Admit it: If you were a kid in the ’80s, you wanted to be like Michael Knight when you grew up. The biggest reason to pine for his job? The company car, KITT.
And in just about every episode, Michael would press the big Turbo Boost button, launching KITT hundreds of feet through the air. Is it any wonder that the words “turbo” and “boost” are so popular with today’s gearhead? Blame the television. It’s what everyone else does.
Adding a turbo to a real car may not propel it through the air—well, unless it’s a rally car—but a turbocharger can turn a mundane economy car like a Civic or Neon into a Corvette-killer. It can also help a classic Studebaker hit 240 mph at Bonneville.
If your car doesn’t run on special effects, then too much boost can be a bad thing. You could blow a head gasket, hit the limits of your fuel system, or overheat the incoming air so much that you actually lose power.
The goal is to maintain a level of boost that provides the desired power while limiting the risks to the engine. Remember, your idea of an acceptable level of risk may not match that of warranty-conscious engineers.
There are several ways to limit boost. The size of the turbine can be reduced so it can’t spin the compressor fast enough to reach unsafe levels. However, turbos of this type tend to be sluggish and unresponsive. Intake restrictions can limit boost—and may be required by racing series rules—but they force the turbo to work harder and can also overheat the incoming air.
It’s possible to control boost by using a bypass valve to vent excess pressure before it reaches the throttle. This requires compressing more air than is used—not a good way to control boost.
Some novice turbo users get the impression that the compressor bypass valve, sometimes called a blow-off valve, is what controls boost. It actually doesn’t set the boost level—or, at least, it shouldn’t. The real purpose of a bypass valve is to control pressure spikes that happen when the throttle is snapped closed.
Properly controlling boost isn’t that hard provided you understand the hardware used: the wastegate as well as various mechanical and electrical controls.
The Wastegate: Some Control, Not Much Thinking
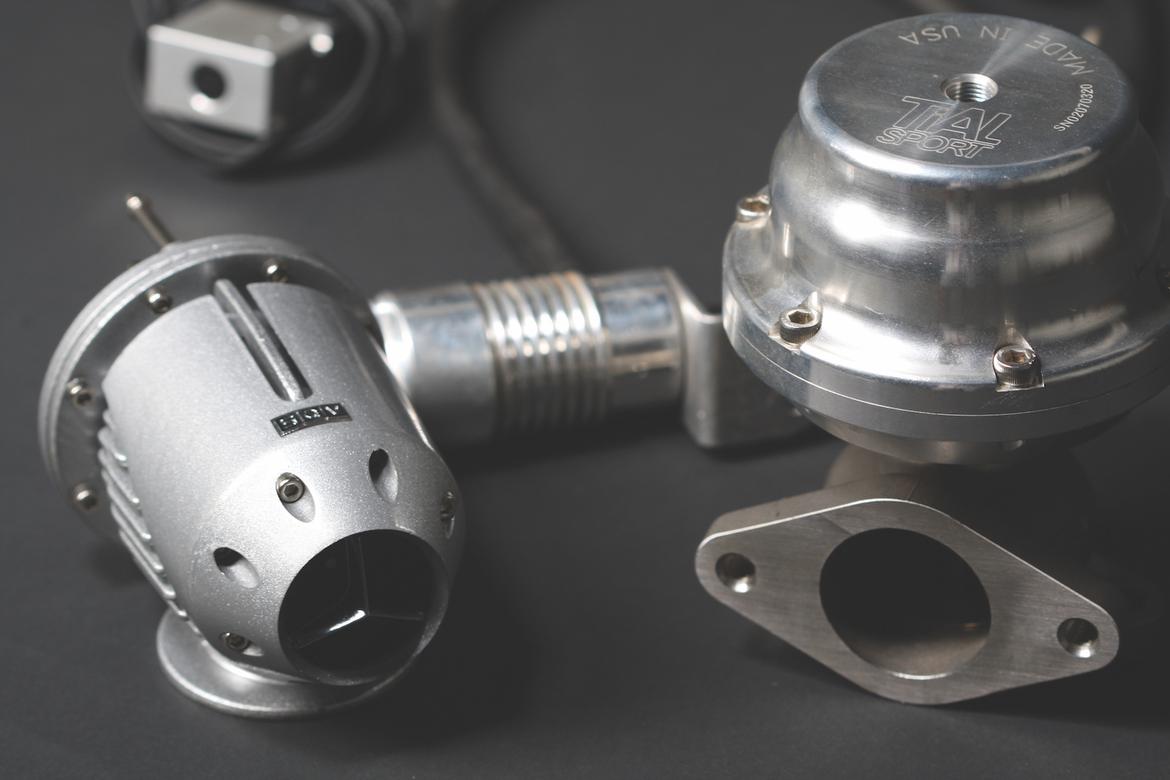
A blow-off valve (on the left), sometimes called a compressor bypass valve, has one job: preventing pressure spikes in the system when the throttle is closed abruptly. A wastegate (on the right) regulates the amount of boost pressure that’s allowed to make its way into the combustion chambers.
Except for a few very cutting-edge turbos, most systems seen on modern cars control boost with a device called a wastegate. The wastegate is fairly simple: It’s a valve that lets the exhaust gases go around the turbine and straight into the downpipe. The further the valve opens, the less exhaust pressure is available to drive the turbine and make boost.
Normally, a spring holds the wastegate closed. Air pressure from the turbo outlet pushes a valve against the spring. The amount the valve opens is determined by how far the pressure can push the spring; the spring is often preloaded so that it requires a set amount of pressure before the valve starts to open at all.
A wastegate can be built into the turbo, in which case it’s called an internal wastegate. If it’s built separate from the turbo, it’s known as an external wastegate. Internal wastegates are less expensive to build and make packaging easier, but external designs can flow more.
Running too much boost or installing a turbo that’s too small can overwhelm a wastegate, however. It’s possible to get so much exhaust volume that even a fully open wastegate won’t prevent runaway boost. The fix depends on the wastegate type: Internal wastegates can sometimes be ported to allow more flow, while external wastegates can be replaced with larger units.
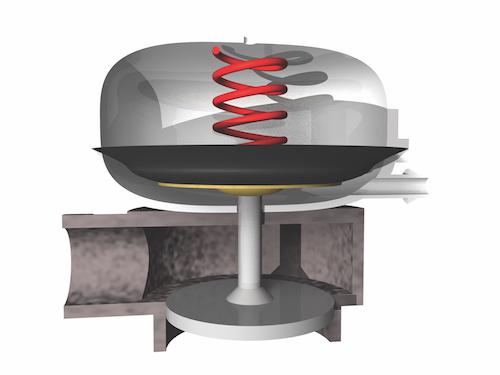
Mechanical wastegates are simple devices: The spring strength determines the target boost level.
The wastegate can serve as a boost control device on its own without any further control devices. Simply pick the spring so that it starts to open just below the desired boost. Once too much boost is generated, it pushes open the wastegate far enough to reduce the turbo speed and bring the boost down to the target level. This is simple, inexpensive and effective.
Simple, inexpensive and effective doesn’t mean it’s right for every application, however. A wastegate without any more control devices will open somewhat before peak boost is reached, slowing down spool times. Also, there’s only one way to adjust the boost: Wait for the wastegate to cool off and swap in a different spring. Fortunately, there are several ways you can get more control over boost.
Mechanical Boost Control: Inexpensive Yet a Bit Primitive
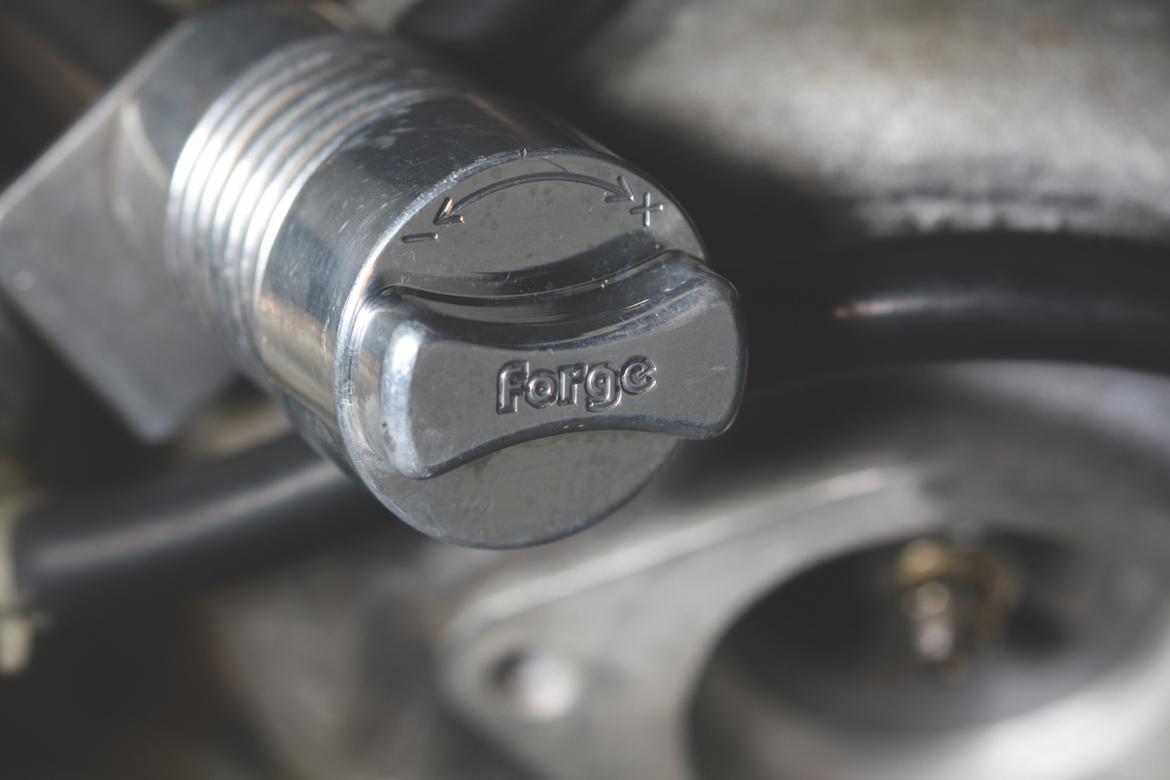
Mechanical boost controllers give the driver the ability to adjust peak boost levels.
The simplest type of boost control is a bleeder valve that releases a controlled amount of pressure from the wastegate line. This prevents the wastegate from opening until the turbo reaches a higher boost pressure than its spring would normally allow.
It’s possible to whip up a bleeder valve boost control using a simple tee and an aquarium valve; this used to be a popular trick for raising boost when replacing the wastegate spring wasn’t an easy option. However, this solution tends to suffer from significant lag and can change boost depending on altitude and air temperature. Now that superior control devices are showing up at very low prices, the bleeder valve has started to fall out of favor.

The bleed valve is a simple and inexpensive mechanical boost control mechanism; it bleeds off pressure before the compressed air reaches the wastegate, effectively tricking the system into reaching higher boost levels.
The ball valve boost controller is a major improvement over the bleed valve. This simple mechanical device is plumbed into the wastegate line; it only lets pressure through to the wastegate after it hits a preset level. Below this level, the valve vents out the boost and keeps the pressure off the wastegate actuator. A screw inside the valve is used to adjust the set point.
The ball valve is also a much more responsive type of boost controller. Because it only opens when the target pressure is hit, it cuts turbo lag to a minimum. While there is often a small amount of overshoot—the valve takes a little bit of time to open up—it is very good at holding a constant level of boost.
Ball valves are also quite inexpensive. Some versions are known as Granger valves because they can be pieced together with parts sourced from an industrial supply store. Today, valves built specifically for boost control can be found for similarly low prices.
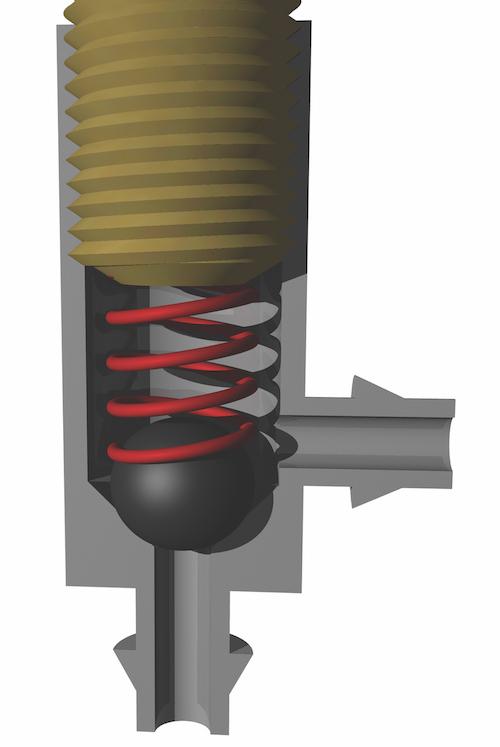
A ball valve-type boost controller has the same job as the bleed valve, but it’s a superior mechanical design that only vents pressure to the wastegate when the boost hits a preset level. At that point, the pressure is routed to the wastegate.
These control devices do have limitations as to how far they can raise boost, however. Eventually the pressure in the exhaust manifold builds up to the point where it forces open the wastegate even when no pressure is applied to the diaphragm. Once that point is reached, the wastegate needs a stiffer spring.
It’s possible to use a solenoid valve to switch between different boost control devices: one for low boost and another for high boost. For example, a drag car could come off the line under low boost and then switch to a second, higher boost setting for second gear; the result would be a manageable launch plus a faster top end.
However, if you want a more complicated setup, it may be time to put electronics in charge of the boost level.
Electronic Boost Control: More Thinking, More Control
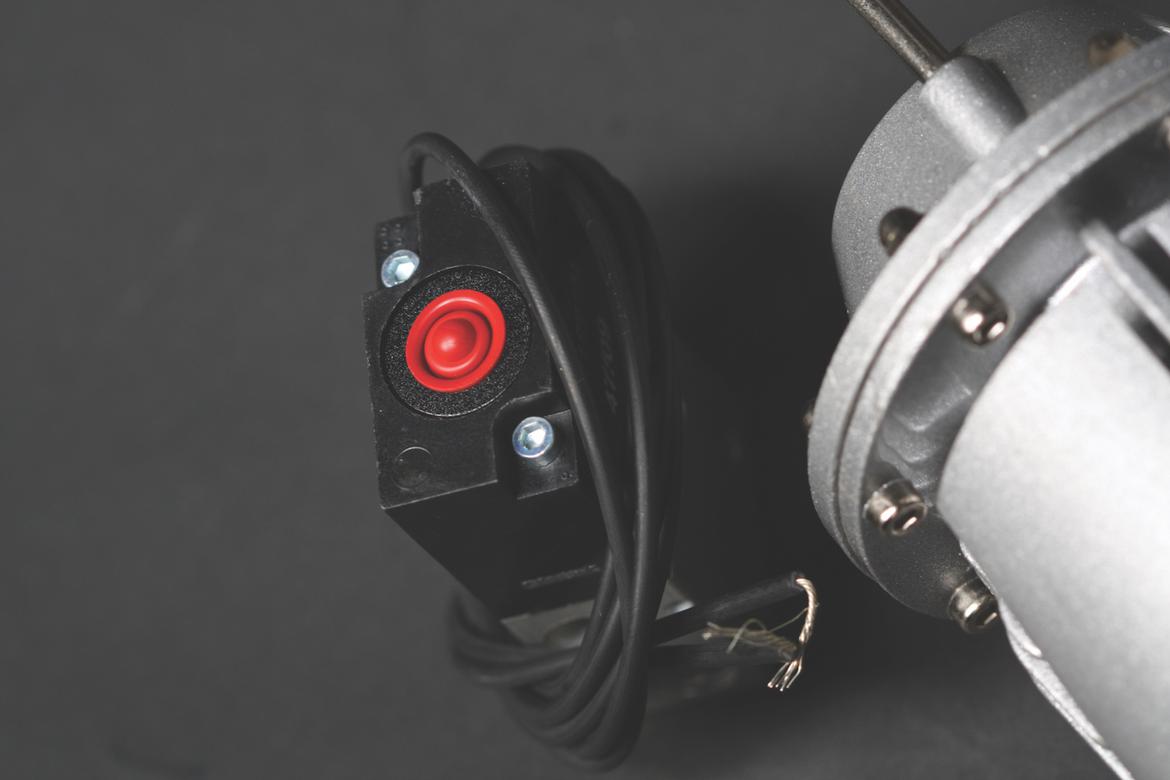
Both ball and bleed valves rely on the boost pressure for their operation, but a solenoid-operated device adds a greater measure of control with the aid of electronics.
Mechanical boost control can react, but it can’t think. While electronic boost control devices aren’t as smart as the AI that controlled KITT, they do allow boost control to carry out tricks that require a bit more calculation.
Electronic boost control can be built as a separate black box or integrated directly into an engine management system, granting it access to all of the available engine sensors. In response to the boost controller’s calculations, these electronics can then command a bleed valve operated by a solenoid or a stepper motor.
The electronics can calculate how much to open the valve using two basic methods: closed loop or open loop. Closed loop determines a pressure to target, looks at the actual boost pressure, and adjusts the valve opening based on the difference between the two. Open loop looks at boost pressure along with many other variables, calculates how much to open the valve, and keeps it there until one of the input variables changes—no matter what the boost pressure is doing.
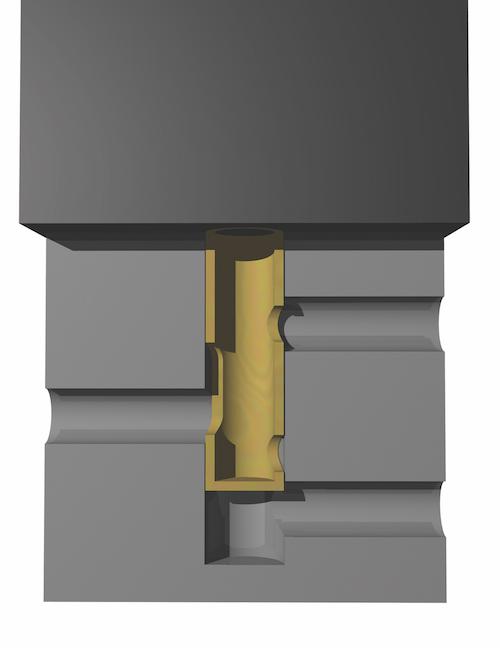
This cutaway depicts a boost control solenoid; it can move the hollow shaft to any position between the two ports, regulating how much pressure is bled off and how much is sent to the wastegate.
As one may suspect, open loop boost control suffers from some of the same weaknesses that plague the simple bleed valve, particularly that it slightly changes boost levels depending on altitude and weather. However, if you give the electronic boost control the ability to change the valve opening based on engine rpm, the simple electronic boost controller can hold the valve open until the engine speed reaches the point where the turbo makes its maximum boost. The result is a bit less lag than with a plain bleed valve.
Closed loop boost control allows you to specify a specific maximum boost, and a well-tuned system will provide rapid spool-up plus the ability to hold the boost exactly where it’s desired. However, when adjusting closed loop controllers for peak efficiency, a couple of arcane voodoo numbers are required. A knowledge of calculus can help with understanding the equations used by closed loop controllers, but what works for one controller rarely works for another.
A poorly tuned closed loop controller can also turn into a nightmare, producing boost that spikes and bounces around like a yo-yo. It’s the familiar trade-off: With more variables to adjust, you may hit just the right setting or get things horribly wrong.
While mechanical boost controllers have just one input—the current boost level—it’s possible to make an electronic boost controller that’s dictated by any input that could possibly be useful for determining boost levels. One of the most common inputs for an electronic boost control is rpm. This allows boost control to be tied to the engine’s powerband. For example, the wastegate could be completely closed at low engine speeds; it could also be operated to add a little extra boost after the engine makes peak power, thus widening the powerband a little.
Another common input is throttle, as the throttle position sensor can tell the boost controller to back off of boost at part-throttle. This is particularly useful if the throttle body is large enough that it isn’t a major restriction, even when still slightly closed.
Electronic boost control can get even more exotic if the budget allows. Some controllers tie in to a vehicle speed sensor to limit boost at low speeds, while others allow separate boost settings for every gear—less boost in first gear but more boost in the higher gears. Another possibility, first used on Saab’s APC system, is to add a knock sensor and reduce boost if it senses detonation.
Of course, not every electronic boost control system is going to have all of these options. If you’ve hacked the ECU of a naturally aspirated car to provide boost control, for example, you probably won’t find much code that’s actually meant to control boost—unless the designers were planning on a turbo option. Instead, you’re more likely to find a bit of emissions control code that can be hijacked to create a simple open loop code based on one or two variables.
Some well-known, expensive, purpose-built boost controls don’t have every feature checked off, either. It pays to both check the spec sheets and ask the opinions of people already running a system. Don’t be surprised if an aftermarket, stand-alone ECU is the best answer; fortunately, they’re not nearly as expensive as they once were.
Lots of Options
These days, there are more options for boost control than ever. If you just need to set a limit and don’t have boost control built into the electronics already present, the best option is an inexpensive ball valve.
This doesn’t mean that more expensive systems are a waste of cash, however, as spending more money can yield more control. You may not get a bright-orange Turbo Boost button on your dash, but a good electronic boost controller will know just when you need that extra boost anyway.
Like what you're reading? We rely on your financial support. For as little as $3, you can support Grassroots Motorsports by becoming a Patron today.