I've a garage that was built many decades ago, probably in the 1960's, and it was built with a floor made of multiple slabs. They've pitched a little and spread a little. Worst spread is about 1.5 inches wide which is great at swallowing bolts and small sockets. And there's one slab that's about a half or more inches taller than its neighbor, leaving a ledge to trip over.
I'm not entirely sure what the most correct way is to fix this. Cut the slabs up and haul out and have a new floor poured? I'm not interested in the hot mud solution that I've heard about for this kind of thing. And I'm sort of facing some budget challenges coming this year with some other home projects and some other things. So I come here looking for feedback on a couple ideas and maybe get some product suggestions.
Thoughts on me cleaning out the spread joints with a shop vac to try and get as much junk out of there as possible and then using Quikrete to fill those gaps and pouring some out to try to smooth out the low areas to lessen the difference in heights between the high and low areas?
To try and make this bodge job a bit nicer and maybe last a little longer, are there any affordable-ish snap-together garage flooring solutions that can bend a bit and conform to a not so great flooring surface? I think that kind of thing would make this a lot nicer overall but I don't know if there's a go-to flooring to look at first.
If I can get five years out of this sort of fix, that's great, and at that point hopefully I'll have funding to change the floor professionally assuming I'm still in this house by then.
There are a lot of concrete floor leveling products on the market that could possibly work. Many you mix to about the the thickness of a slurpee and pour and it self-levels. A problem may be getting it to bond to the old surface. But, might be worth a try. You can get a reasonable amount of those products for your use for $50 to $150.
I have had good experience with them in residential use, not sure how they would hold up to car weight. But can't be any worse.
Google "Concrete floor leveler"
In reply to Purple Frog :
I looked up concrete floor leveler and the issue here is how big the differences in height are at their worst + the gaps between some of the slabs. It would have to be really thick, thicker than what I see recommended for floor leveler. I think for now I'll pour concrete into the gaps and if I still want to really level the floor, look for some bids on a more professional repair. I was seeing about $1500 in floor tiles at minimum and that seems like a lot when it's really not the right way to fix this.
SV reX
MegaDork
3/15/25 7:02 p.m.
I'm not sure what "hot mud" is, but mud jacking does work (lifts the slabs back into place and fills the void underneath).
There are different products and techniques. One is a soil/ cement solution that is pumped in under pressure. Another is an expanding foam product.
It's used frequently in commercial applications. I see no reason to not consider it for residential application.
SV reX
MegaDork
3/15/25 7:04 p.m.
Do you want level, or flat?
Most of the self leveling products are extremely viscous. They pour in liquid form. They don't work well to make something flat (when it's still out of level)
SV reX
MegaDork
3/15/25 7:12 p.m.
Inexpensive approach...
I wouldn't worry about level. Close the gaps and eliminate tripping hazards.
Vacuum out the large gaps and fill with Top and Bond or hydraulic cement. The skim over the patch with floor patch (sold in flooring dept). It bonds to both wood and concrete, and feathers well to zero thickness.
For unlevel spots up to 1/2" or so, just feather it out with the floor patch.
Let the floor patch set up for a few minutes, then just before it gets really hard use a scraper to "cut" the ridges and imperfections flat.
On the trip hazard you could move over 6 inches and cut out a bigger chunk. That would allow you to ease up on the height difference with a slope.
NOHOME
MegaDork
3/15/25 7:40 p.m.
Pic of what we are fixing would be helpful.
Surface area?
What is a reasonable budget for this project?
Traffic/load?
People give away driveway pavers if you look, so maybe smash the high points, a layer of bedding sand to bring up the low points and lay out 12X12"pavers in the space. Or whatever you can find for free. It is a lot of work.
I thought of the industrial rubber flooring with maybe a filler underneath, but I think you are mostly looking for "free"?
Used conveyor belts are cheap / free. They would do a good job of covering the floor.
For the 1/2 "step" can't you just grind it down to get rid of the trip hazard?
I have used some epoxies to fix concrete floors and they worked fairly well, but can be expensive. I don't mean epoxy floor coverings, but actual epoxy that fills holes or sticks concrete together.
Lot of replies since I last checked this thread which I really appreciate. I took some pictures this morning to show three symptoms of what is going on with this floor that I'm most not-pleased with. All of this is caused by the outside of the floor slabs sinking relative to the center, and one side (south side of the building) is worse than the other. The foundation/footing (I'm going to use improper terminology probably again here and there, this isn't my field at all) seems fine and the building structure & walls etc seem pretty stable and the building is fairly square based on discussions I had with a crew that re-did the siding and changed out a door on the back wall from a 1-car to a walk-through (the one-car was probably installed by a previous home owner and was not done at all well and I really don't think I'll miss it)
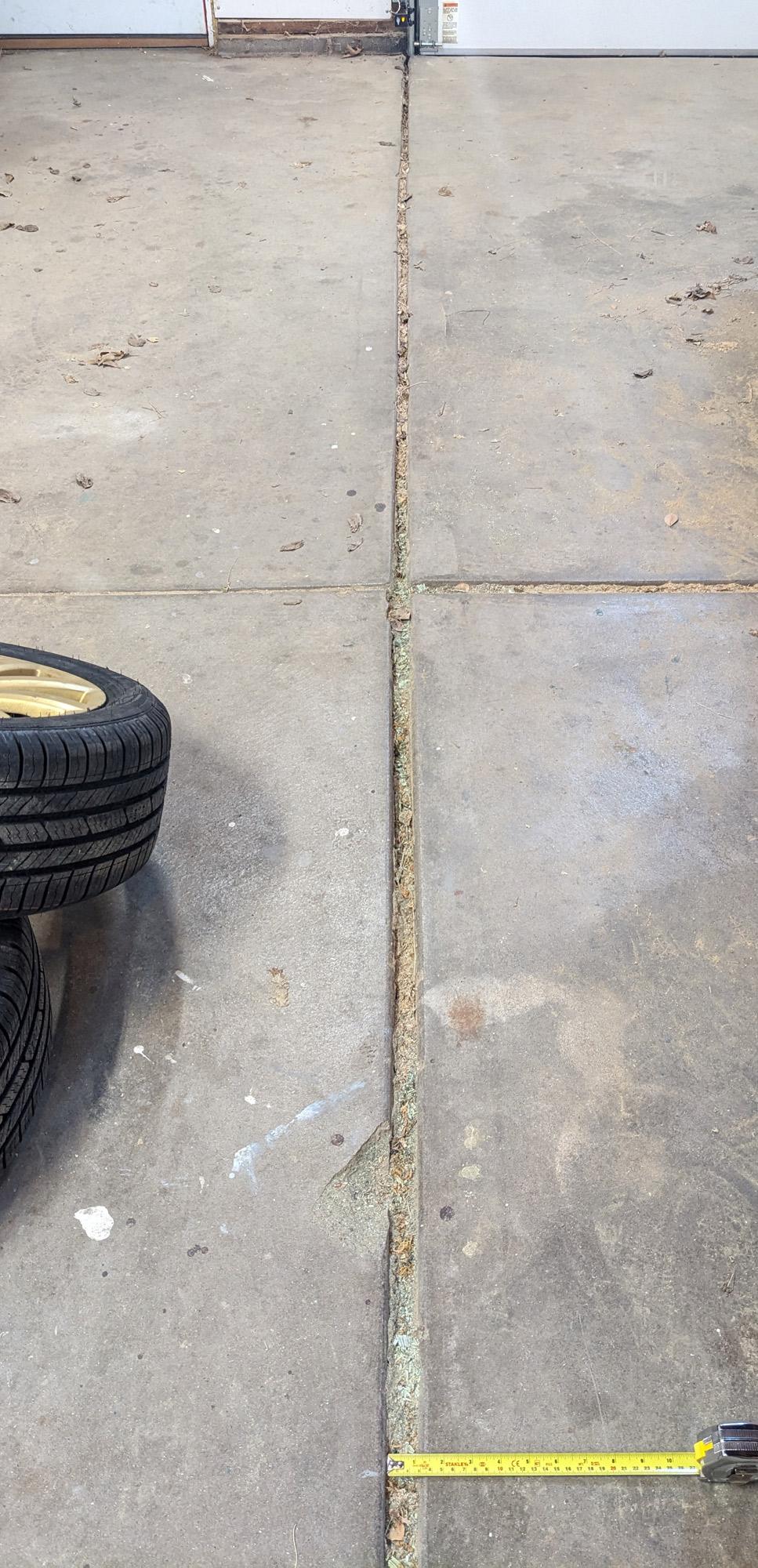
Here's the worst of the spreading that I'd like to fill in.
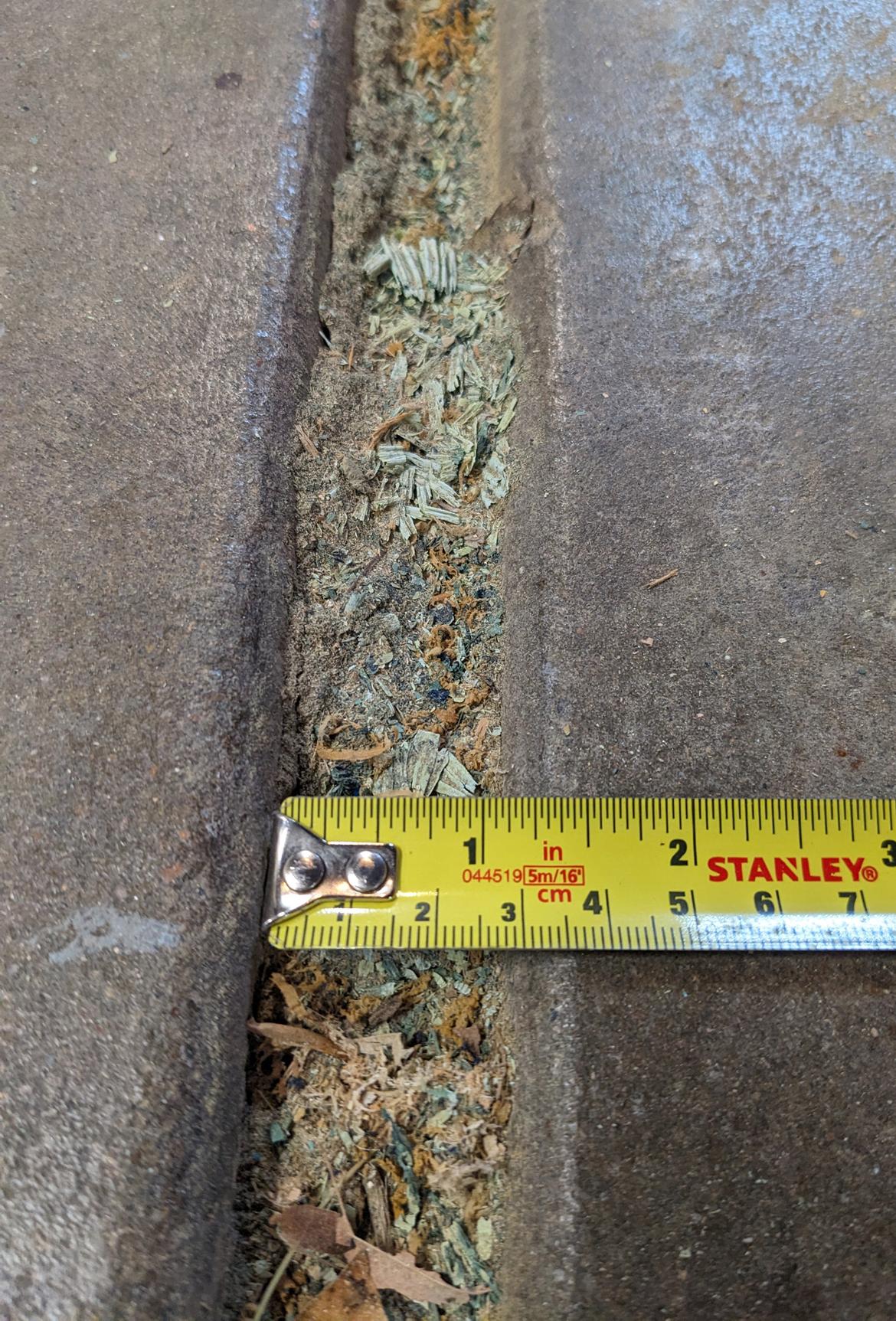
Then we get to the pitched slab that I mentioned would be a tripping hazard and really all-around hassle rolling things over.
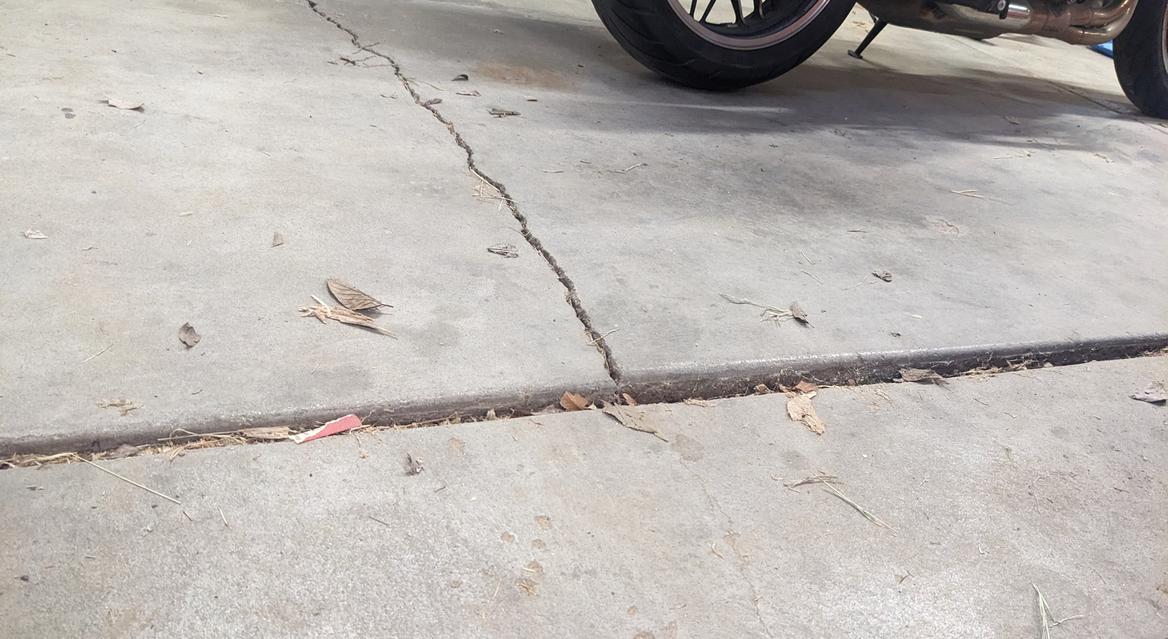
This is the worst area for this. This is also towards the south, so the other side of the same slab in the first two pictures.
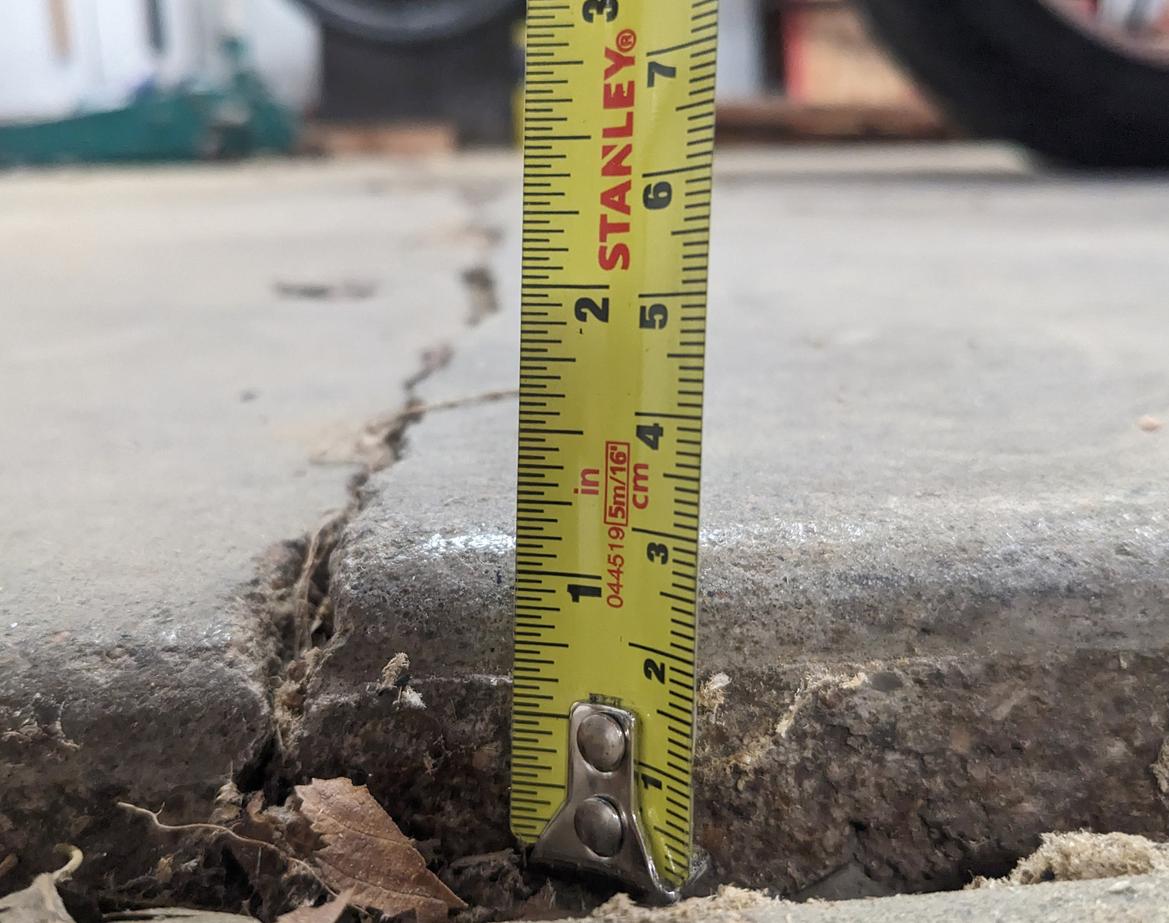
Finally we have the door that, due to the floor sagging more towards the south end of the building, is not able to seal against the floor at the door opening.
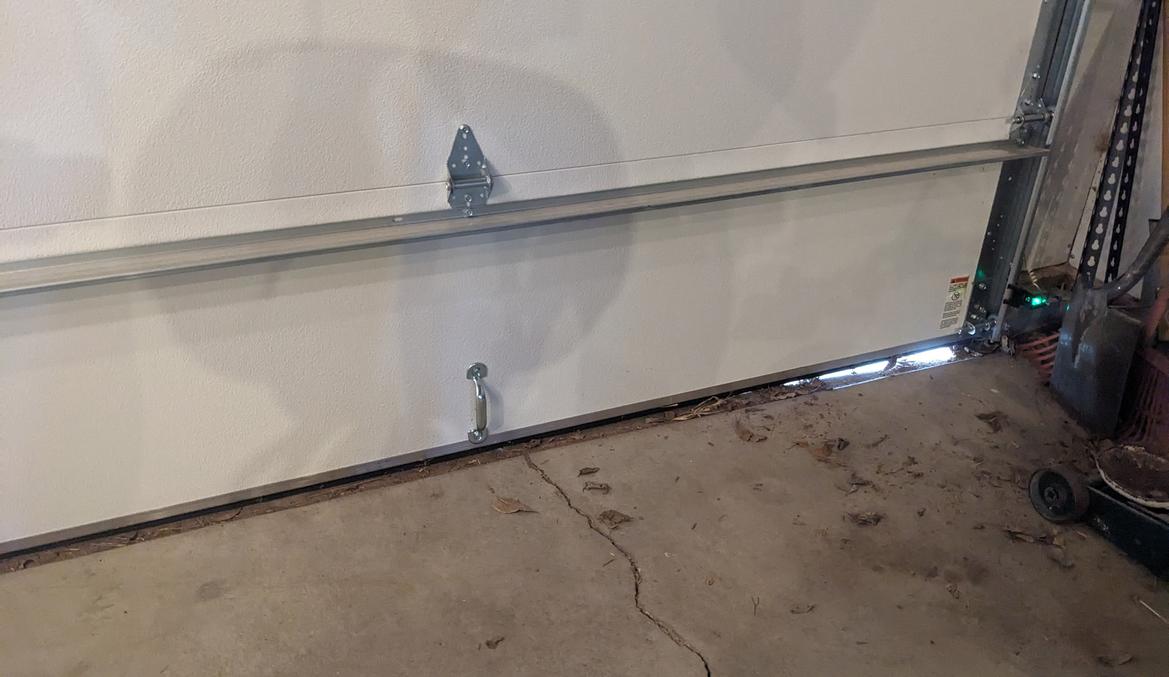
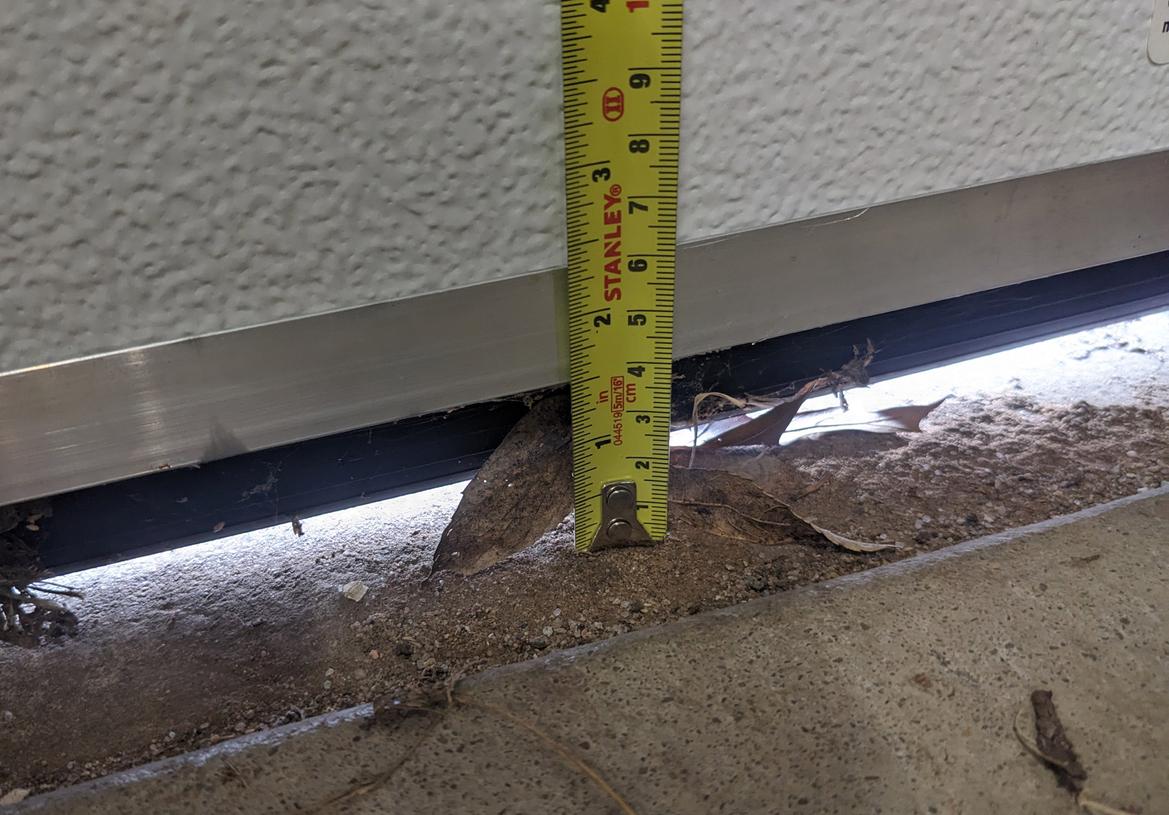
The previously mentioned mud jacking (not sure why I thought it was called "hot mud", sorry for the confusion) seems to carry some mixed opinions. Access to the south side of the building is made worse by it being about a foot from the neighbor's property line, and a fence (which I own and honestly is planned to come out at some point anyway) but if that makes the most sense maybe that's a route I could take?
Really curious what folks think my best options are with these photos to reference.
In reply to NOHOME :
You asks some great questions.
Surface area? About 900 square feet, 24 ft wide by 38 feet long, rounding up slightly.
Reasonable budget? Depends on how permanent/good the fix. I was thinking a couple grand to just fill in bad areas and then PVC tile over it, but if there's a way to fix this properly I could be talked into a few grand more.
Others asked about grinding and yes, I think that's probably part of the solution if I don't have someone come cut out the floor and pour new. I'm also not looking for perfectly level, my first thought was being able to roll carts or a car dolly through the building without it being a huge pain, as well as losing things into gaps in the floor.
NOHOME
MegaDork
3/16/25 10:55 a.m.
I might be inclined to rent a concrete saw and cut out the worst of the bad bits. Where there is a crack you could cut it out bigger so as to make a more stable repair. Not hard to mix up concrete in wheelbarrow or rent a mixer.
Then tile over the lot.
This is a textbook case for mud jacking - they also have a less invasive version using some sort of poly/epoxy mix. The difference is in the size of the holes they have to drill.....for mud jacking I think it's about a 2" or 2 1/2" hole, for the poly stuff it's more like 1/2-3/4". Of course in both cases they grout the holes in once they're done.
Poly is more expensive, but both work. I had quite a bit of mud jacking done to my driveway a number of years ago and it's held up fine. I think they use a bentonite mud mix, it cures out like concrete.
You might look to see if you have a chipmunk infestation, they burrow under driveways and garage floors and that's what cause them to drop. If you do, fixing the floor now will result in it sinking somewhere else as they move the burrow to another spot. In my case they were under the driveway and it had subsided almost 6", when I fixed the drive they moved in under the garage floor. Farking bastiches!
I think for a garage floor I would use the poly version......but if you have them you have to get rid of Chip and Dale or the problem will be right back.
In reply to MiniDave :
Thanks for the feedback. I hadn't thought about rodents but I can go looking. I think there's probably some drainage and negative grade issues in some of the area around the garage so I'll be looking for improvements there as well. Got new gutters and downspouts about a year ago so that's done but I'm sure other things can be improved upon.
I'll go looking for local companies and get a few quotes as soon as I can.
Thanks everyone who have asked questions or otherwise contributed so far.
Don't need mud jacking. There is a hydronic pressure issue or tree stump that pushed up and cracked the slab. The rest of the floor looks fine. If it was me I'd remove the raised section and repour just that part.
The gap on the door isn't even related to the garage floor. It's related to the driveway slope. A bigger flanged door seal would solve that issue.
With the gaps in between the slabs. What they do at most jobs I've seen. Is they clean them out and then stuff the round foam filler into the crack. Then pour flexible epoxy on top of that. The epoxy is at most a 1/4 inch thick. Depending on how thick the slab is they might stack a couple of those in the crack to build it up to just roughly a 1/4 to a 1/3 of a inch depth.
Which ever you do it's not going to be cheap or easy. Reasonably priced is what I would say. Also not that difficult of a job either. Best for the younger kids as being in my 60's that's got pain written all over it for me.
I wouldn't think the self leveling stuff would be strong enough/thick enough to last in a garage?
SV reX
MegaDork
3/18/25 7:59 a.m.
In reply to brad131a4 (Forum Supporter) :
That's an interesting thought. I agree that a couple of those pics look like the slab may have heaved (not settled). If that's the case, mud jacking won't help. It would have to be cut out and re-poured (as you noted)
(I think you meant hydraulic, not hydronic)
If it's heaved, there's a good chance it's frost heave. Especially if that joint is near the door.
@pres589: Is it heaved, or settled?
Crack Stix is designed for larger cracks, put the product in and heat it with a propane torch. I have no personal experience, but it seems ideal for what you want to do. $100 for a 125' bucket.

Home Depot rents a 10" concrete grinder for $160 for 4 hours. Knock down the high spots, then fill the cracks.
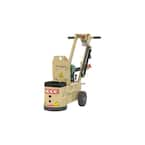
If you want to level the corner near the door, grind the surface a bit, build a V-shaped form, then pour a self-leveler and feather out to meet the slab. 1" depth is fine without aggregate.
In reply to SV reX :
You know, I think heaved is what is going on, now that's it's been mentioned. Grinding has been mentioned, which would smooth things to a degree, but only as the edges really unless I want to grind out the middle slabs where the floor is at its highest. And then it's thinner so I assume it might crack up faster in the future.
Filling the gaps with a foam product as brad131a4 mentioned and then pouring flexible epoxy over that to get a flat fill sounds doable. Anyone know of a product name for these items?
pinchvalve has some suggestions I like; grind down the worst of the pitched edges and around that low spot at the door, then build a form and pour some self-leveler in to build that area back up under the door so the gap goes away.
So basically I'm thinking grinder for the high stuff and to prep the area under the door, self-leveler to build that area back up under the door, and foam & epoxy to fill the gaps. Just need to figure out what those products are and get a day to get it done. As always, thanks for the input everyone, and any other ideas or input is of course welcome.
SV reX
MegaDork
3/19/25 7:06 a.m.
If it's heaved because of a root, be aware that roots keep growing. Grinding may work for a while, but cutting it out and re-pouring is the only way to get rid of the root.
In reply to SV reX :
The closest tree to the garage was in my back yard, was close to the building and sending roots under the driveway, and I had it cut down two years ago. There's a tree in a neighbor's back yard but it's probably 25 feet away from the building and is to the south of the building; I don't think that tree is affecting things, but I could be wrong. Still, the main tree is out of there now.
I see this as a patch job to make the building nicer for the next 5 or so years.
Diamond tiles are durable, snap-together garage tiles that allow for drainage and are somewhat forgiving on uneven surfaces. I would go with them.