I have an older Dayton 80 gal compressor that has a fresh motor and generally works well. It's in a little mechanical "nook" off of my house's attached garage, which is also where I've got my tire machine. We air up bike tires, kids toys and car tires from there as well. (So that compressor probably needs to remain there.)
I've since built a detached shop about 75 ft away, and ended up with a 3 phase compressor that's sitting out there, but no 3 phase power. Rather than spend $500 on a single phase motor, could I just use that tank as a receiver tank and bury a line from house to shop? If I did that, I'd likely use PVC. I know it's a bomb and all, but it would be buried. My buddy actually has a very analogous setup with remote compressor piped underground to his shop with PVC and it's been fine for a decade or more.
Just looking for reasons for or against that plan vs new motor vs maybe some options I haven't considered.
Thanks!
NOHOME
MegaDork
5/11/24 9:51 a.m.
Can't think of any reason not to do what you plan. Once, when my main 50 gal compressor failed in the middle of a paint job, I used a rented compressor with a smaller tank to hook up to the large one and finish the job.
Question I have is: Why do you need the tank in the shop if you have the airhose from the other shop?
You need the tank in the shop to be able to maintain CFM. There will be a certain amount loss of flow due to length of pipe, unless the pipe is fairly large. OBTW, the pipe becomes more storage capacity.
One issue would be how much condensation builds up in the pipe underground.
The shop 3p compressor was bought as a package with some machine shop tools and I don't guess I need it at all, but it's there. Figured it'd be a buffer tank. And the 75ft figure from shop to garage is face of building to face of building. The run to get a hose to use in shop from house would be 100'+ and the run of pipe will likely be that long to reach one of the sleeves I put in the foundation. Figured both would represent less than ideal pressure loss, but at least running pipe to other compressor I've got some volume of air waiting on me.
I also keep reminding myself that time is money and a motor swap is an hour and $500. Figuring out fittings, hoses, piping and digging associated with said pipe might be cheaper, but it'd probably take me a weekend.
In reply to Oapfu :
Best idea, right there.....I used VFD's in the opposite configuration too - I had 3 phase power all over my plant and very little single phase, when I needed it I used one of these. They were cheaper than a transformer and easier to wire.
Depending on the HP required, they're fairly inexpensive.....
Preface: I am an industrial maintenance technician and one of my jobs involves air compressors. I am no expert but I am competent.
The remote slave system works well in certain situations. Moisture control is very important. Get an automatic moisture control system on each end. When I use a secondary remote tank system I run 4 tanks, Two large primary tanks and two small tanks. The large tanks run at maximum PSI (My work Atlas Copcos run at 115), the small tanks are each run off of a large tank at lower PSI (generally 90) I suggest using a 3/4 to 1" transfer line minimum for each transfer. We utilize coated aluminum pipe and and specialized connectors on long runs. On short runs we run coated aluminum, steel, and even PEX on occasion.
At home I have a 30 gallon 225psi compressor running at 175psi, filter dryer, regulator, 3/4" line, 125 gallon slave cylinder, another dryer and regulator at 90psi. Ball valves are super important as well.
I'm on the new construction side ("Senior Super Nintendo") for big defense/industrial client. Been doing phases of large x big production facilities for them for 8 years now. They have all manner of compressed air systems, so I oversee it getting done "right" pretty frequently. I don't have the time nor bandwidth to try to do everything "just so" at home. Compressor in the shop has probably been sitting there hooked to nothing for creeping up on a year... Anything I do from here would be an improvement.
Thinking VFD might be the play. Just hesitant to buy Chinesium when playing with power.
Somebody beat me to it, but I'll second the VFD option. They're so cheap these days it might cost less than the PVC pipe and fittings.
Both are viable suggestions. VFDs are great to run motors like this. Overflow or buffer tanks are also great; I have one in my shop. It's set up high with filtration on both ends and provides an additional air reservoir for when I'm doing air-intensive operations (milling with coolant, plasma cutting). This also means that if I'm drawing on the compressor, as the compressor is operating I get a smooth flow rather than pulses of air during a high-demand process.
Ok, then let's say VFD is the play. Can someone point to a known-to-work affordable option for this setup (see pics below).
Thanks!
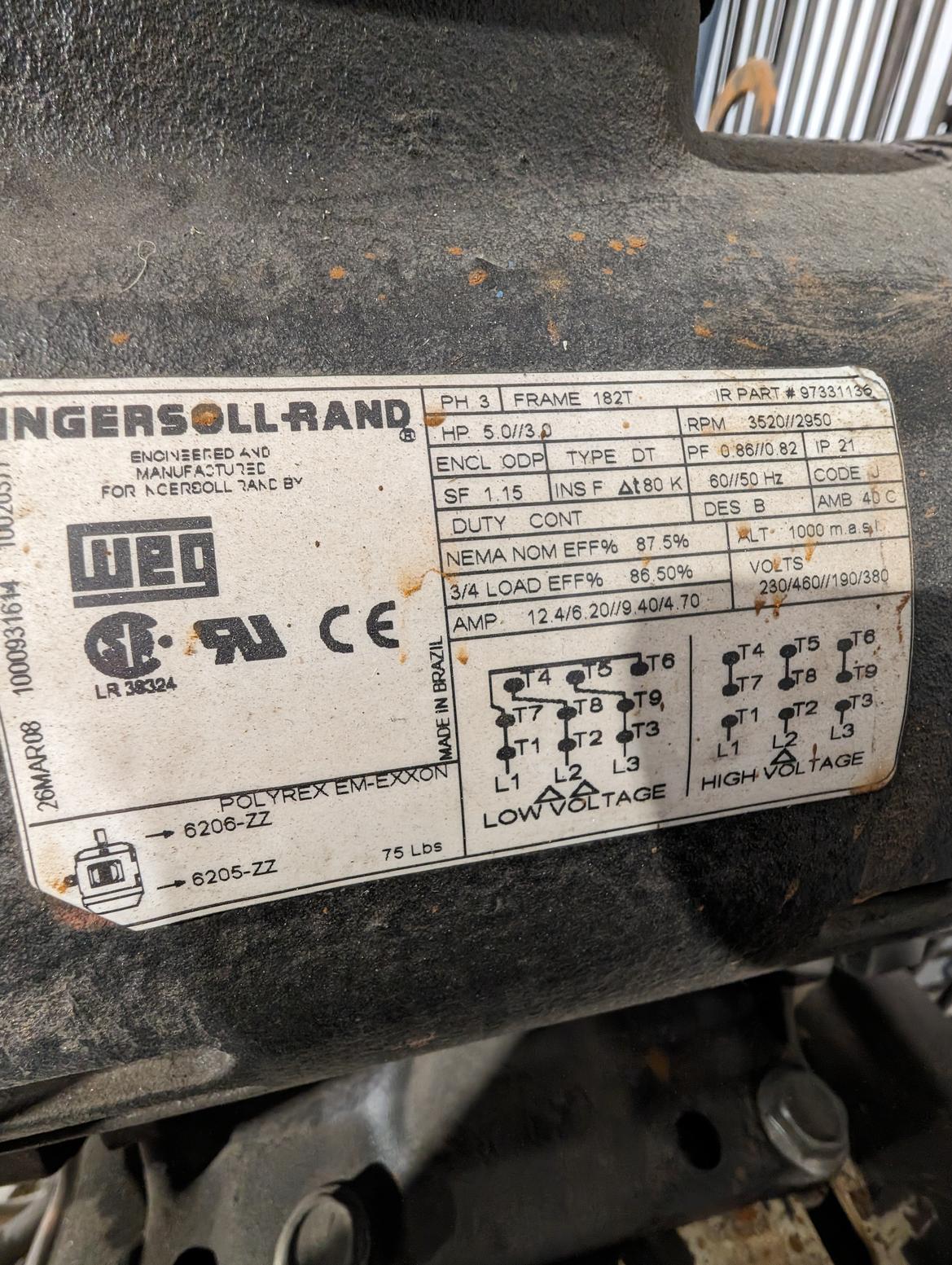
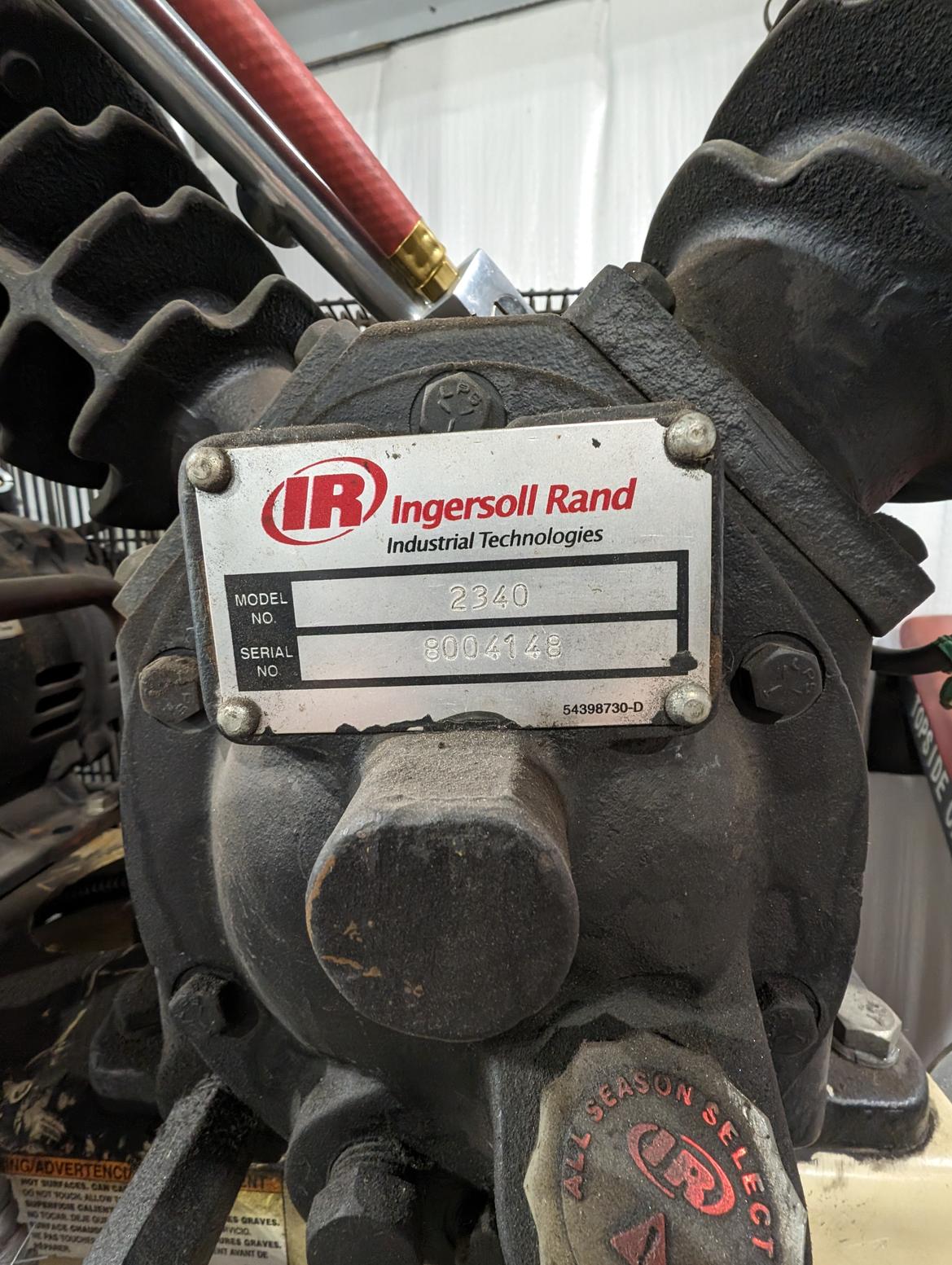
Vevor VFD 4KW 18a 5hp VFD $122 on their site. www Vevor com
Also agreeing with the 1ph-3ph VFD suggestion. The one tricky part might be the control wiring, but it shouldn't be too hard. Basically, whatever control signal from the pressure switch that operates the existing motor contactor will be used to tell the VFD to start. Just make sure the control voltages work. The pressure switch "should" be operating at 24VDC, but it might operate at line voltage. My semi-educated guess is the VFD will want to see a 24VDC signal to start/stop.