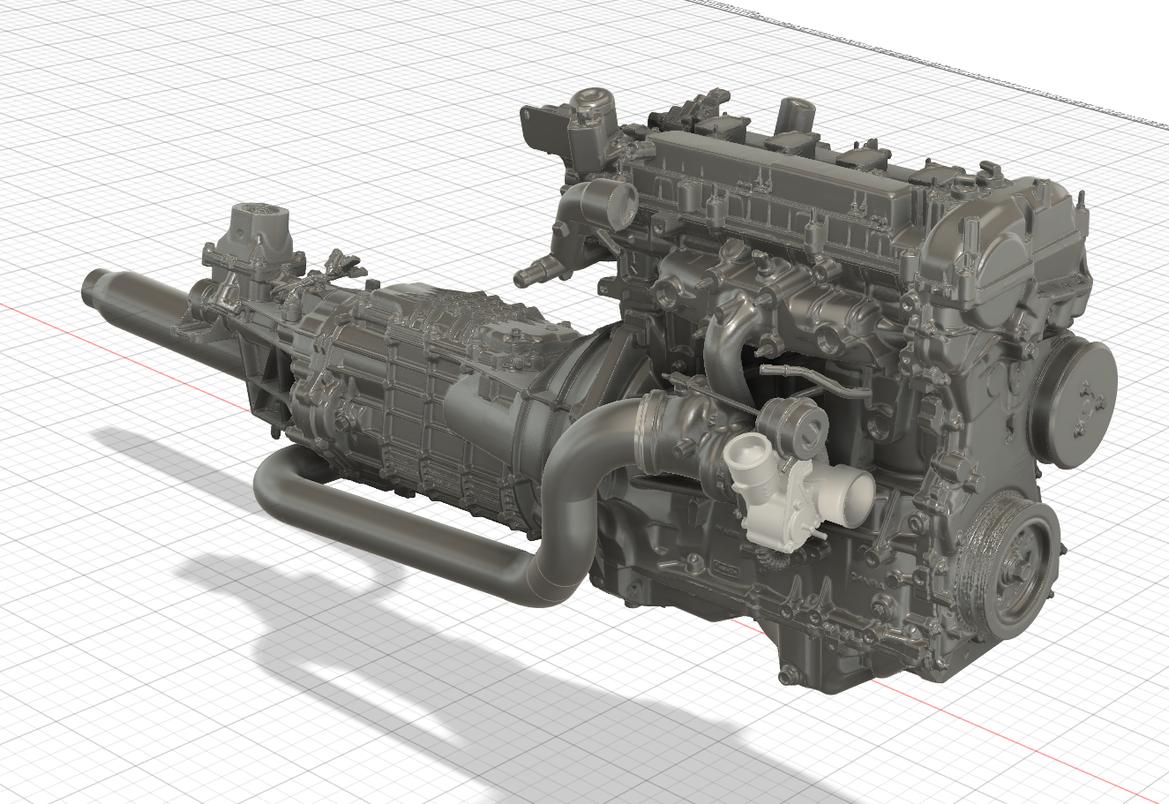
Which model are you using?
Mr_Asa
MegaDork
12/20/24 11:31 p.m.
In reply to APEowner :
The Einstar Shining 3D, it was around $700. You do need a decent computer to run it, but I got by on something pretty basic. I think they released a newer standalone scanner but I haven't tried it.
In reply to enginenerd :
Thanks. Those are pretty amazing results for such a relatively cheap tool.
In reply to enginenerd :
Great, now I own a 3D scanner too.
I have poor impulse control.
In reply to enginenerd :
That's some spectacular output quality. I've never seen our guys at work do that well with our various scanners but they do tend to focus on just the area of interest for the moment and not the complete engine/engine bay. Well done.
In reply to brandonsmash :
I see no problem here...
Keith Tanner said:
In reply to enginenerd :
That's some spectacular output quality. I've never seen our guys at work do that well with our various scanners but they do tend to focus on just the area of interest for the moment and not the complete engine/engine bay. Well done.
Thanks Keith! High praise coming from you. I'll never match the quality nor awesomeness of your MGB GT project but your build helped start the "what if I..?" thinking when I was looking at the engine and car sitting around in the garage.
NOHOME
MegaDork
1/3/25 2:49 p.m.
In reply to enginenerd :
I think Keith belongs high up in the list of "Bad Influencers" on this board.
Pete
My Einstar Shining3D arrived today. I bought it from the manufacturer on Amazon in "used - like new" condition for $600. It arrived brand-new in an unopened box. There's one left if anyone's interested!